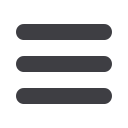
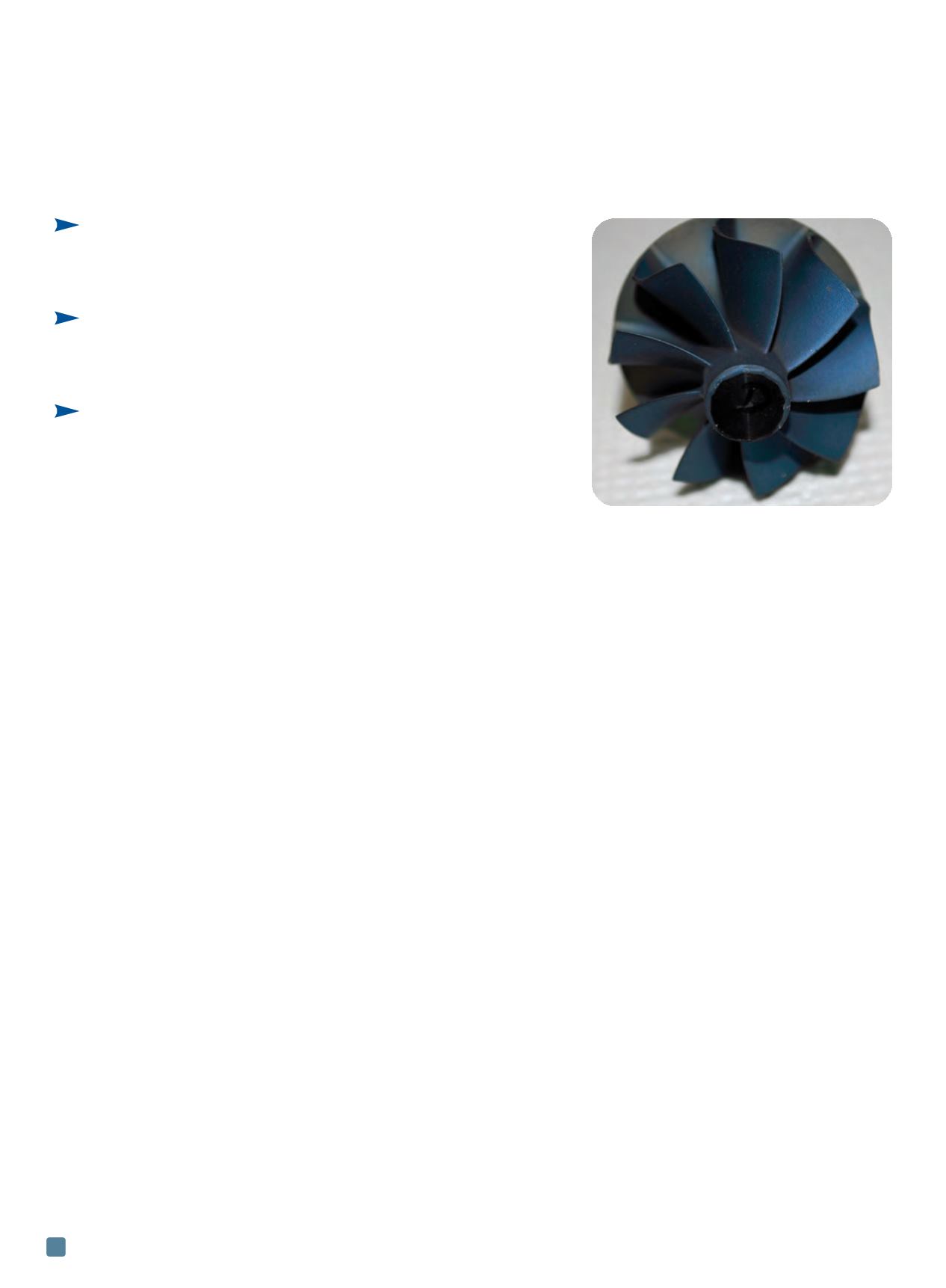
John H. Perepezko,
FASM*
University of
Wisconsin, Madison
Bruce A. Pint,
FASM*
Oak Ridge National
Laboratory, Tenn.
