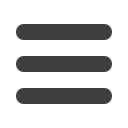
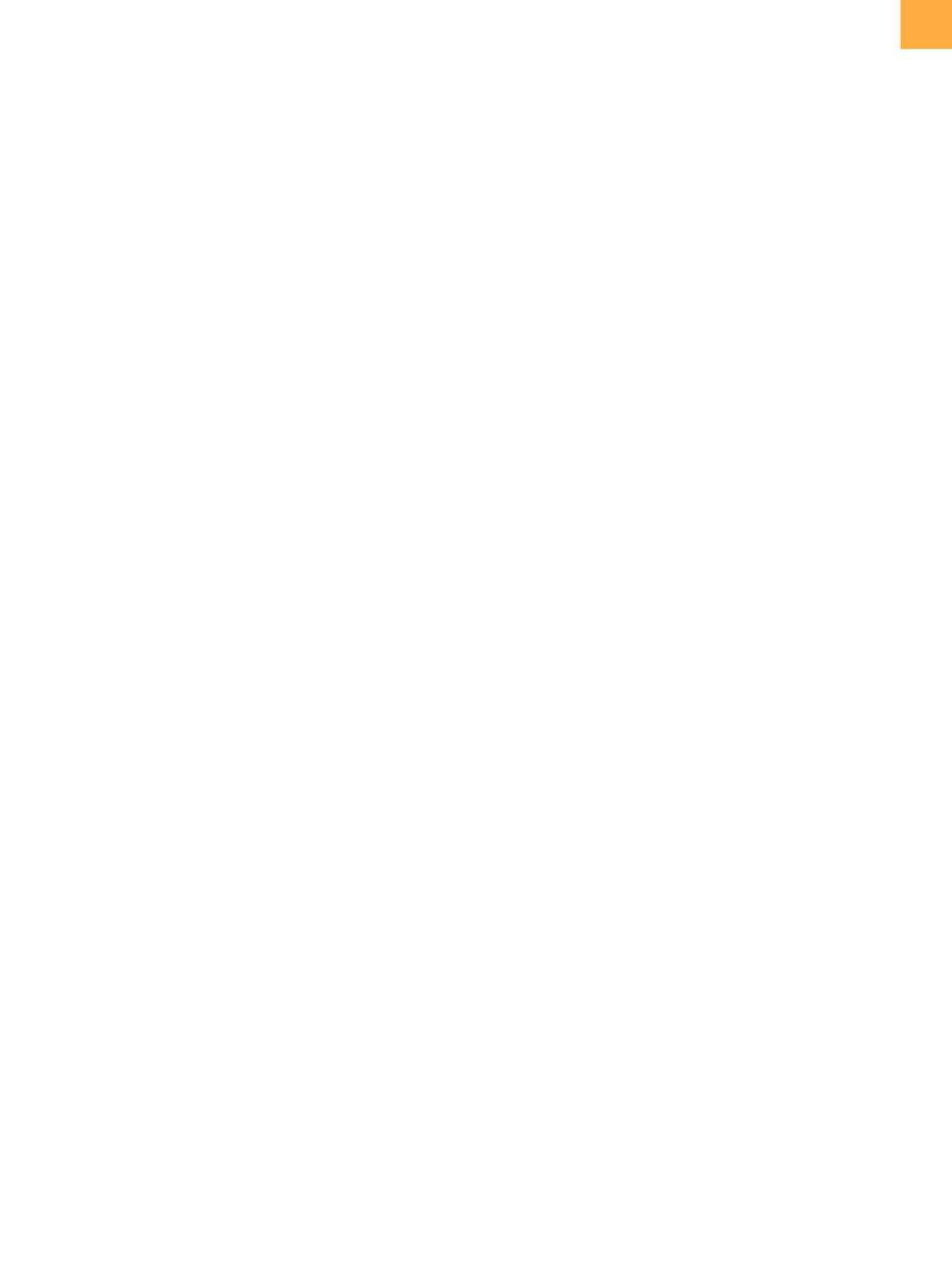
edfas.org
39
ELECTRONIC DEVICE FAILURE ANALYSIS | VOLUME 19 NO. 1
prepping for analytics, optimizing
Z
contrast, thickness
and step-coverage constraints, and accidental cross-
contamination in a dirty prep tool or from a tool internal
component that contradicts one’s conclusions. He also
mentioned general things to avoid when possible, such
as high viscous or mechanical forces that could deform
the sample, solvents that may interact with materials in
the sample, high-temperature applicationor cures, and so
on. He listedmore than a dozen commonly used coatings
(Sharpiepen, polysilicon, SiN, epoxy, eBeamC, eBeamand
iBeam Pt, a list of sputtered metals, silicides, and sput-
tered carbon) along with some of his favorite lab tooling
for applying those materials, as well as pictures of a few
coated structures in cross section. In the end, he professed
an overall preference for sputtered carbon because of
its fine grain, purity, control of thickness and coverage,
optical transparency, and low impact on the sample.
