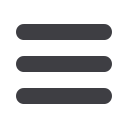
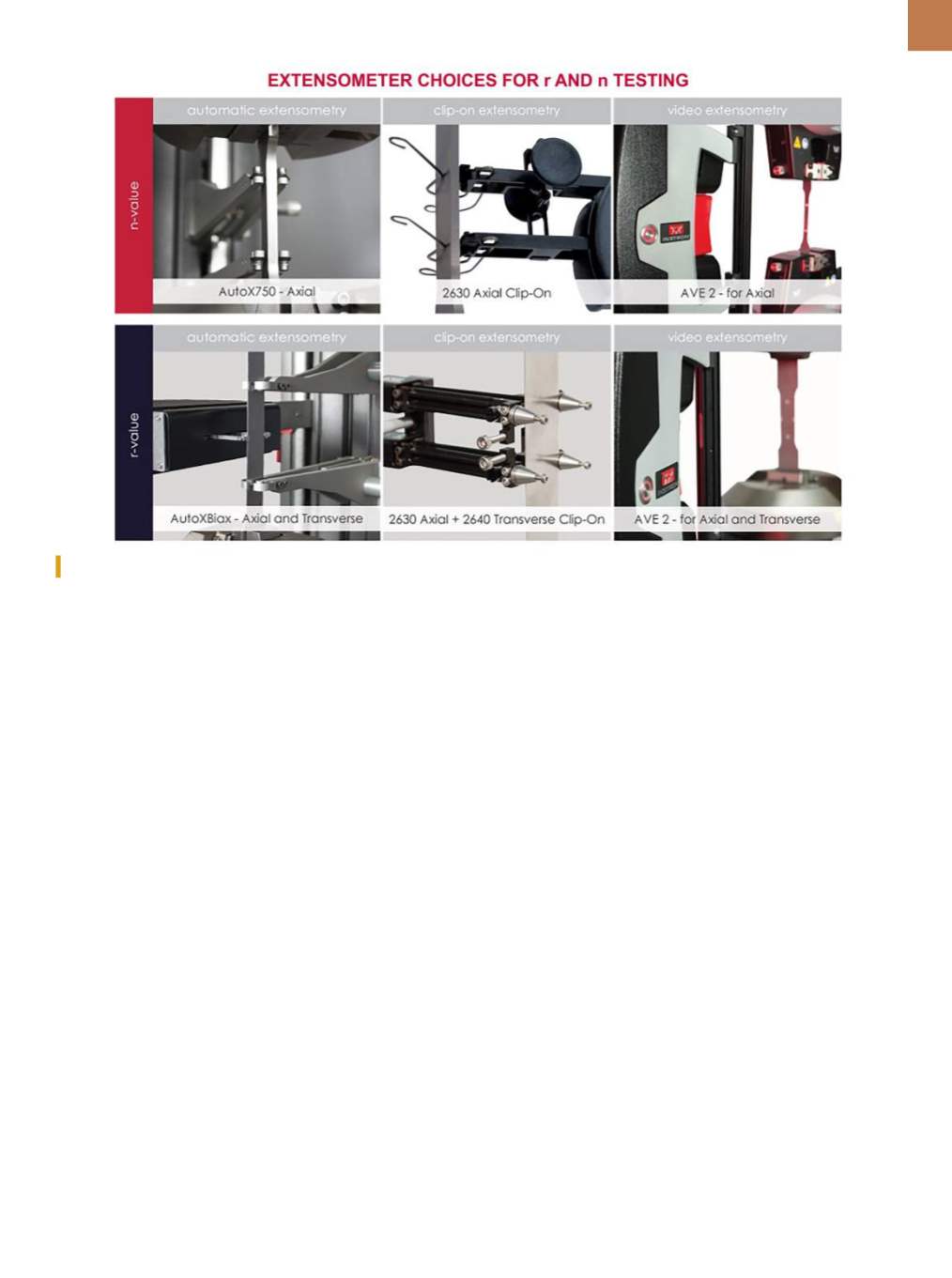
A D V A N C E D
M A T E R I A L S
&
P R O C E S S E S |
O C T O B E R
2 0 1 6
2 5
ers to shape trends and changes within
the industry, directly impacting the
future of structural materials. As with
all research and development, consid-
erable testing must prove that the end
product is high quality, suitable for the
intended application, and able to be
produced with repeatable results.
One testing issue involves the
material’s relative strength. Weaker
materials typically form much more
easily without crack formation. As the
material fails, the break is quite duc-
tile and does not release much energy.
As material strength increases, failures
are much more severe and occur faster,
thus releasingmore energy. Thesemore
aggressive failure conditions can cause
damage to testing equipment such as
extensometers. Traditional clip-on, con-
tact-based transverse extensometers
are difficult to install on specimens con-
sistently and are especially susceptible
to damage during specimen failure.
For
example,
when
testing
advanced high strength steels, the
plastic strain ratio (r-value) must be
determined because it is a key indica-
tor of the material’s forming perfor-
mance. To measure the r-value of high
strength steel and ensure the equip-
ment will not be damaged, Instron
designed the AutoXBiax automatic
contacting extensometer, which can be
automatically removed before failure.
The AutoXBiax uses a robust optical
read head design to keep the device
accurate and operational regardless of
how violent the failure is. An Advanced
Video Extensometer 2 (AVE 2) is also
available, which uses a high-resolution
camera to measure strain, meaning
that nothing has contact with the spec-
imen and the device cannot be dam-
aged by specimen failure. Because the
extensometer does not need to touch
the specimen, the device can also be
used with a temperature chamber, pro-
viding reliable r-value results at low or
high temperatures.
Determining the n-value is import-
ant as well. The strain hardening expo-
nent
n
is a measure of the response of
metallic materials after cold working.
After metals have reached their elas-
tic limit and plastically deform, they
experience strain hardening, which
can increase the strength within the
final product application. Metals with
a high-strain hardening exponent will
achieve increasing strength with a
small amount of axial strain, whereas
a material with a low-strain hardening
exponent will experience high axial
strain with little increase in strength. To
determine n-value automatically, the
axial strain needs to be accurately mea-
sured with an extensometer.
CONCLUSION
It is imperative that the materi-
als testing industry follow these mar-
ket trends. By 2035, there will be an
increase in use of nonmetallic materi-
als in applications formerly dominated
by metals. However, metals producers
will continue to make strides in devel-
oping new alloys to compete, namely
aluminum and advanced high strength
steels. These new metals will be even
stronger and more difficult to test than
today’s materials, demanding that test-
ing equipment manufacturers work
with the metals industry to ensure they
can meet the new challenges.
~
AM&P
For more information:
Matt Spiret is
metals market manager, Instron, 825
University Ave., Norwood, MA 02062-
2643, 800.877.6674,
www.instron.us.
Extensometer styles include automatic, clip-on, and video versions designed to meet the needs of a wide range of materials testing applications.