David R. Forrest,
FASM*
U.S. Dept. of Energy,
Washington
ADVANCED MATERIALS & PROCESSES •
SEPTEMBER 2014
22
M
aintaining our current standard of
living will require not only an abun-
dant energy supply, but also one that
is environmentally benign. This reality is moti-
vating the drive toward enhanced efficiency in
energy production. The majority of energy
sources that involve thermal production—in-
cluding fossil, nuclear, and even concentrated
solar power—require increased operating tem-
peratures and materials that can withstand an
aggressive, high-temperature environment for
long periods. Structural intermetallics offer a
number of attractive materials choices to ad-
dress these needs.
A myriad of intermetallic alloy phases are
available, with unique capabilities ranging from
electronic properties (such as permanent mag-
net and thermionic emission characteristics) to
specific chemical behavior (for use in catalysts
and sensors, and for corrosion and oxidation
resistance). However, the use of intermetallic
alloys in structural applications has lagged after
substantial progress in the 1980s and 90s. One
reason is that the fundamental characteristics
that impart intermetallics with exceptionally
high modulus and strength present challenges
to achieving useful ductility and fracture tough-
ness. However, the outlook for structural appli-
cations is changing. As the fundamental
understanding of deformation behavior and de-
fect structure has evolved, it has provided valu-
able guidance to enable advances in alloy design
and materials processing. These advances have
moved some intermetallics, such as Ti alu-
minides, from the laboratory into full scale
structural applications. Later this month, the
structural intermetallics symposium at Materi-
als Science & Technology 2014 in Pittsburgh
will highlight some of these advances as well as
progress in newer refractory metal silicide al-
loys for ultrahigh temperature applications. See
sidebar for details.
Commercial applications
Titanium aluminide alloys based on the γ-
TiAl phase have been widely studied
[1,2]
and cast
components are being introduced into gas tur-
bine engines and turbochargers (Fig. 1). These
commercial successes are the result of a multi-
faceted design approach to modify the natural
highly ordered structure to overcome pure
TiAl’s brittle nature. Lattice-distorting and par-
titioning alloying elements have been intro-
duced, phase transformations and secondary
phases are incorporated, and casting tech-
niques and heat treatments are being used to
homogenize and control grain structure. First
principle calculations are also helping to de-
velop new compositions. Resistance to disloca-
tion movement, which dominates the fracture
and fatigue crack growth behavior and limits
the extent of structural applications, is also in-
fluenced by deformation twinning that results
in cyclic hardening during fatigue.
In most structural applications, compo-
nents must be joined. Solid state joining by dif-
fusional annealing of a foil interlayer can be an
effective technique if there is control over the
intermetallic phases that can form within the
diffusion zone. A novel surface halogen treat-
ment significantly improves the high tempera-
ture oxidation resistance of TiAl-type alloys.
For Ti-Ni shape memory alloys, a refined and
uniform intermetallic precipitate structure is
favored by short annealing times.
Iron and nickel aluminides were researched
extensively in the 1980s and 90s in an attempt
to take advantage of their attractive high tem-
perature corrosion resistance
[3,4]
. Extensive ef-
forts were made to develop Fe
3
Al, FeAl, Ni
3
Al,
and NiAl for a variety of structural applications.
Great progress was made in increasing the high
temperature creep strength of NiAl
[5]
, but it did
not displace single crystal superalloys for high
temperature applications. Commercial applica-
tions include FeAl heating elements, Fe
3
Al
porous hot gas filters, and cast Ni
3
Al rolls for
Structural Intermetallics:
Alloy Design, Processing, and Applications
Structural
intermetallics
offer a number
of attractive
choices to
address an
urgent need for
materials that
can endure
harsh
environments
for extended
periods.
*Member of ASM International
Fig. 1 —
Cast 50-mm diameter TiAl automotive
turbocharger.