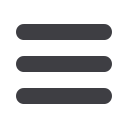
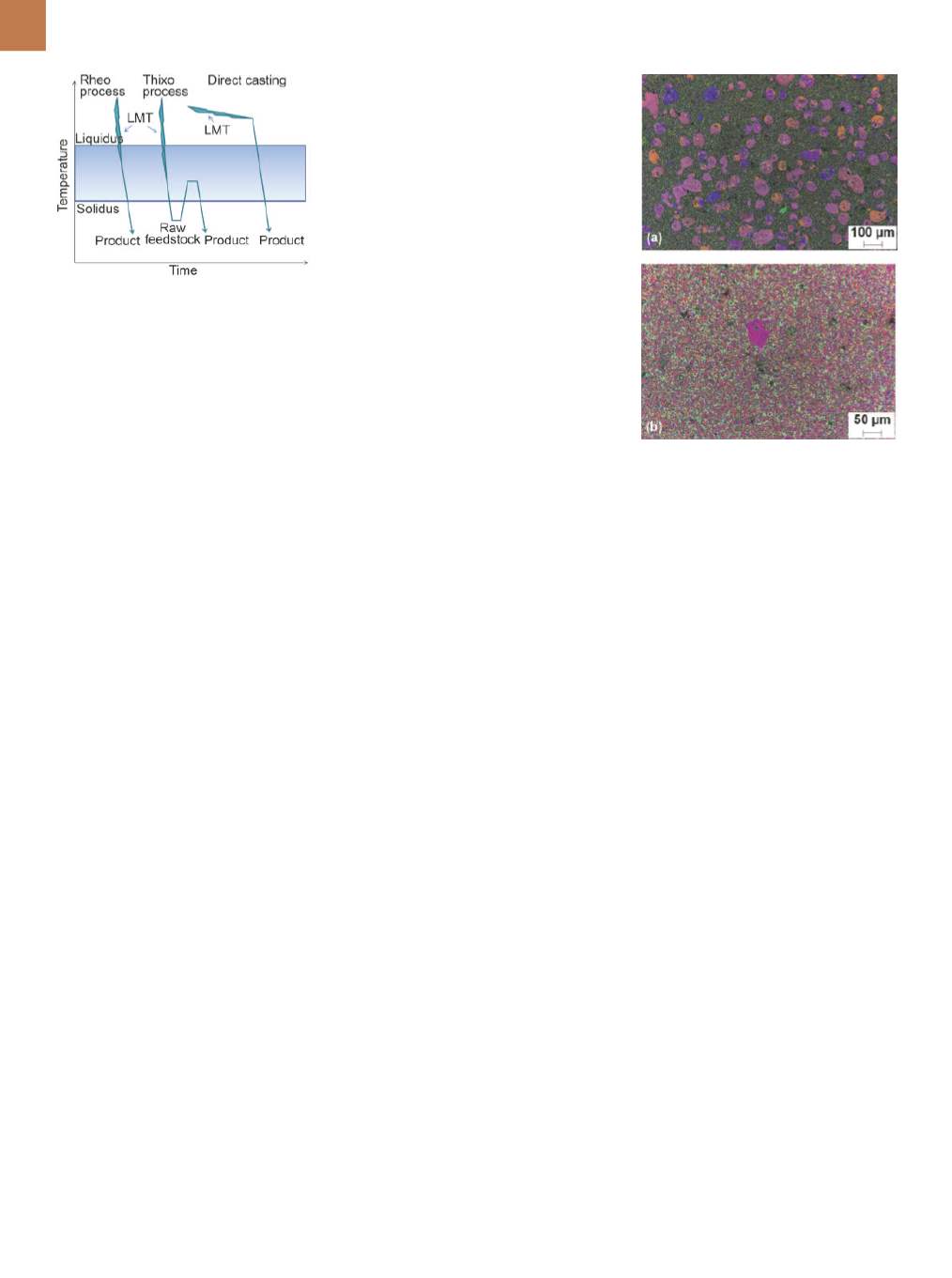
A D V A N C E D M A T E R I A L S & P R O C E S S E S | O C T O B E R 2 0 1 6
2 0
net shape components with properties
substantially better than those in cast-
ings. The primary objective of engineer-
ing liquid metal within all semisolid
technologies is to generate thixotropic
structures through nucleation of glob-
ular forms instead of dendritic ones
during solidification. The former
improves flow during net shape form-
ing and provides other benefits
[4]
. In
contrast to dendritic forms, thixotropic
mixtures serve as deformable semi-co-
hesive spheroidal solids saturated with
liquid, where an applied macroscopic
stress is supported by both solid and
liquid phases. This deformation behav-
ior is unique for thixotropic structures.
