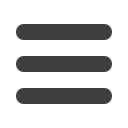
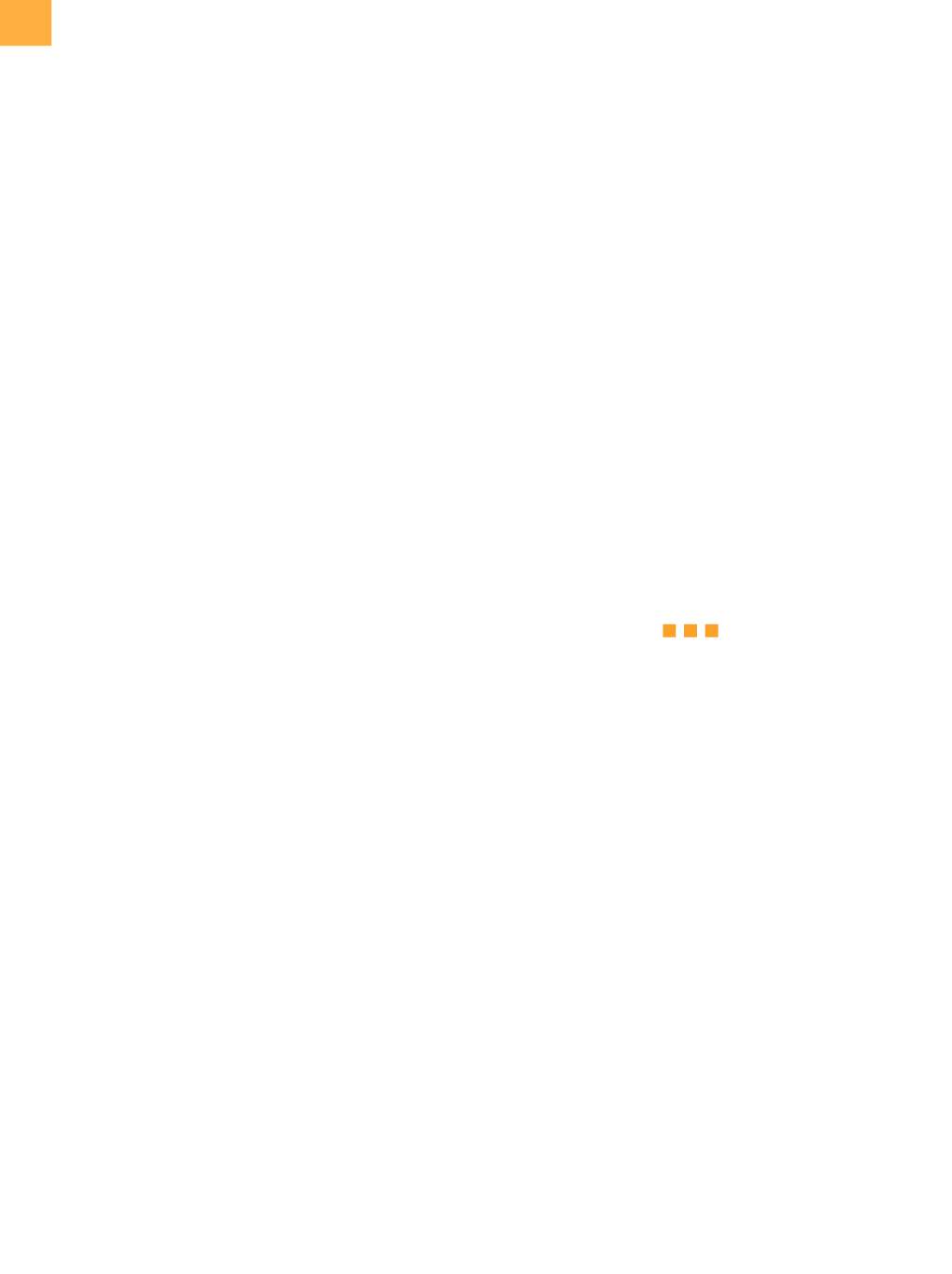
edfas.org
ELECTRONIC DEVICE FAILURE ANALYSIS | VOLUME 19 NO. 1
14
AN EVALUATION OF CORROSION INHIBITORS
FOR USE IN ACID DECAPSULATION OF SAMPLES
WITH SILVER BOND WIRES
Kirk A. Martin, RKD Engineering
Nancy Weavers, Left Coast Instruments
kirk@rkdengineering.comor
nweavers@lcinst.comEDFAAO (2017) 1:14-20
1537-0755/$19.00 ©ASM International
®
BACKGROUND
In previous literature on decapsulation of integrated
circuits with silver bond wires,
[1]
a 2.2% Lugol’s solution
(potassium iodide and iodine in water) was mixed in bulk
with fuming nitric acid and used as an etchant in both
handdecapsulation andwith an automatic decapsulation
system. The freshly mixed etchant worked well, but after
30 to 45 min, the bond pull strength dropped off, reach-
ing zero at 2 h. The bond pull tests showed peak forces
at approximately the 1:30 mix ratio, with the pull force
dropping off at both higher and lower ratios.
