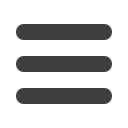
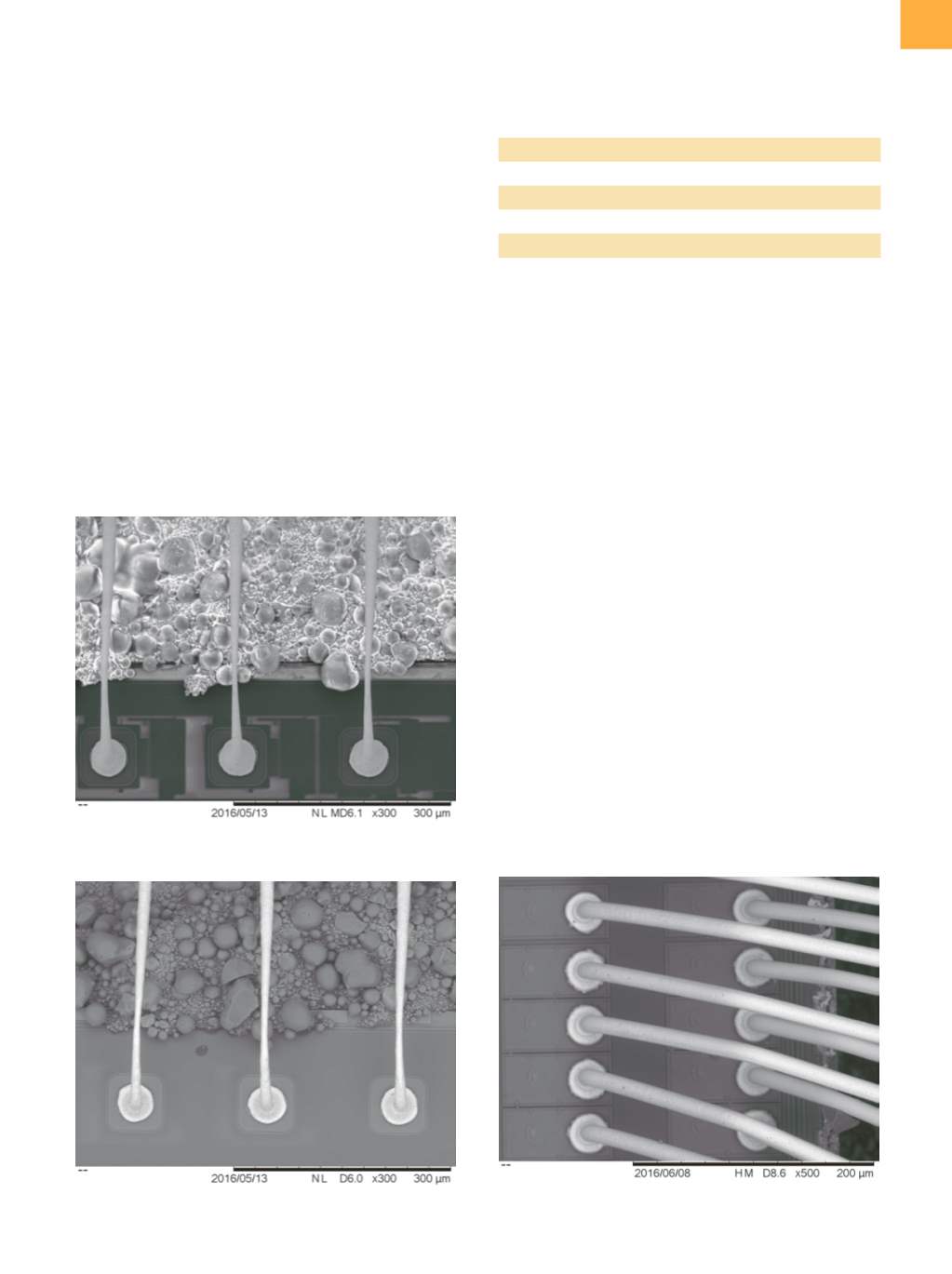
edfas.org
1 7
ELECTRONIC DEVICE FAILURE ANALYSIS | VOLUME 19 NO. 1
Over a 2-to-1 range in iodine concentration, the process
changes from elimination of wires to varying degrees of
wire thinning. It can be seen that iodine dissolved in 70%
nitric acidprovides some protection at themix ratios tried.
Themeasured iodine content of the solution was 0.00372
mol/L. This results in iodine concentrations of 0.00025,
0.00015, and 0.00012 mol/L at the mix ratios used above.
It may be possible to obtain better wire protection with
lower iodine concentration, but the reactivity with the
wires as shown at higher concentrations may indicate a
very limited process range and lack of stability.
EVALUATION OF WIRE PROTECTION
FROM DISSOLVED IODATE
A saturated solution was made of potassium iodate
in deionized water. The concentration is highly tem-
perature dependent but was approximately 0.3 normal.
This is approximately 30 times the measured iodate
concentration established in the evaluation of the etchant
used in Ref 1. This solution was used as the corrosion-
inhibitor source for an I53 connected to an Elite Etch-Cu.
The samples decapsulatedwere the same type as used in
Ref 1, but a slightly different recipe was used, as shown
in Table 1.
As can be seen from Fig. 4, this process effectively
prevents wire damage from the fuming nitric acid used
for decapsulation.
Approximately 72 h later, the same solution and recipe
was used to decapsulate another sample. The results
shown in Fig. 5 demonstrate that the solution is stable
over this time frame. The premixed etchant used in Ref 1
lost effectiveness in less than 2 h.
Due to the sensitivity of the solution concentration to
temperature and its limited solubility at any temperature,
solutions were investigated using iodic acid. In addition
to much higher possible concentrations in water, iodic
acid is somewhat soluble in dilute nitric acid, depending
on the HNO
3
concentration. The addition of nitric acid to
the solution reduces the amount of water introduced,
minimizing metal loss and increasing the efficacy of the
etchant. Two solutions were made up. The first solution
Fig. 2
150 s etch with 25:1
Fig. 3
150 s etch with 30:1
Table 1 Silver wire decapsulation recipe
Etch temperature
30 °C
Heat-up time
120 s
Etch time
120 s
Etch volume
3 mL/min
Rinse time
0 s
Etch mode
Pulsed HNO
3
+ INH
Ratio
30:1 (acid:inhibitor)
Fig. 4
Etched with potassium iodate