Alloys with dendritic features cannot be
deformed by grain rearrangement due
to significant geometric interference of
complex solid features, leading to high
flow resistance.
The initial approach of semisolid
processing focused on rheocasting,
where the molten alloy treatment
during cooling to the liquidus-solidus
range caused transformation from den-
dritic to globular morphologies. Several
liquid metal treatments were intro-
duced as the technology progressed.
Semisolid processing was later dom-
inated by thixoforming (thixocasting,
thixoforging), where thixotropic raw
material produced during the first stage
was subsequently reheated to the semi-
solid range and subjected to net shape
forming. However, thixocasting soon
lost its advantage due to excessive cost,
and today’s semisolid processing is
again dominated by rheo routes.
Fig. 3 —
Concept of liquidmetal treatments
during rheoforming, thixoforming, and liquid
base forming. LMT: Liquidmetal treatment
before transferring into die/mold for net
shape forming.
Fig. 4 —
Features of microstructure obtained
after liquidmetal treatment: (a) semisolid
processing with globular morphology of
primary solid; (b) near liquidus processing;
fine microstructure with a single globule of
primary solid seen in the center. Material:
Mg-9%Al-1%Zn magnesium alloy. Color
etching reveals approximate grain
orientations.
Treatment starts within a sin-
gle-phase liquid and continues during
coexistence of a two-phase thixo-
tropic slurry (Fig. 3). As a result, only
a portion of metal remains liquid and
requires attention at the time of net
shape forming. The solid fraction range
that enables processing was defined
between 5% and 60%. The upper limit
is considered the content above which
the alloy freezes, so it cannot flow into
the mold cavity. However, with the
invention of semisolid extrusion mold-
ing, the upper limit was substantially
raised to over 85%, meaning that only a
small fraction of liquid metal remained
at the time of net shape forming
[5]
.
The thixoforming path involves
partial remelting of the previously
solidified thixotropic alloy, creating
a fraction of fresh liquid within the
solid, which adds complexity. The
chemical composition of the liquid
fraction in the semisolid state dif-
fers from that measured for the bulk
alloy, and the differences grow with
decreasing temperature (Fig. 4a). The
overall alloy chemistry should be spe-
cifically designed for this purpose to
take advantage of having melts with
two different compositions, i.e., an
initial one and another at the forming
stage. The lack of specifically designed
alloys is one obstacle limiting commer-
cialization of semisolid processing.
NEAR-LIQUIDUS PROCESSING
Temperature and time are essen-
tial parameters of liquid metal engi-
neering. Initially, globular structure
formation was explained as the need
to break up dendrites during the freez-
ing process either using mechanical
stirring or other forms of agitation.
The fragments of dendrites within the
melt volume serve as nuclei of new
grains that transform into spheroids.
However, experimental evidence made
this mechanism questionable. Direct
observations of the solidification of
transparent liquids withmetal-like crys-
tallization characteristics and numer-
ical modeling suggest that globular
crystals form through direct nucleation
from a liquid instead of from fragments
of broken dendrites.
In general, the morphology of a
solid in a two-phase mixture of solid
and liquid is controlled by cooling or
convection, or a combination of both.
However, the particular role in gener-
ating globular forms is associated with
melt temperature
[6]
. Generally, lowering
the casting pouring temperature pro-
motes formation of equiaxed solidifica-
tion morphologies. In particular, when
superheating is sufficiently low, the
entire melt is undercooled and copi-
ous heterogeneous nucleation occurs
throughout. This leads to complete
elimination of the columnar zone in the
casting and to formation of fine equi-
axed grains in the entire volume. Exe-
cuting temperature control imposed by
the near liquidus concept is challenging
for certain hardware and larger alloy
volumes. A combination of melt shear-
ing and precise temperature control
in the near liquidus range conducted
within the processing machinery leads
to an ultrafine structure of magnesium
alloys and a superior combination of
strength and ductility (Fig. 4b).
Experiments show the need for
a better understanding of thixotropic