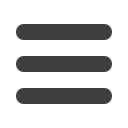
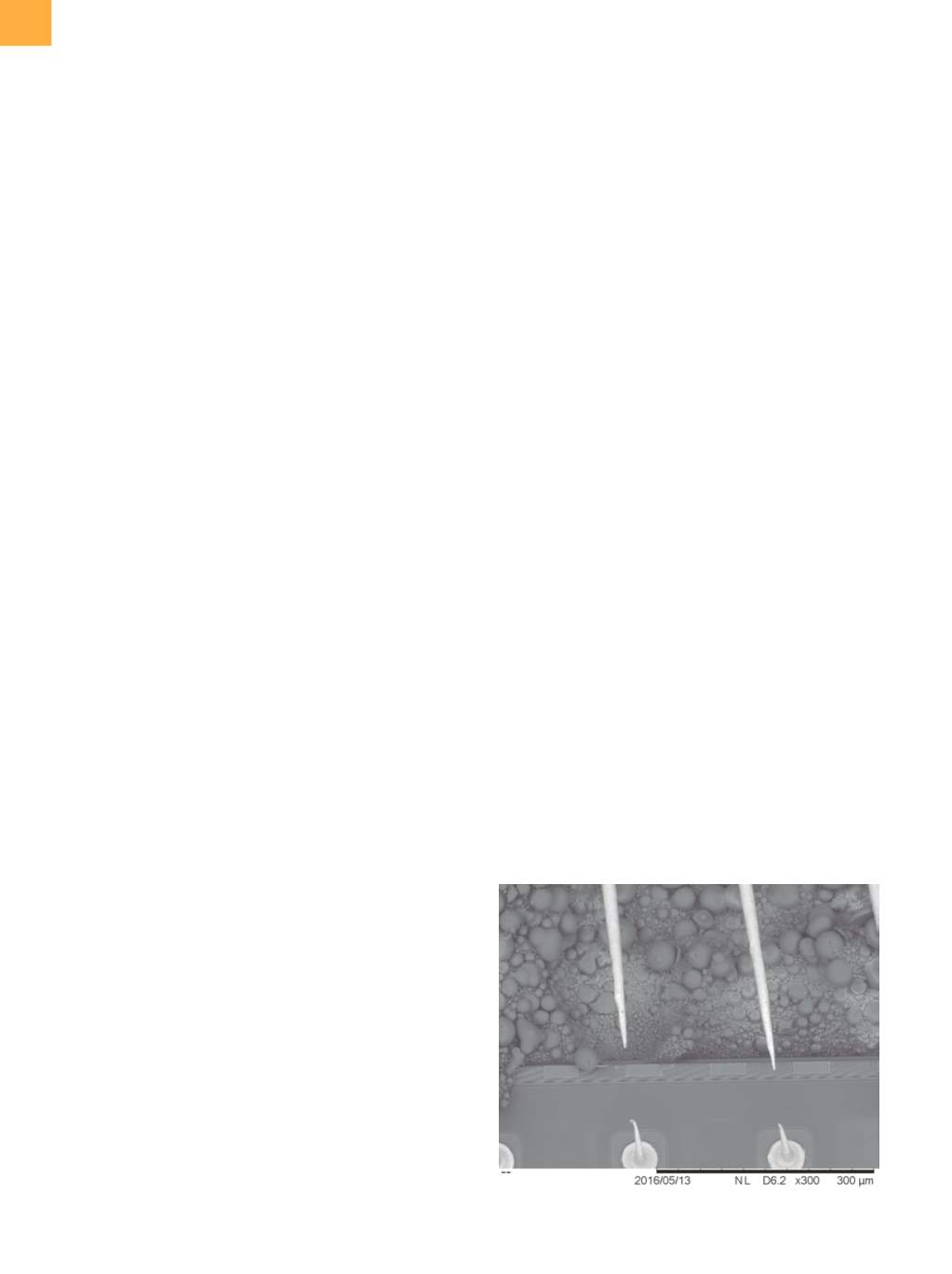
edfas.org
ELECTRONIC DEVICE FAILURE ANALYSIS | VOLUME 19 NO. 1
16
iodine concentrations of up to 0.024 mol/L are possible
for 100% nitric acid.
