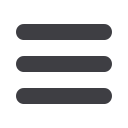
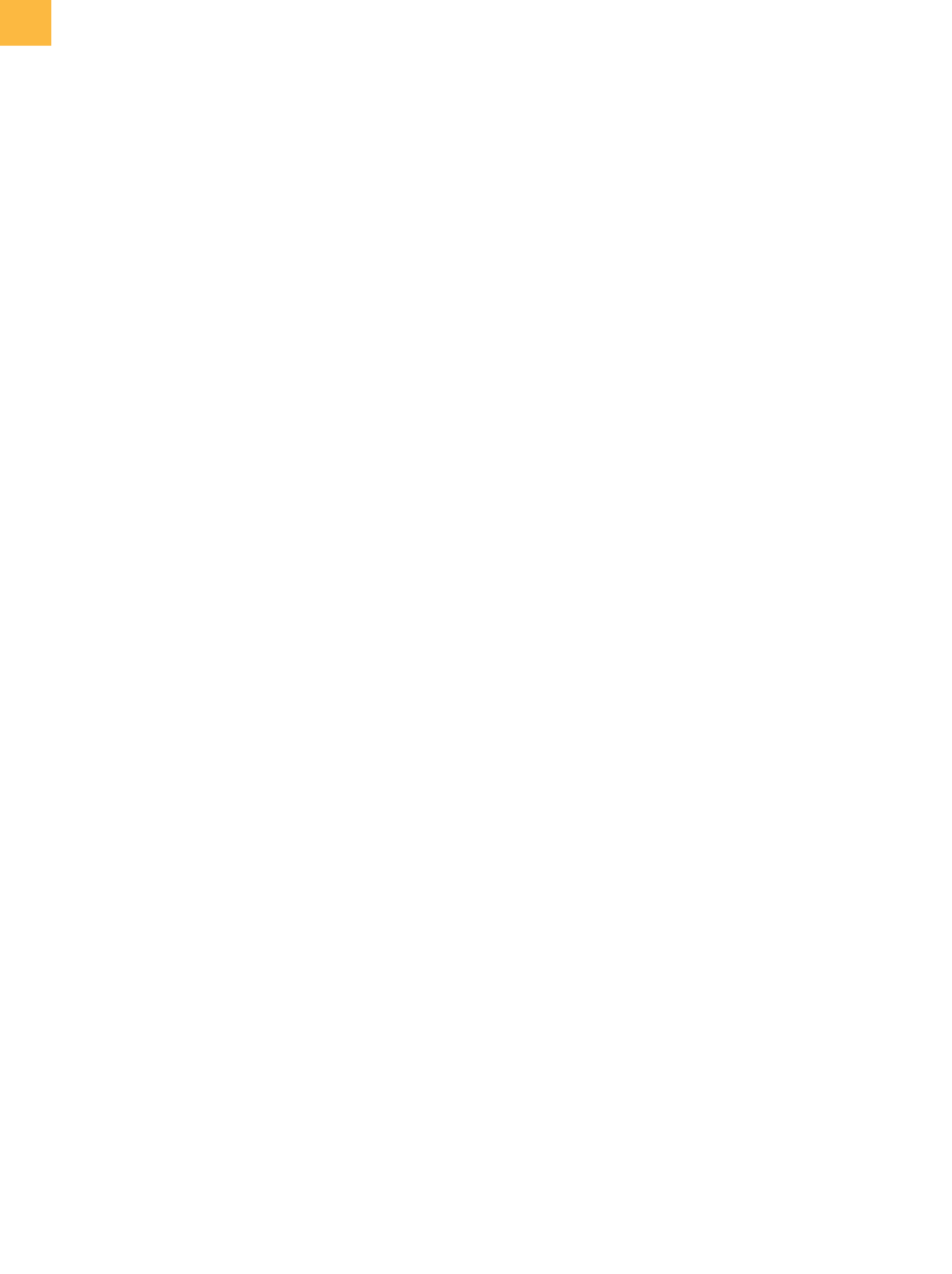
ELECTRONIC DEVICE FAILURE ANALYSIS | VOLUME 18 NO. 2
8
unnecessary and only increases the cost of the system.