Valery Ray of PBS&T, MEO Engineering Co. followed
up on some of Bryan’s comments about the need to
coat samples that will be subject to charged particles or
electron beams. The approach in his presentation, “Old
FIB Tricks with New Conductive Polymers,” was to forgo
expensive lab high-vacuum systems and instead employ
low-cost spray-on or spin-on liquid-based materials.
Valery began with an overview of the 100-year history
of conductive polymers and how discovery and innova-
tion in materials has helped fuel flat-panel and battery
technology. Polymers and surfactants have found wide
acceptance in electron beam lithography, where their
conductive properties can helpprevent charge buildup on
insulating substrates that would otherwise result in beam
deflection and pattern distortion. Commercially available
formulations, such as ESpacer 300 and aquaSAVE, were
discussed and how relatively easy they are to spin apply
and remove, alongwith their electrical properties. Perhaps
the highlight of his talk was the details of his home-built
spin coater for material application, using such “high-
tech” items as a bench vise, a Dremel rotary tool holding
an SEM stud, and a plastic 100 DVD holder as an overspray
containment device!
Valery showed several examples of SEM, FIB, and TEM
images produced with materials coated with conductive
surfactants. The SEM images were quite good as a result
of the improved surface-charge control. Of course, mini-
mizing total thickness is important, particularly with FIB
imaging. In some cases, FIB images were reduced to only
minimal topology contrast when thick applied layers
resulted in a totally planarized surface. The TEM images
were particularly interesting, where typical e-beam-
depositedmaterials were separated from the surface by a
thin layer of polymer prior to the FIB lamella preparation.
The next two presentations dealt with advanced TEM
preparation methods. Stephan Kleindiek of Kleindiek
Nanotechnik presented “A Novel Software Approach to
TEM Sample Lift-Out Using the Lift-Out Shuttle.” Richard
Young of FEI/Thermo Fisher Scientific presented “TEM
Prep Goes Forth—Ready for Seven.”
Stephan showed his latest load-lock-compatible
shuttle with smart control software. The system replaces
the conventional TEM lift-out technique that requires the
“welding” of a manipulator needle to the top of a sample
and then cutting it loose once the sample is attached
to the lamella holder. Instead, this system employs a
mechanical microgripper (tweezer-like assembly) that
can grab a sample and let it go at will. Offering simplicity
and mouse-click convenience, a single screen interface
controls aspects of the shuttle stage, SEM/FIB column,
and gripper.
Richard’s presentation echoed some of Stephan’s
theme of lift-out automation, but he took it further by
looking at the requirements of the entire sample-prep
process. High-volume process monitor jobs done in
support of manufacturing can rely on a high degree of
automation, but with the understanding that placement-
centering accuracy and final thinning results will suffer.
If work must be done at the highest resolution with very
exacting placement—essential, for example, on 7 nm
gate structures—the best choice is still semiautomated,
or “guided,” operations.
He also showed what can be achieved on the newest
generation of tools, where improvements in ion and elec-
tron columns alongwith advanced in-tool S/TEM imaging
combine to produce exceptional results. Ion columns
can now run at 500 to 1 kV while producing useable
images, enabling superior beamplacement with reduced
amorphous formation. The SEM columns have a higher
current density, enabling better concurrent imaging and
endpointing. Finally, in situ S/TEM imaging improvements
may eliminate theneed to takea trip toadedicatedS/TEM.
Ed Principe of Tescan USA re-introduced the audience
to the concept of the analytical cluster tool inhis presenta-
tion, “Ultra-High VacuumModular FIB-SEM Platforms for
Advanced Materials Processing and Characterization.” As
Ed pointed out, the ultrahigh vacuum (UHV) multibeam
FIB-SEM for Auger analysis was commercialized nearly
20 years ago. Given the new ion species and analytical
techniques we have today, what could we build next?
Ultraclean UHV chambers are required for a number
of advanced surface analysis techniques (time-of-flight