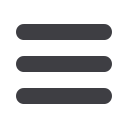
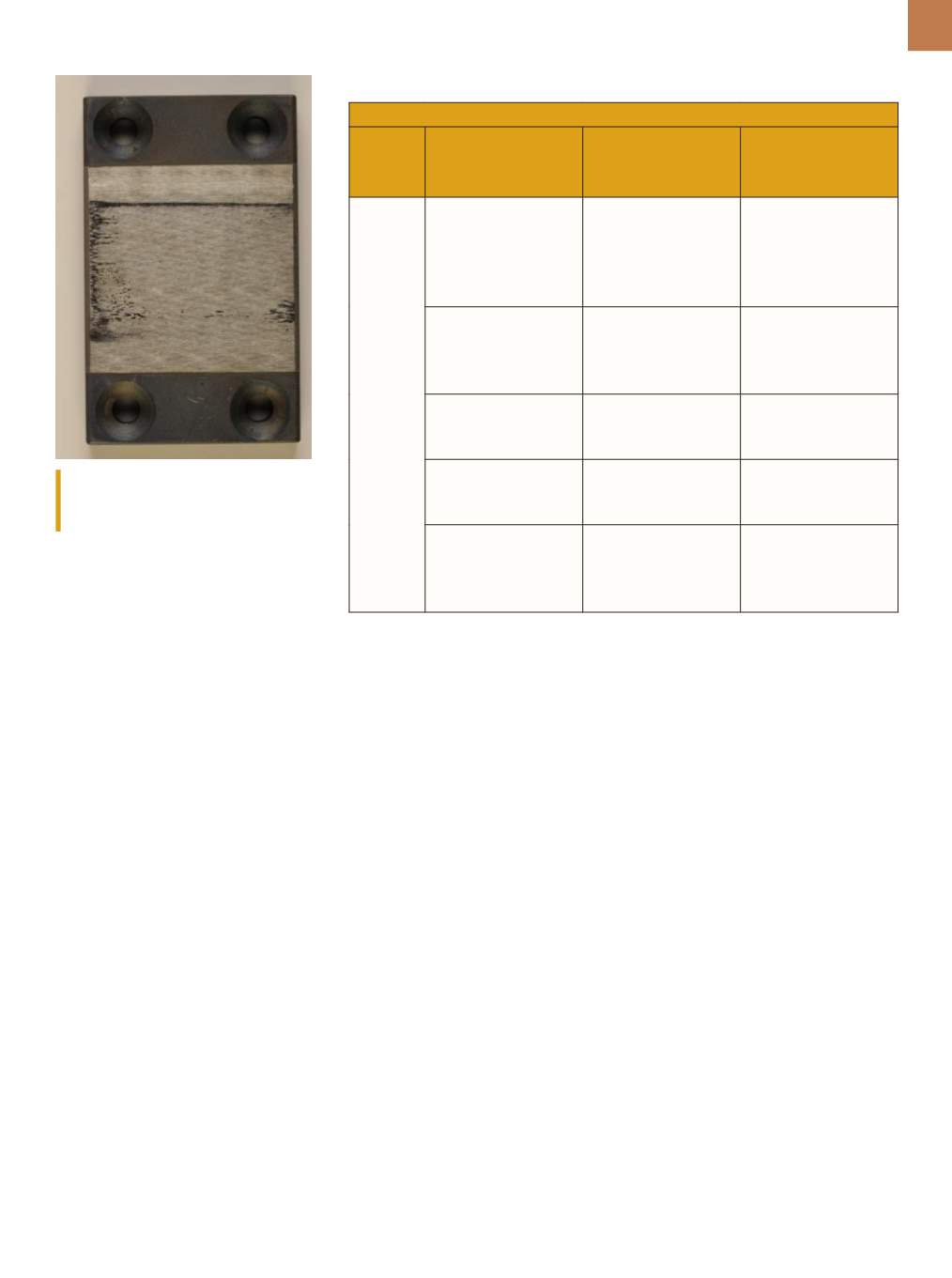
A D V A N C E D
M A T E R I A L S
&
P R O C E S S E S |
O C T O B E R
2 0 1 6
2 7
enables the industrial R&D group and its
members to share the risks and rewards
of aluminum component development
and testing. “The major advantages of
putting ALTec in place is that it enables
a project-based approach that directly
responds to industry needs, combined
with an emphasis on clear communica-
tion with members to rapidly integrate
the advances in their product lines,”
says Gagnon.
For an affordable cost, members
participate in projects designed to
respond to specific challenges. Project
outputs are communicated via confi-
dential webinars and technical briefs,
and members are able to implement
the new technologies. Established in
2015 with seven members and two
sponsors, the group now has 18 mem-
bers including companies such as Ford
Motor Co., PPG Industries, Centerline,
and others with whom projects are
designed. Eight major partners includ-
ing Rio Tinto, Prima, the Aluminum
Association of Canada, and others pro-
vide additional funding and input into
the consortium’s overall direction and
goals. In total, ALTec represents nearly
$3.5 million dollars in R&D investment
per year.
PROJECT COVERAGE AREAS
Approximately 10 projects have
been initiated based on the needs
expressed by members. From a tech-
nical standpoint, the projects fall
under three areas, each led by an NRC
expert. These include manufacturing
of advanced aluminum components,
assembly of aluminum and multi-ma-
terial components, and durability and
performance evaluation and solutions.
“Increasing the productivity of
forming processes such as extrusion,
stamping, and die casting is our objec-
tive,” says ALTec manufacturing expert
Jean Savoie. “We’re helping members
develop new alloys and processes
suitable for rapid production of struc-
tural parts by hot stamping, assisting
them in extruding profiles with various
thicknesses, and developing new core
technologies for high integrity casting,
as well as intelligent dies for forming.
The last 10 years have seen a growing
emphasis on rapid, flexible processes
that will reduce the weight and cost of
components while accelerating their
path to market. We think this can be
achieved through better modeling and
simulation of forming processes, and
we measure our success by the quality
of the first prototypes that come out of
these optimized processes.”
On the assembly side, mechanical
fastening of aluminum to high strength
or stainless steel is being displaced by
friction stir welding (FSW), adhesive
bonding, and resistance spot welding.
Research is focused on finding the best
approach from a corrosion standpoint.
FSW is extremely promising, especially
if it can be made linear—the main chal-
lenge is large loads that result in high
robot payloads in an industry seeking
to minimize these payloads.
To address this issue, a novel
C-frame type robot is being designed
to minimize lateral loads and increase
forging loads. Looking ahead, it is clear
that engineers wonder which welding
or joining technique is the most appro-
priate for a given application, a ques-
tion that is becoming more difficult
TABLE 1
—
PROJECT COVERAGE FOCUS
Project Coverage Areas
Manufacturing of
advanced aluminum
components
Assembly of
aluminum and
multi-material
components
Durability and
performance
evaluation and
solutions
Key
topics
covered
Warm and hot
forming of aluminum
sheet alloys at high
production rates
Durable structural
adhesive joints of
minimally pretreated
multi-material
structures
In-service stress
corrosion cracking:
Evaluation of high
strength aluminum
alloys
Heating coatings
for multifunctional
intelligent molds
Al/steel friction stir
welding process
optimization and
robotic solutions
Mitigating galvanic
corrosion of aluminum
in dissimilar material
assemblies
Tribological coatings
for multifunctional
intelligent molds
Weldability of Al alloys
Design and
production of large
hollow extrusions
Vacuum-assisted high
pressure die casting
of hollow aluminum
structural nodes
High velocity oxygen fuel coated sample
for strip draw test used to evaluate tribo-
logical performance.