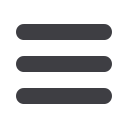

A D V A N C E D
M A T E R I A L S
&
P R O C E S S E S |
O C T O B E R
2 0 1 6
2 3
D
uring the past several decades,
metals were the most commonly
used engineering material. How-
ever, in recent years the metals indus-
try has faced increasing competition.
Strengths of other material groups—
such as plastics and composites—are
threatening metal use in certain man-
ufacturing environments. The most
prevalent examples are seen in the
automotive and aerospace industries
where the principal volume is for sheet
material.
Today, many cars feature body pan-
els produced fromplastics, whichare not
structural and therefore do not require
the advantageous properties of metallic
materials. Most importantly, plastics are
considerably less dense than their
metal counterparts,
which
means
vehicle mass can be decreased by
using plastics instead of metallic
materials. This may be a fairly easy
swap
for
cer-tain
nonstructural
components
and
sec-tions,
but
structural
areas
have
different
requirements.
In
addition,
composite
use
is becoming more widespread in the
pro-duction of higher-end vehicles. In
these applications, the high strength
of com-posite materials and the ability
to place this strength in a specific axis
make them extremely effective at
reducing
overall
vehicle
mass.
Fortunately for the metals industry, the
composites manufacturing process is
relatively expensive compared
to the ability topress and formmetal pan-
els. Composites and metals are very dif-
ferent in terms of mechanical behavior. A
simple example of this is how they react
to a bump or knock. A metal panel may
receive an obvious dent that can be easily
knocked back into shape with no effect
on its properties. However, a composite
material will spring back to shape, but it
is still susceptible to sustaining internal
damage despite no external evidence of
injury.
Similarly, in the aerospace indus-
try, airplanes were traditionally man-
TECHNICAL SPOTLIGHT
TESTING TRENDS: MEASURING
TOMORROW’S STRUCTURAL
MATERIALS
The materials testing industry must follow market trends, keeping up with both
increased use of nonmetallic materials in fields formerly dominated by metals,
as well as new and challenging metal alloys.
Today’s nonstructural automotive body panels are often made of plastics to save weight.
ufactured with metallic materials. In
2009, Boeing released what is touted
to be the most fuel efficient modern
airliner. The airplane is predominantly
produced from carbon fiber reinforced
composite materials, whose strength to
weight ratio is extremely advantageous.
In the past, metals—mainly aluminum
alloys—comprised more than 50% of
the total aircraft structure. In the Boe-
ing 787 Dreamliner, this was reduced to
20% of the overall structure. This trend
toward lower metal use appears to be
continuing.