[2]
The same authors indicate that
it can take many days for nitric acid/iodine solution to
equilibrate in concentration. This observationmakes prior
data, such as in Ref 3, questionable in absolute values but
valid for relative values. The long time required to dissolve
iodine has been observed in our work, with some solu-
tions requiring several days for all of the iodine to go into
solution. This long time frame indicates that little iodine
is actually dissolved in the nitric acid during the 2 h shelf
life observed in Ref 1, eliminating direct dissolution as a
transport mechanism.
The oxidization of iodine to iodate by concentrated
nitric acid is well known, as is the reaction of iodide with
iodate in an acidic environment. This indicates iodate as
the primary iodine-transport mechanism shortly after
the etchant is mixed. Because the solubility of iodic acid
in 98% nitric acid is very low, the iodic acid may be trans-
ported as a suspension as well as a solute.
EVALUATION OF ETCHANT
COMPOSITION OVER TIME
To create a process that is not subject to solution shelf
life considerations, it is necessary to understand what
changes over time in the etchant described in Ref 1. This
was done by mixing according to Ref 1 and evaluating
the solution over time intervals for contained iodate and
iodine. The iodine test does not discriminate between dis-
solved or suspended particles. Because iodine evaporates
from iodine and tri-iodide solutions, a fresh 2.2% Lugol’s
solution was made up immediately before performing
the tests. One milliliter of the solution was placed into a
graduated cylinder, and 30 mL of 98% fuming nitric acid
was added. The mixture turned yellow and was stirred
manually for a few seconds. Samples were periodically
taken as close to the surface as possible. When sampled,
two samples were taken. One was diluted to 1 molar
HNO
3
, and the other was diluted and neutralized to a
pH of approximately 7.5. The neutralized samples were
titrated to determine iodine content. The diluted samples
were evaluated for iodate. The concentration difference
required the use of different solutions for the titrations.
A high concentration of thiosulfate was required for the
iodate samples, and a very low concentration for the
iodine samples. Any undissolved iodate entrained with
the sample will dissolve in the water used for dilution.
This may match the characteristics of the etchant as it is
pumped from the source bottle. Because the iodate pre-
cipitates and settles, less will be entrained in the etchant.
The starting assay indicated that all iodine introduced is
converted to iodate. The assay also indicated no detect-
able dissolved iodine. Over time, as the iodate precipitate
settled to the bottom of the acid mix, the concentration
of iodate decreased, while dissolved iodine remained
undetectable. After 12 h, the acid solution was clear, and
little iodate was detected. After hours, small amounts of
iodine were detected. This indicates that the presence
of iodate is a function of time and the settling rate of the
iodic acid. Because the iodate is not soluble in fuming
nitric acid, it readilyprecipitates out, producing the limited
life observed in Ref 1. The iodine-transporting compound
does not decrease in efficacy; it simply settles out.
EVALUATION OF WIRE PROTECTION
FROM DISSOLVED IODINE
Todetermine if dissolved iodine couldcontribute to the
preservation of silver bond wires, a test was devised that
used only dissolved iodine. A volume of 70% nitric acid
was placed on a stirring hot plate set at 30 °C. An excess of
iodinewas added, and the acidwas left for approximately
36 h. The solution took a strong red-orange color. This
solution was used as the inhibitor source for etching four
parts with an I53 connected to an Elite Etch-Cu. (The I53,
manufacturedbyRKDEngineeringCorp., is apatent-pend-
ing syringe pump configured to introduce small quantities
of a corrosion inhibitor into the acid streamof an automat-
ic decapsulation system. The Elite Etch-Cu, model 7100,
is an automatic dual-acid decapsulator manufactured
by RKD Engineering Corp.) The first part was etched for
120 s with a ratio of 20:1. The etch results indicated that a
longer etch time was needed. The remaining three parts
were etched for 150 s with acid-to-inhibitor mix ratios of
15:1, 25:1, and 30:1. The results are shown in Fig. 1 to 3.
Fig. 1
150 s etch with 15:1
AN EVALUATION OF CORROSION INHIBITORS FOR USE IN ACID DECAPSULATION
(continued from page 14)