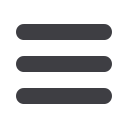
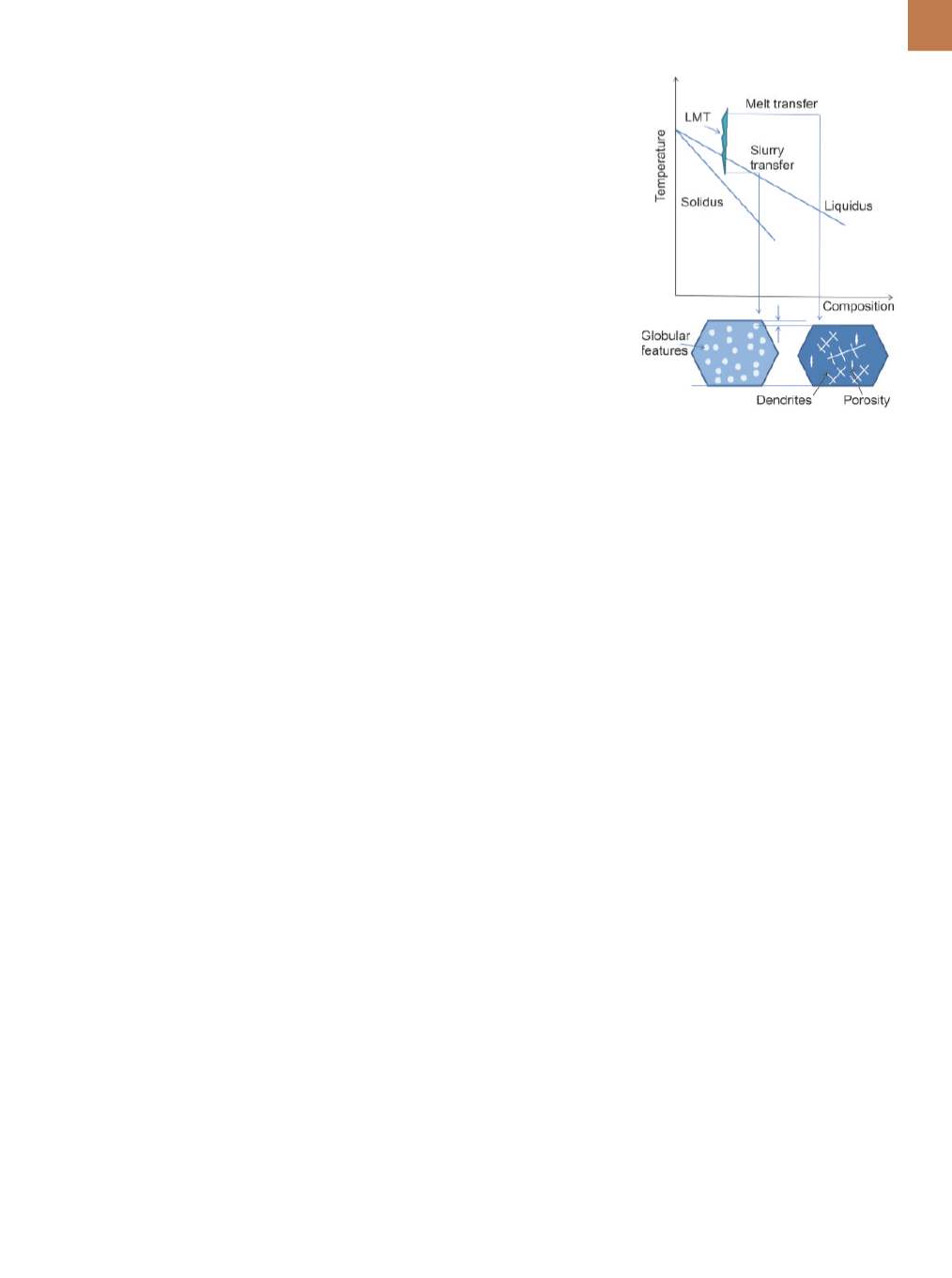
A D V A N C E D
M A T E R I A L S
&
P R O C E S S E S |
O C T O B E R
2 0 1 6
2 1
structure formation by pointing out the
importance of time over melt tempera-
ture during processing, emphasizing
the importance of melting kinetics
[7]
.
The use of high-purity aluminum and
a binary Al-Si eutectic alloy show that
the possibility of forming thixotropic
structures in materials with no practical
freezing range is at odds with the con-
ventional requirement of the freezing
range by inspecting the liquid fraction
versus temperature curve defined as
the processing window. Results suggest
that time sensitivity depends on alloy
mass, heat flux, and phase transforma-
tion temperature.
