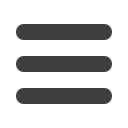
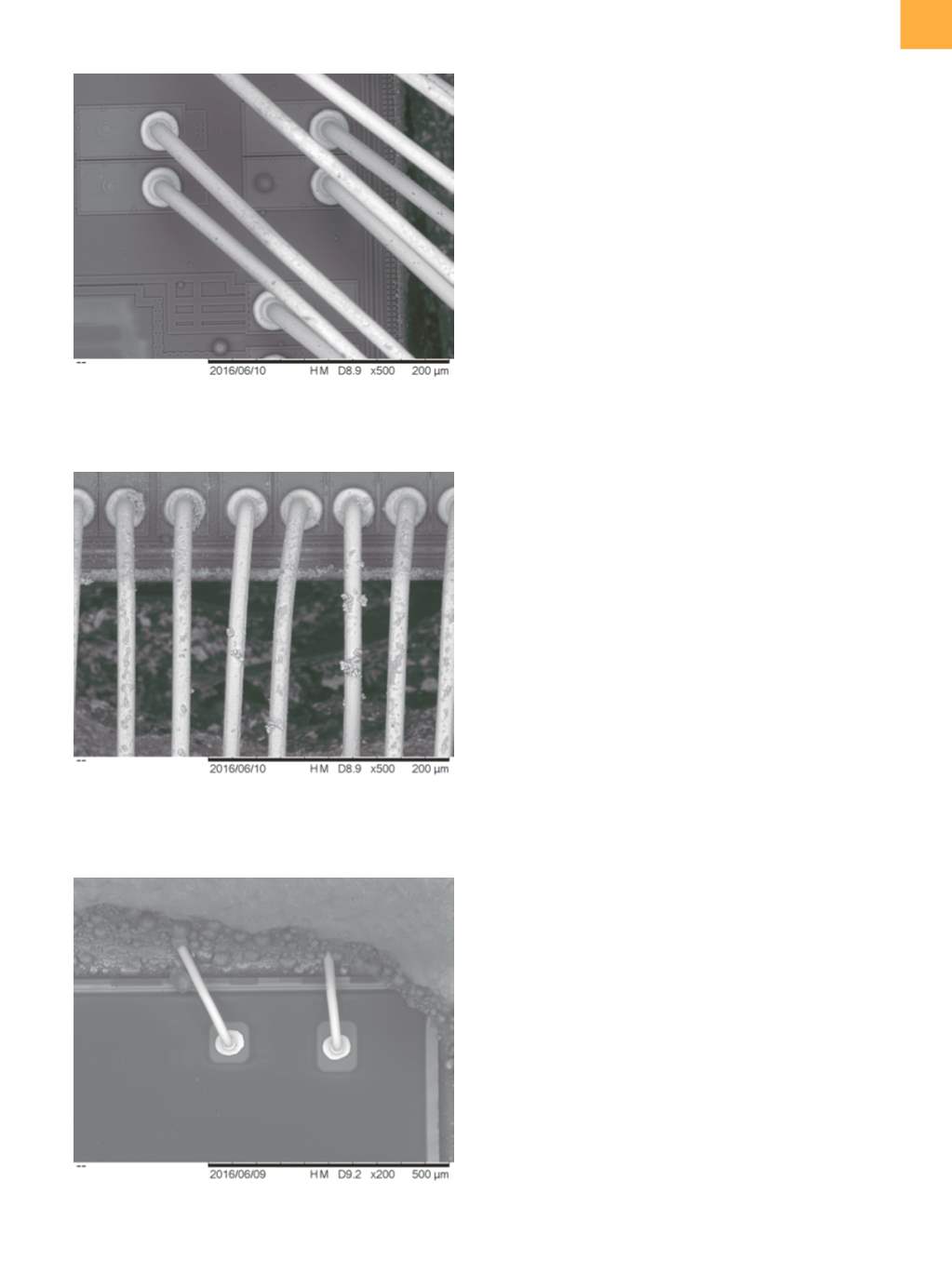
edfas.org
19
ELECTRONIC DEVICE FAILURE ANALYSIS | VOLUME 19 NO. 1
was 0.3 normal HIO
3
in water. The second was 0.3 normal
HIO
3
in 50% HNO
3
. The etch results, at different fuming
nitric acid to corrosion-inhibitor mix ratios, are shown in
Fig. 6 through 11.
All electron micrograph images were taken with the
Hitachi High Technologies TM-3030Plus tabletop scan-
ning electron microscope. No sample preparation was
used, to negate the possibility of any sample-preparation
artifacts. As can be seen, there is no detectable difference
in wire quality. Along with the increasing amount of etch
debris with lower amounts of introduced water was a
corresponding increase in the size of the etched cavity.
As the encapsulant-removal rate increases, so does the
debris load of the etchant and the greater the amount left
on the wires and die surface.
DISCUSSION
The data presented in Ref 1 indicate a fairly narrow
range of process parameters that produce undamaged
silver bond wires. Bond pull strengths dropped with
increasing etch time, higher and lower mix ratios, higher
etch temperatures, and greater age of the premixed
etchant.
Using a corrosion inhibitor that was directly injected
into the fuming nitric acid flow path in an automatic
decapsulator significantly increases the available range
of process parameters. Varying the etchant-to-inhibitor
ratio by a factor of 2 produced no detectable difference
inwire quality. The inhibitor has a nearly infinite shelf life.
Initial evaluations of effects from increased etch
times and higher etch temperatures indicate significant
increases in the useful range of these parameters as well,
as shown in Fig. 12 and 13.
All of theparts shown in thefigures use silver alloywire.
It has been found in additional evaluations that pure silver
wires require a higher-concentration inhibitor solution. An
iodic acid solution at 1.0 M concentration reproduces the
results shown with pure silver bond wires.
CONCLUSION
Silver bond wires can be protected from damage
during acid decapsulation by the injection of a corrosion
inhibitor into the acid stream. The use of a 0.3M iodic acid
solution provides protection of silver alloy wires over a
wide range of process parameters, including etch time,
etch temperature, and the amount of inhibitor injected.
Additionally, a 1.0 M iodic acid solution will provide the
same protection for pure silver wires. This solution also
has a very long shelf life and is relatively safe.
Fig. 11
40:1 iodic acid in dilute nitric acid
Fig. 12
Etched using iodic acid at 50 °C
Fig. 13
Etched using iodic acid with 360 s etch time