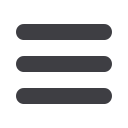
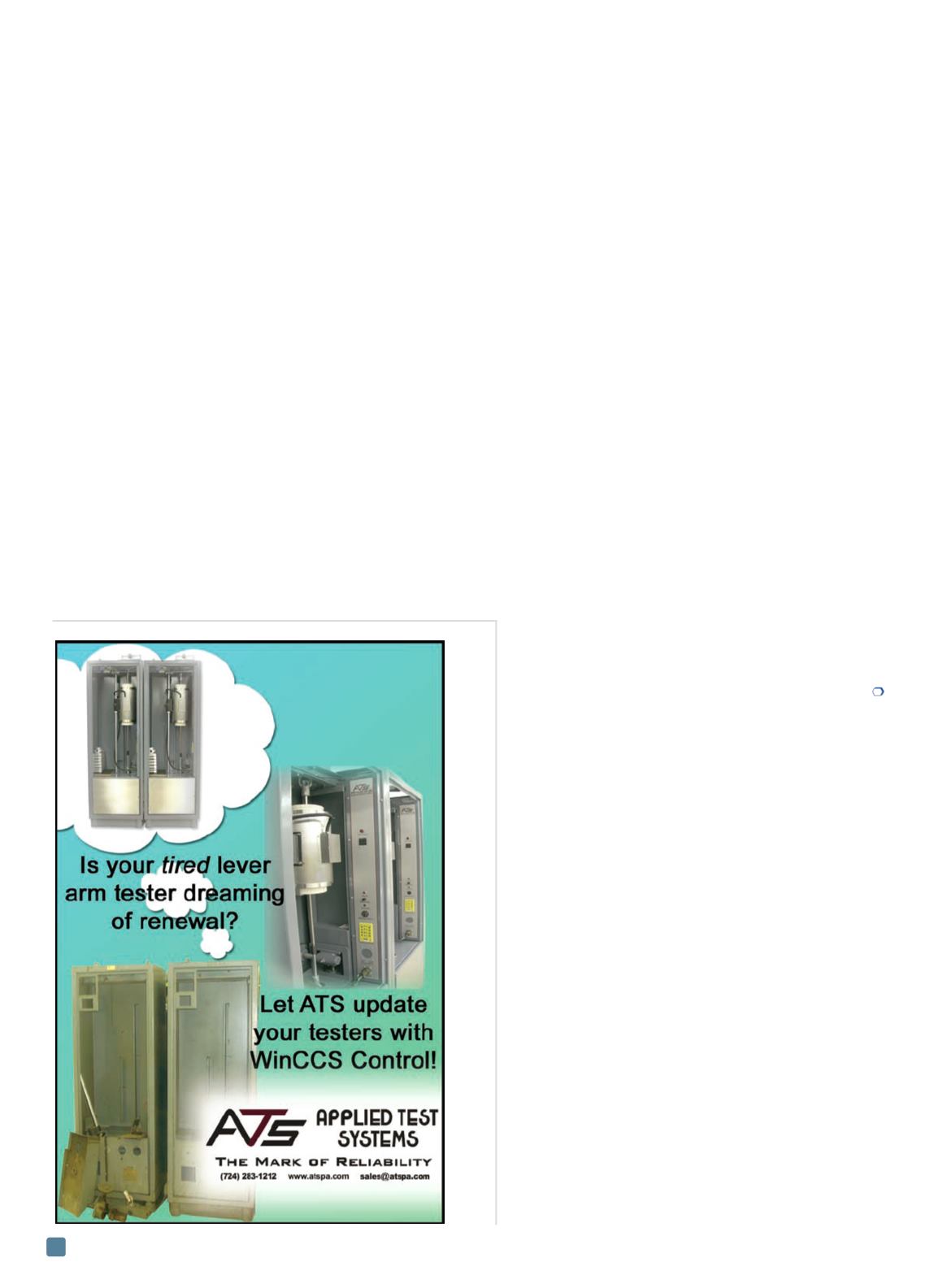
occasional observation of large, approximately equiaxed
martensite constituents on a single 2D surface suggest that
these were martensite plates observed nearly parallel to the
broad face of the plate.
