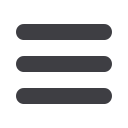
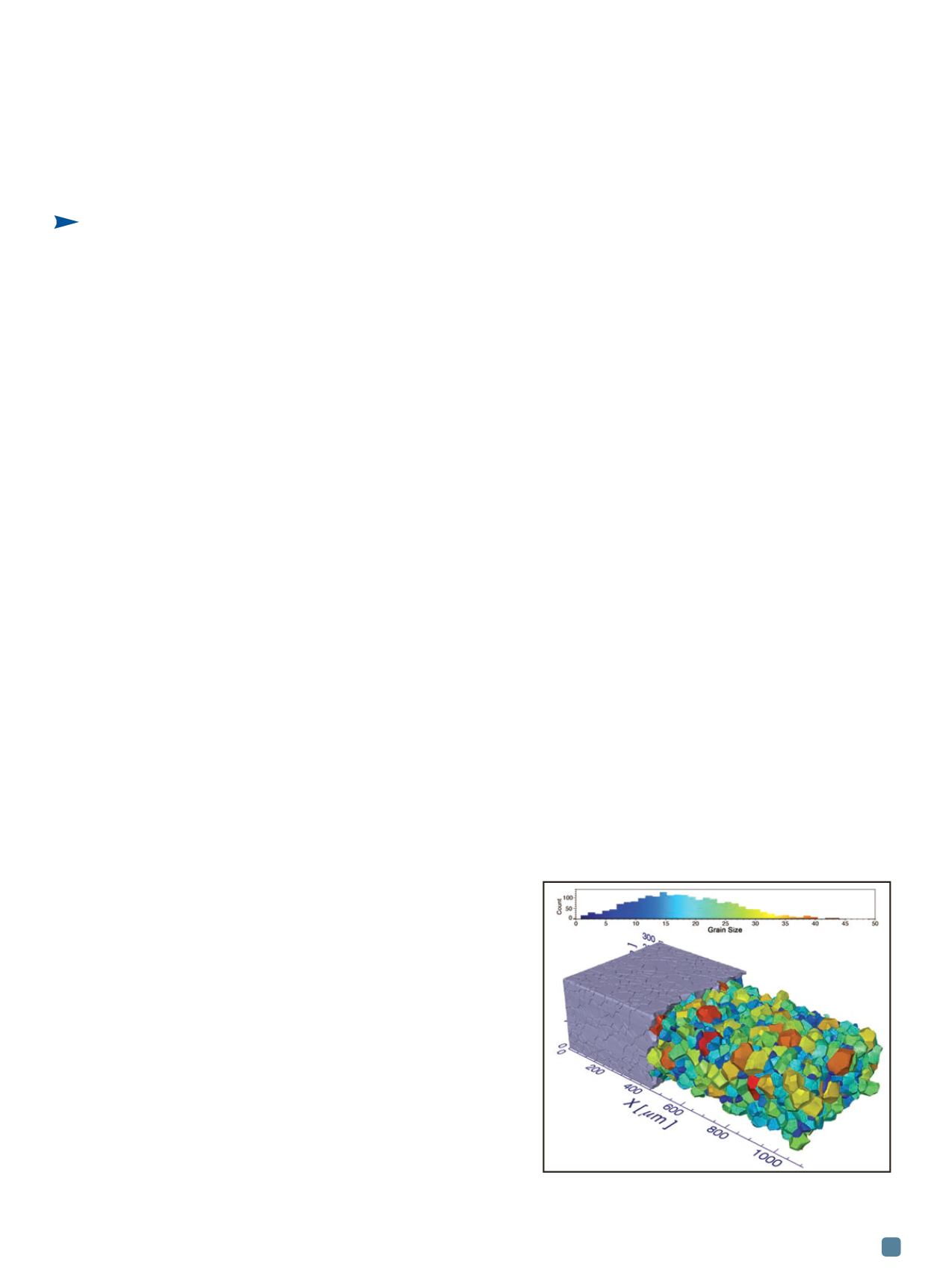
ADVANCED MATERIALS & PROCESSES •
SEPTEMBER 2014
17
Validating Models
Using
3D Microstructural Characterization
T
he microstructures present in any given
material are typically described through
characterizing observations of 2D sec-
tions through that material. Next, the proposed
3D structure is generated either through ex-
trapolation from those 2D observations or sta-
tistical analysis of observed characteristics.
However, the data obtained from 2D observa-
tions is unable to reveal actual 3D characteris-
tics of real microstructures. Even relatively
simple microstructures exhibit complexities
only revealed through 3D analysis, and more
complex microstructures present in many ad-
vanced alloys often preclude accurate determi-
nation of the 3D structure from 2D sections.
A material’s microstructural characteristics
are often used to predict its behavior. Further, a
material’s properties are directly related to its
constituent microstructures, and this fact is
used to develop models and formulae that re-
late microstructural features to properties that
depend on them. However, real microstruc-
tures typically exhibit complex shapes and mor-
phologies, a distribution of characteristic
feature sizes, and variations in spatial arrange-
ments and connectivities often unpredicted
based on 2D sections. For example, while the
largest particle size can be determined from a
big enough 2D sampling section, the smallest
particle size cannot be differentiated from off-
centered sectioning of larger particles. Many
properties are also more dependent on either
smaller or larger feature sizes than on the aver-
age feature size used in most empirical models.
Recent efforts, most notably integrated
computational materials engineering
(ICME) and the Materials Genome Ini-
tiative (MGI), are using computational
models to improve and accelerate new
material discovery, development, and
deployment. These programs require
models that can accurately predict the
microstructures generated by a specific
thermomechanical processing route for
a certain composition and, from this,
predict the corresponding mechanical
properties generated by that mi-
crostructure. Coupling such models to
selected experimental trials for verifica-
tion/validation purposes can dramati-
cally streamline new material discovery.
Accurate descriptions of relevant mi-
crostructural characteristics, however,
cannot be obtained through 2D techniques.
Characterizing materials in 3D is necessary to
reveal the actual distributions of relevant mi-
crostructural characteristics and thereby enable
development of realistic models to predict the
behavior of new materials.
Grain size distributions
One of the simplest andmost widely usedmi-
crostructural characteristics is material grain size,
which indicates the amount of work introduced
into the material and the degree of recovery
and/or recrystallization. Because grain size re-
flects both the amount of grain boundary area
and the typical dimension of easy dislocation
propagation, it is an important factor in many
equations. In particular, the Hall-Petch relation-
ship is an equation that expresses the relationship
between a material’s grain size and its strength.
A number of models have been developed
to predict grain size distributions. In 1957,
Feltham
[1]
demonstrated that a log-normal dis-
tribution can be used to describe grain size dis-
tribution. Eight years later, Hillert
[2]
combined
the theory of Ostwald ripening with grain
growth theory to develop an alternative grain
size distribution. In 1974, Louat
[3]
developed an
additional theory to predict grain size distribu-
tions based on a random diffusion-like motion
of grain boundaries. These are the most com-
mon theories used to model grain size distribu-
tion of a material.
Direct validation of predicted grain size dis-
tributions is difficult. While there are interpo-
lations from 2D measurements, they typically
R.W. Fonda, FASM*
D.J. Rowenhorst
Naval Research
Laboratory,
Washington
In order to take
full advantage of
the promise of
recent
computational
efforts, new
microstructural
models that
consider
realistic shapes,
connectivities,
and distributions
are required.
This can only
be achieved
through 3D
characterization.
*Member of
ASM International
Fig. 1 —
3D reconstruction of grains in a
b
-titanium alloy
colored according to grain size.