The
Z
axis uncertainty must be equal to or better than
the required profile integrity. If it is desired to reproduce
a surface profile to ±1 µm, the
Z
axis repeatability need
not be less than 0.5 µm. If
X-Y
-positional repeatabil-
ity is not constrained directly, it can be defined as the
maximum profile slope divided by the
Z
axis maximum
uncertainty. Therefore, if a 1 µm
Z
axis limit is required,
and the maximum profile slope is 20 µm/mm, the
X-Y
uncertainty needs only to be less than 50 µm. Nowhere
is there a requirement for 50 nm resolution in any axis or
“submicron” accuracy.
If a machine is required to thin plastic-packaged
devices and produce a thinned die with less than ±5 µm
in thickness variation, the following specifications are
all that are required. Tighter specifications only result in
increased purchase and maintenance costs:
• X
and
Y
axis resolution: 1.0 µm
• Z
axis resolution: 0.5 µm
• X, Y
axis independent repeatability: 2.0 µm
• Z
axis independent repeatability: 1.0 µm
• Spindle runout: 10 µm
• Axis orthogonality: 0.05 mrad, maximum
• Variation fromstraight line travel: 0.003mmper 25mm
of travel, including runout
• Axis pitch and yaw: 0.05 mrad, maximum
• Stage deflection: 50 Newtons/µm, maximum
The axis resolution defines the minimum required
scale resolution. It should be 50% or less of the repeat-
ability. The spindle runout limits the effective increase in
tool diameter caused by “wobble.” The axis orthogonality
and axis pitch and yaw each limit axis-to-axis interaction
to 0.05 µm per millimeter of travel. Because all materials
and machines are elastic, the stage deflection specifica-
tion is required to limit the
Z
axis positional change as a
result of the tool forces.
In total, over a 25 mm
2
area, the
X-Y
-positional uncer-
tainty is approximately 15 µm with 2 µm repeatability.
The
Z
-positional uncertainty is approximately 11 µm
with repeatability of less than 2 µm. Any more than this is
unnecessary and costly, and any less does not guarantee
performance.
The axis positional uncertainty comes into play if
the surface profile is measured by different equipment.
If this is done, all of the positional uncertainties of both
the measuring system and the processing machine add.
Because the positional uncertainty is much greater than
repeatability, the integrity of profile reproduction comes
into question.
FRONTSIDE DELAYERING
REQUIREMENTS
Delayering requirements are much more complex.
Delayering on a flat lap requires that the device rotational
axis and the scan axis be parallel to the platen rotational
axis to a degree of precision that is not normally encoun-
tered. Maintaining 10 nmplanarity of a 10mm
2
die sample
requires that all axes be within 0.002 mrad. In addition,
the vertical runout of the platenmust be less than 0.2 µm.
Measuring the runout is problematic, as are the align-
ment measurements, but all are possible with the right
measurement equipment and personnel. Delayering on
a backside thinning machine is even more problematic
because axis alignment is either not available or difficult
to adjust to the accuracy required. Delayering requires
that the spindle be orthogonal to the
X-Y
plane within
0.0067 mrad for a 3-mm-diameter tool. A larger tool
diameter tightens the requirements. Normally, the spindle
orthogonality of a backside system is more than 10 times
that required to do die delayering. Additionally, 10 nm
Z
axis repeatability is not truly available. This indicates that
using a flat lap is difficult and using a backside thinning
system is not realistically possible. If one is delayering
a 5 µm design-rules die, almost anything can be used.
Currently for the latest design rules, only a very carefully
set up flat lap can meet the requirements.
CONCLUSIONS
Claiming or stating resolution as accuracy is disin-
genuous because accuracy is a function of many different
parameters. Accuracy, repeatability, and resolution must
be matched to the process requirements. Increasing
resolution, repeatability, and accuracy beyond what is
required will not increase sample quality. The desired
process results should determine the equipment specifi-
cations. There are some critical parameters that currently
are not specified by some equipment suppliers, such as
the geometric relationships and straight line movement
variations of each of the axes. To ensure that the desired
results are obtained, these parameters must be defined.
For some processes, there are no readily available, simple,
and easy equipment solutions…yet.
REFERENCES
1. “Accuracy,”
Dictionary.com,
dictionary.reference.com/browse/ accuracy?s=t,definition 2.
2. T. Doiron and J. Beers:
The Gauge Block Handbook,
NISTMonograph
180, 2005.
(continued on page 10)