CONVENTIONAL CASTING
ANDALLOY DEVELOPMENT
Substantial advantages are ex-
pected using liquid metal engineering
on casting alloys with temperatures
exceeding the liquidus. However,
progress over the past few decades in
casting hardware and auxiliaries (par-
ticularly high-pressure die casting) was
not accompanied by understanding
and exploring opportunities created
by engineering liquid metal. Therefore,
there is renewed interest in the pro-
cessing side of die casting, especially in
controlling the nature of molten metal
supplied to the shot sleeve of the ma-
chine. Recently, high integrity castings,
where net shape parts have negligible
porosity after solidification became of
interest. Better quality components
with higher strength lead to potential
savings due to component size reduc-
tion for a given application, resulting
in lower material and energy consump-
tion and a smaller machine to manufac-
ture it, which translates to lower capital
investment.
Recent alloy development shows
that alloying aluminum with elements
having high melting points (e.g., V, Zr,
Cr, Ti or Mo) generates extremely coarse
compounds that degrade alloy prop-
erties in the as-cast state, and require
long, costly post-casting homogeniza-
tion. In some cases, even a long heat
treatment is not effective. Moreover,
to homogenize the molten alloy, high
overheating and long holding times
are required, leading to losses of more
volatile constituents. Therefore, it is
believed that intensive mechanical
shearing/de-agglomeration not only
homogenizes the chemical compo-
sition, but also refines alloying com-
pounds of complex chemistry that
control alloy properties during service.
The melt treatment during alloy gen-
eration should offer benefits including
reducing the overheating temperature
required during melting, reducing
the required holding time in the mol-
ten state, and reducing holding times
during post-cast heat treatment. In
some cases, heat treatment is elimi-
nated, thus improving the energy effi-
ciency of the entire process.
BENEFITS OF CONTROLLED
NUCLEATION
During solidification, the homoge-
neous nucleation, occurring randomly
in the bulk of the liquid, is always kineti-
cally less favorable than heterogeneous
nucleation, taking place on preferential
nucleation sites. The heterogeneous
nucleation can be further enhanced
by providing substrates for easy nucle-
ation described as nucleation potency.
The latter term is defined as the crystal-
lographic lattice mismatching between
materials of the substrate and nuclei.
An epitaxial nucleation model assumes
that heterogeneous formation of the
solid phase on a potent (small lattice
misfit) substrate occurs by epitaxial
growth of the transient solid phase
on the substrate surface under criti-
cal undercooling. This mechanism is
being explored to improve alloy prop-
erties through grain refinement. After a
nucleus is formed, solidification enters
the stage of growth. For decades,
there has been a discussion to deter-
mine which of two stages, nucleation
or growth, exerts a larger effect on the
casting structure. There is a merit in
the recent tendency towards emphasiz-
ing the paramount role of nucleation.
However, to take full advantage of
solidification, both stages, nucleation
and growth, should be understood and
explored.
Metallic oxides present in molten
alloys have a particular role in grain
refinement. During melting, pouring,
Fig. 5 —
Schematic emphasizes component
integrity and alloy microstructure; (left)
semisolid forming with globular morphol-
ogy, high integrity, and better net shape
dimensions; (right) forming from overheated
melt with dendritic morphology, porosity,
and larger shrinkage.
and transfer processes, oxide formed
on the free surface is entrained into the
alloy volume due to melt turbulence.
When an oxidized surface is folded
over onto itself and entrained into the
bulk liquid, a double oxide-film defect
is formed with characteristic features
of unbonded oxide surfaces separated
by a gas. Entrained oxides and other
defects preclude the production of high
integrity parts.
Liquid metal engineering not only
eliminates the harmful effect of oxide
inclusions, but also serves as an effec-
tive grain refiner. For example, delib-
erately dispersed oxide film on molten
Mg alloys using intensive melt shear-
ing functions as endogenous particles
for effective grain refinement. For the
Mg-9Al-1Zn alloy, microscopic analysis
of oxide extracted from molten alloy
reveals submicron-sized MgO particles
resulting from forced breakup of the
oxide films. High-resolution microscopy
reveals good lattice matching between
MgO and the
α
Mg matrix
[8]
. It is con-
cluded from this work that intensive
melt shearing disperses oxide films and
oxide particles at a level that results
in a slow rate of agglomeration, which
enables casting and solidification to
proceed with the grain refining effect.