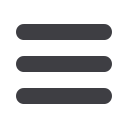
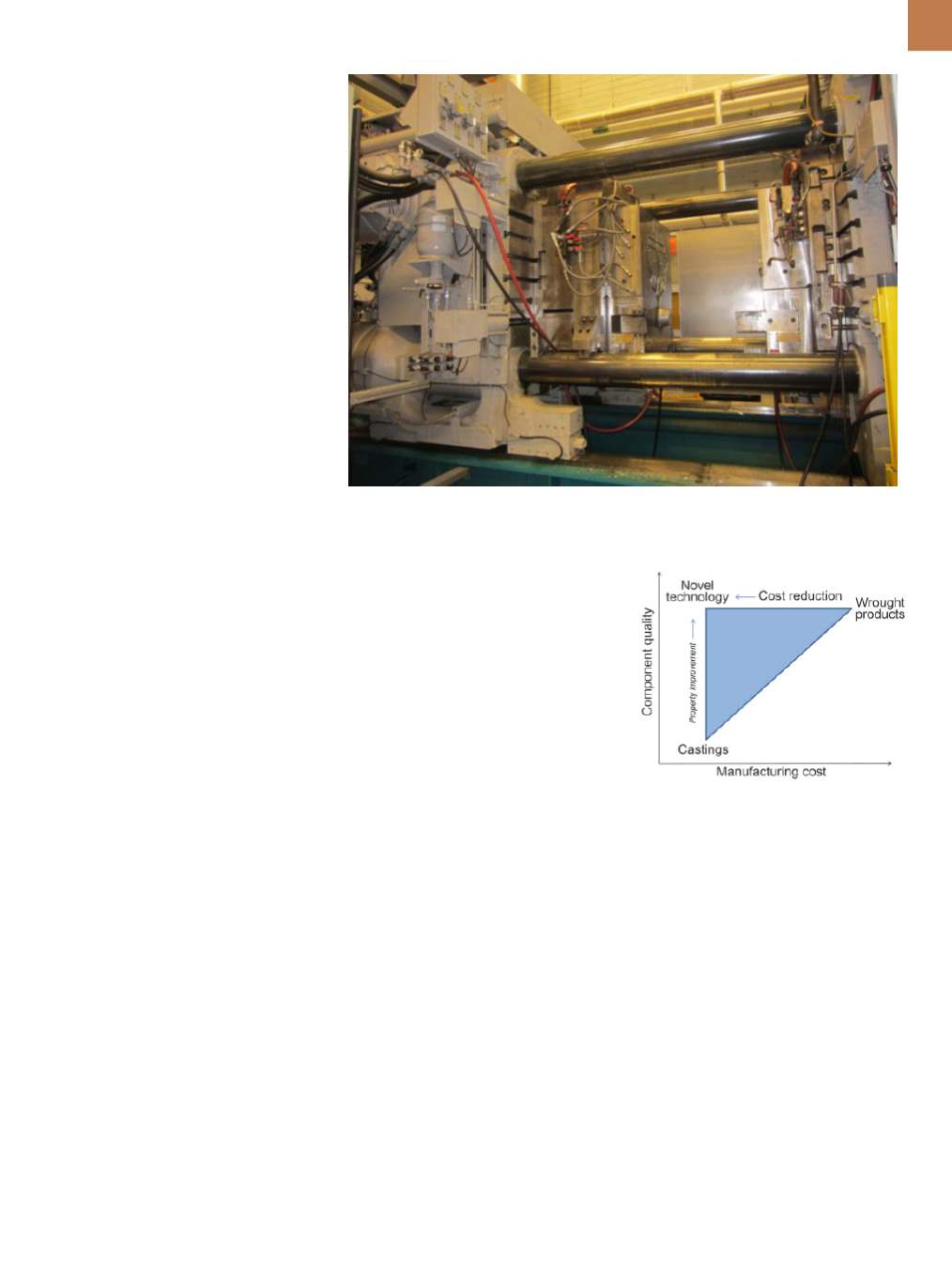
A D V A N C E D
M A T E R I A L S
&
P R O C E S S E S |
O C T O B E R
2 0 1 6
1 9
alloys with specific temperatures and
chemistries to generate thixotropic
morphologies is also being explored. A
generation of unique alloys and com-
posites made by mixing thixotropic
slurries instead of molten alloys offers
another opportunity
[2]
.
Characteristics of two-phase slur-
ries are affected by the deformation his-
toryof thematerial in the solidstateprior
to melting as it occurs during a stress-in-
duced melt activation (SIMA) process,
which demonstrates process complex-
ity. The liquid alloy treatment can occur
either at the stage of raw material gen-
eration for further processing, as in
semisolid technologies, or directly prior
to casting into net shape components.
The overall objective at the stage of raw
material generation might be limited to
alloy microstructure. However, during
forming of net shape components, it
must cover both alloy microstructure
and component integrity. The oppo-
site approach of manipulating liquid to
generate foamed materials instead of
high-integrity structures is also of engi-
neering and commercial interest
[3]
.
Liquid metal engineering is appli-
cable to all alloys although current
research is focused on aluminum and
magnesium due to their lower melting
Fig. 1 —
Clamp area of 1200-ton, high-pressure die casting machine used for industrial-size
trials at CanmetMaterials facility.
Fig. 2 —
Cost-quality relationships for
components manufactured through
casting and through solid state wrought
path. Anticipated location of the novel
technology indicated for comparison.
temperatures, and, therefore, less chal-
lenging designs of processing hardware.
Note that the term liquid metal engi-
neering has also been used for decades
by the U.S. Atomic Energy Commission
for development and non-nuclear test-
ing of liquid-metal reactor components,
covering totally different processes and
materials from those described here.
SEMISOLID STATE
TECHNOLOGIES
Invented in the early 1970s, semi-
solid processing was initially seen as a
technology capable of manufacturing
M
any factors must be considered
when selecting a manufactur-
ing technique to fabricate com-
mercial components for large-scale
production, such as in the automotive
industry (Fig. 1). Two issues of utmost
importance are part quality and cost.
During part design, many manufactur-
ing choices are available. The majority
are associated with either net shape
forming directly from the liquid state
or those involving complex multistep
operations involving a wrought path
with additional hot and cold forming,
machining, and other shaping pro-
cesses following casting. Conventional
casting offers limited part quality at
relatively low cost. By comparison,
solid state forming generally provides
better properties at substantially
higher cost. Work is being done to
improve casting quality and to reduce
solid state processing cost. However,
novel technology that combines the
best features of both processes might
offer the ultimate solution—the high-
est properties achievable in wrought
products at the low cost and simplicity
of casting (Fig. 2).
LIQUID METAL ENGINEERING
Liquid metal engineering is gain-
ing attention as a new technology for
large-scale production. The technique
involves a variety of physical and
chemical treatments of molten metal
to influence solidification. A simpli-
fied approach limits the phenomenon
to single-phase molten alloys above
the liquidus line. However, it should
generally cover manipulating liquid
alloys coexisting with a solid phase, as
is the case at temperatures in the liq-
uidus-solidus region of the particular
phase diagram
[1]
. Current techniques
include melt filtering, rotary degas-
sing, and various stirring/shearing/
agitation methods using ultrasound,
electromagnetic, magneto-hydrody-
namic, and mechanical means (e.g.,
reciprocating injection screw and var-
ious types of mixers). For example,
ultrahigh shear mixing/de-agglomer-
ation solutions used in the food and
cosmetic industries are also being
tested with metals. Developing molten