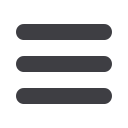
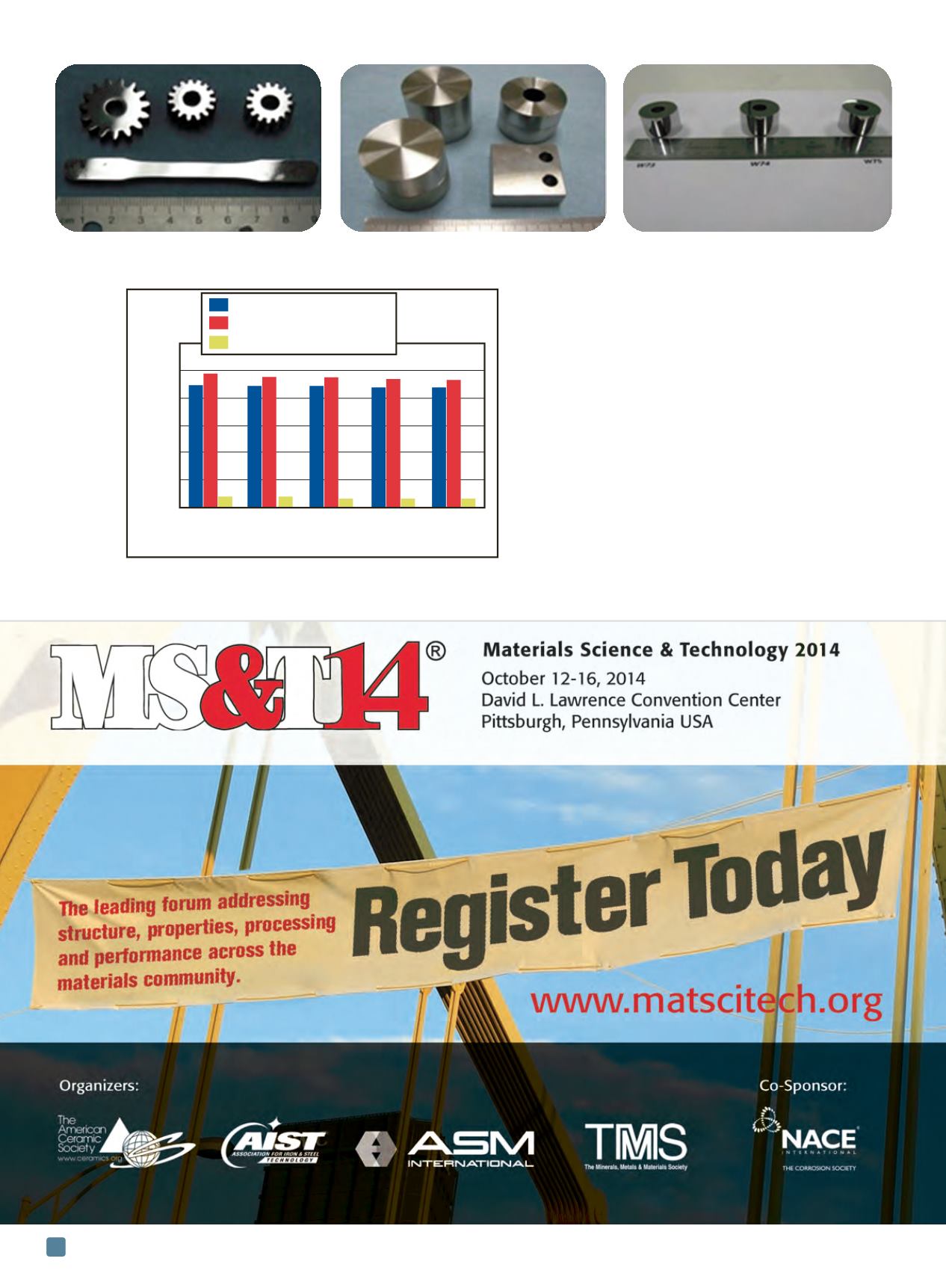
sintered state. Another benefit of high part density is min-
imal dimensional change (shrinkage) after sintering. CDC
optimized high-density PM parts exhibit exceptional prop-
erties equivalent to wrought products in terms of mechan-
ical strength and toughness as well as high temperature
resistance and ductility (Figs. 3-6). The CDC method also
features the ability to press a variety of powder types, in-
cluding composite materials, to yield much higher pressed
and sintered densities than those achievable by conven-
tional lower pressure PM methods.
Future applications
Potential commercial and military applications for
CDC higher pressure compaction near-net or net shape
manufacturing technology are endless. Some examples in-
clude high vacuum grade microwave tube components,
vacuum flanges and fittings, cryogenic compatible metal-
ADVANCED MATERIALS & PROCESSES •
SEPTEMBER 2014
30
Fig. 5 —
CDC compacted and sintered/heat treated advanced stainless steel parts (Custom 465) for naval applications feature
wrought-equivalent properties of 250 ksi tensile strength and 17-25% ductility for improved toughness
[6]
.
(a)
(b)
(c)
2625
(VS+45%
CW+HT)
2486
(VS+HT+
24%CW)
2608
(VS+38%
CW+HT)
2605
(VS+40%
CW+HT)
2600
(VS+43%
CW+HT)
Fig. 6 —
CDC optimized Custom 465 stainless steel exhibits
properties and fine-grained microstructures equivalent to
wrought materials.
Yield strength (ksi)
Ultimate tensile strength (ksi)
Ductility (%)
300
250
200
150
100
50
0
Strength (ksi) and ductility (%)