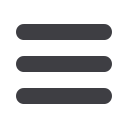
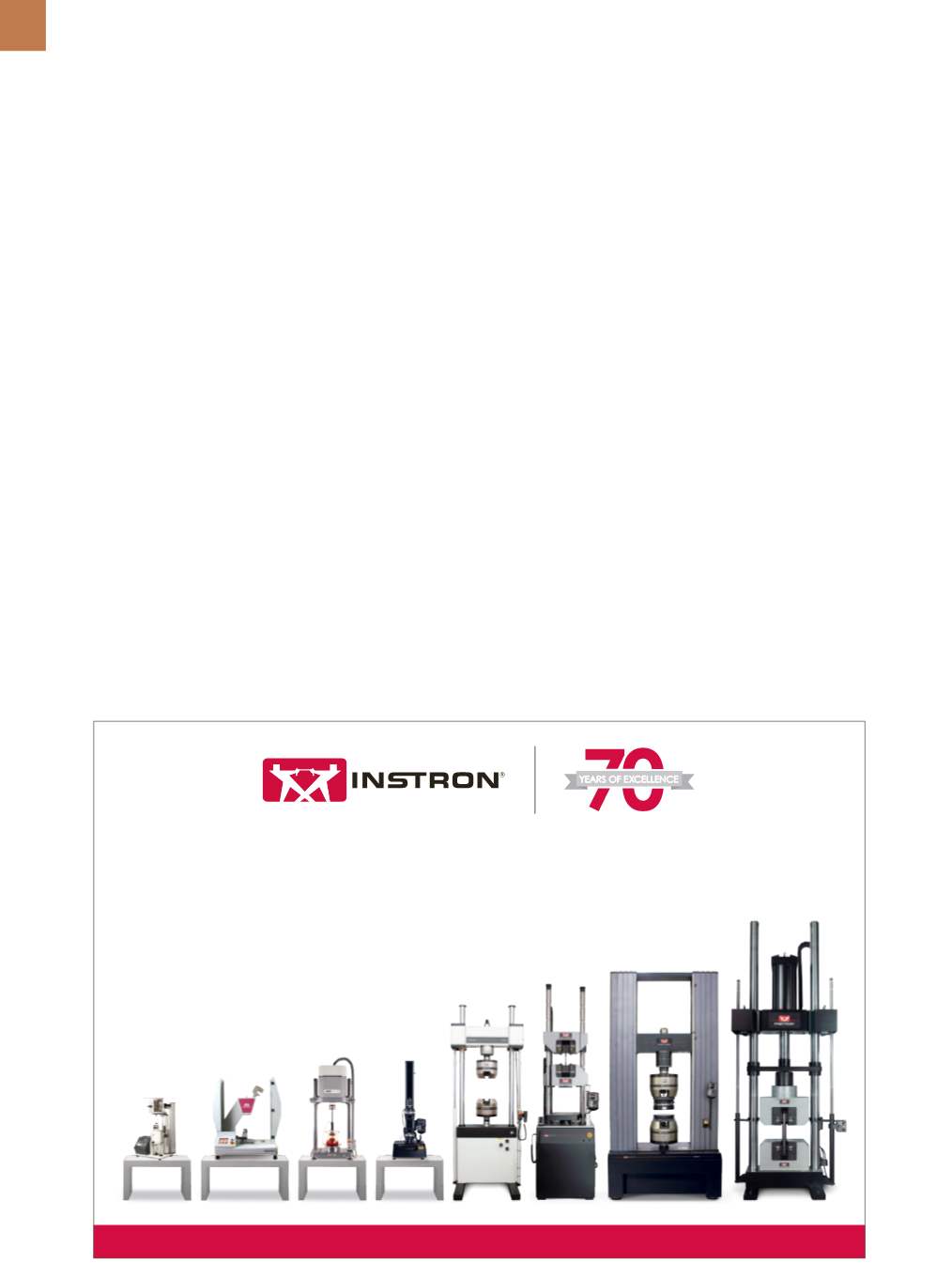
A D V A N C E D M A T E R I A L S & P R O C E S S E S | O C T O B E R 2 0 1 6
2 2
IMPROVING QUALITY
THROUGH PART INTEGRITY
Internal
component
integrity
and alloy microstructure—factors that
affect part performance—must be char-
acterized to assess the influence of
liquid metal treatment on component
properties (Fig. 5). The transition from
casting a liquid alloy into semisolid
state reduces liquid content, resulting
in reduced solidification shrinkage. In
addition, the thixotropic nature of the
slurry improves flow during filling of the
die cavity, which reduces defects, espe-
cially for parts with intricate shapes and
complex filling paths. Both factors have
a positive effect on part quality. At the
same time, the reduced temperature of
the semisolid slurry can lead to prema-
ture freezing, preventing complete part
cavity filling—a negative factor.