Themechanismof protecting the silver wires has been
assumed to be the result of a coating of silver iodide that
forms on the wire.
[1]
This could either be the result of a
reaction between silver nitrate and potassium iodide:
Ag + 2HNO
3
→
AgNO
3
(s) + NO
2
(g) + H
2
O:AgNO
3
+
KI
→
KNO
3
(aq) + AgI(s)
or the direct reaction between silver nitrate and iodine:
2AgNO
3
(s) + I
2
+ 4H
+
→
2AgI(s) +2NO
2
(g) + 2H
2
O
Both cases will produce a porous silver iodide coating
that is not very soluble in fuming nitric acid. It should be
noted that silver nitrate is only slightly soluble in fuming
nitric acid but is highly soluble in water. Because water is
produced during the digestion of the encapsulant, it may
be locally in high concentrations.
The characterization of the iodine transport and
reaction on the wire is necessary to optimize reagent
concentrations at these active surfaces and to stabilize the
process results in relationship to the age of the etchant.
An etchant is needed, or ameans of mixing at the point of
use, that provides optimum and repeatable wire protec-
tion without shelf life concerns.
IODINE TRANSPORT
The addition of Lugol’s solution to fuming nitric acid
introduces iodine as iodide (I
−
) and tri-iodide (I
3
−
). The
introduced iodine will react with the nitric acid, creating
additional species. The possibilities are dissolved elemen-
tal iodine created by the oxidization of I
3
−
, iodide (I
−
), and
iodate (IO
3
−
). Upon contact between the fuming nitric acid
and the Lugol’s solution, I
3
−
oxidizes to I
2
, which is further
oxidized to iodic acid:
I
2
+ 10HNO
3
→
2HIO
3
+10NO
2
+ 4H
2
O
A second reaction takes place between the iodic acid and
iodide:
IO
3
−
+ 5I
−
+ 6H
+
→
3I
2
+ 3H
2
O
The iodine created is oxidized to iodic acid, and the
cycle continues until the only species left is iodate. At the
mix ratios in Ref 1, iodate will be at a concentration of
0.438mol/L of acid, and NO
2
will be five times higher. This
produces enough NO
2
to generate a definite yellow color
to the mixture. The reactions also create a lot of water,
approximately 4 mol of water for each mole of iodine. In
total, the water content of the Lugol’s solution and the
water fromthe reactionswill add approximately 4%water
to the etchant.
Some literature indicates that the solubility of iodine
in nitric acid is fairly high.
[2,3]
One paper suggests that
“IT MAY BE POSSIBLE TO OBTAIN BETTER
WIRE PROTECTION WITH LOWER IODINE
CONCENTRATION, BUT THE REACTIVITY
WITH THE WIRES AS SHOWN AT HIGHER
CONCENTRATIONS MAY INDICATE A VERY
LIMITED PROCESS RANGE AND LACK OF
STABILITY. ”
(continued on page 16)