However, serial sectioning and 3D reconstruction of
this coarse martensite, shown in Fig. 4b, reveals that the
actual morphology of the typical coarse martensite con-
stituent
[10]
is that of a lath—a long, thin precipitate with
a moderate width. The observed length of a 2D surface
varies with sectioning orientation, and lath orientations
near 45° can even exhibit the long dimensions on two
perpendicular surfaces that were originally used to iden-
tify and confirm a plate morphology. Further, 3D recon-
struction of the 2D equiaxed morphology, initially
thought to be plan-view images of the martensitic plate,
demonstrate that these are cross-sections of a similar,
but thicker, lath morphology
[11]
.
Conclusions
As ICME, MGI, and other microstructure-based mod-
eling efforts become more prevalent, it is increasingly im-
portant to develop and apply accurate microstructural
models to correctly predict a material’s behavior. These
models are often limited by knowledge of the morphology,
connectivity, and distribution of features within the actual
structure. Current models are typically based on a uniform
distribution of an average feature characteristic (such as
grain size) determined from 2D polished sections. To take
full advantage of the promise of recent computational ef-
forts, new microstructural models that consider realistic
shapes, connectivities, and distributions are required. This
can only be achieved through 3D characterization.
Even relatively simple microstructural features such as
grain size distributions cannot be determined accurately
through 2D analysis. Grain size is a critical component of
many microstructure-dependent property models, so ac-
curate representation of grain size is important. Charac-
terizing the more complex microstructural features
prevalent in many advanced alloy systems and modeling
their influence is even more difficult from 2D sections, and
requires 3D analysis. Both microstructure evolution mod-
els and microstructure-dependent property models need
to have accurate microstructures as input.
The three different cementite precipitate morphologies
proposed from 2D observations all exhibit different growth
rates and properties, and the grain boundary precipitates
grow and impinge at different rates than the actual precipi-
tate morphologies observed through 3D analysis. Similarly,
the correct lath morphology of the coarse martensite found
in low carbon steels through 3D analysis will grow and affect
the properties of the alloy differently than the plate morphol-
ogy assumed from 2D and even two-surface analyses. Pre-
dictions based on 2D observations cannot accurately
represent the real structure of a material. Instead, 3D analy-
sis is required to determine the correct morphology, con-
nectivity, and distribution of the characteristic features.
For more information:
Richard W. Fonda is microstructural
evolution and joining section head at the Naval Research Lab-
oratory, 4555 Overlook Ave SW, Washington, DC 20375,
202.767.2622,
richard.fonda@nrl.navy.mil,
nrl.navy.mil.
Acknowledgments
The authors acknowledge funding from the Office of Naval
Research and through the Naval Research Laboratory, and ex-
press gratitude for the guidance, assistance, and many helpful
discussions with G. Spanos.
References:
1. P. Feltham,
Acta Metall.,
Vol 5, p 97-105, 1957.
2. M. Hillert,
Acta Metall.,
Vol 13, p 227-283, 1965.
3. N.P Louat,
Acta Metall.,
Vol 22, p 721-724, 1974.
4. D.J. Rowenhorst, A.C. Lewis, and G. Spanos,
Acta Mater.,
Vol 58, p 5511-5519, 2010.
5. M. Groeber, et al.,
Acta Mater.,
Vol 56, p 1257-1273, 2008.
6. C. Zhang, et al.,
Metall. Mater. Trans A,
Vol 35A, p 1927-
1933, 2004.
7. M.V. Kral and G. Spanos,
Acta Mater.,
Vol 47, p 711, 1999.
8. R.W. Fonda, G. Spanos, and R.A. Vandermeer,
Scripta Met-
all. Mater.,
Vol 31, p 683-688, 1994.
9. H.K. Bhadeshia, et al.,
Trans. Indian Inst. Metals,
Vol 59, p
689-694, 2006.
10. D.J. Rowenhorst, et al.,
Scripta Mater.,
Vol 55, p 11-16,
2006.
11. D.J. Rowenhorst, A.Gupta, and G. Spanos,
Solid-Solid
Phase Transformations in Inorganic Materials,
TMS, p 569-
575, 2005.
ADVANCED MATERIALS & PROCESSES •
SEPTEMBER 2014
20