The effect of processing tempera-
ture on alloy microstructure is not
straightforward. Alloy microstructure
consists of phases with specific sizes
and morphologies, and replacing den-
dritic forms with globular forms does
not universally exert a positive influence
on properties. In fact, the presence of
coarse globules of the primary solid can
reduce strength. Also, the liquid phase
that solidifies at the end of the process
is highly enriched in alloying elements,
which can be brittle and therefore lead
to a reduction of overall ductility. In
contrast, microstructure refinement
achieved by melt engineering has a
positive effect on part properties for all
solidification morphologies including
dendritic, globular, and equiaxed.
CONCLUSION
There is a continual quest for novel
technology that can be applied to large-
scale production of high-performance
net shape components. Techniques
based on net shape forming from the
liquid state either directly, such as
high-pressure die casting, or exploring
semisolid processing concepts offer
advantages in terms of manufacturing
simplicity, cost, and energy consump-
tion compared with current complex
processes based on solid state forming.
Engineering molten alloys to influence
their solidification process, which leads
to improved component performance
by improving part integrity and alloy
microstructure, looks promising. How-
ever, more research is required to better
understand the technology.
For more information:
Frank Czer-
winski is group leader, senior research
scientist, CanmetMATERIALS, 183 Long-
wood Rd. South, Room 259C, Hamilton,
Ontario L8P 0A5 Canada, 905.645.0887,
frank.czerwinski@canada.ca, or visit
www.canmetmaterials.nrcan.gc.ca.
REFERENCES
1. F. Czerwinski, Magnesium Injection
Molding, Springer, New York, 2008.
2. F. Czerwinski, et al., Metal molding sys-
tem, U.S. Patent 7,694,715, April 13, 2010.
3. F. Czerwinski, Metal molding system
and process for making foamed alloys,
U.S. Patent 7,699,092, April 20, 2010.
4. F. Czerwinski, The Basics of Modern
Semisolid Metal Processing,
J. of Met-
als
, Vol 57, No. 6, p 17-20, 2006.
5. F. Czerwinski and D. Kadak, Process
for injection molding semisolid alloys,
U.S. Patent 6,892,790, May 17, 2005.
6. F. Czerwinski, Near-liquidus injection
molding process, U.S. Patent 7,255,151,
Aug. 14, 2007.
7. D. Zhang, et al., What is the Process
Window for Semisolid Processing?,
Met.
and Matls. Trans. A,
Vol 47, p 1-5, 2016.
8. Y. Wang, et al., Characterization of
Magnesium Oxide and its Interfaces
with Alpha Mg in Mg-Al Based Alloys,
Philosophical Magazine,
Vol 91, No. 8,
p 516-529, 2011.
LEADING THE WAY IN MATERIALS TESTING Founded in 1946, Instron ® is the recognized worldwide market leader in the materials testing industry. Trusted by scientists, engineers, and quality managers worldwide, our products and services aim to instill confidence ... TRUST Instron 825 University Avenue, Norwood, MA 02062 | 1.800.564.8378 | go.instron.com