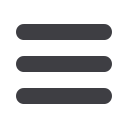
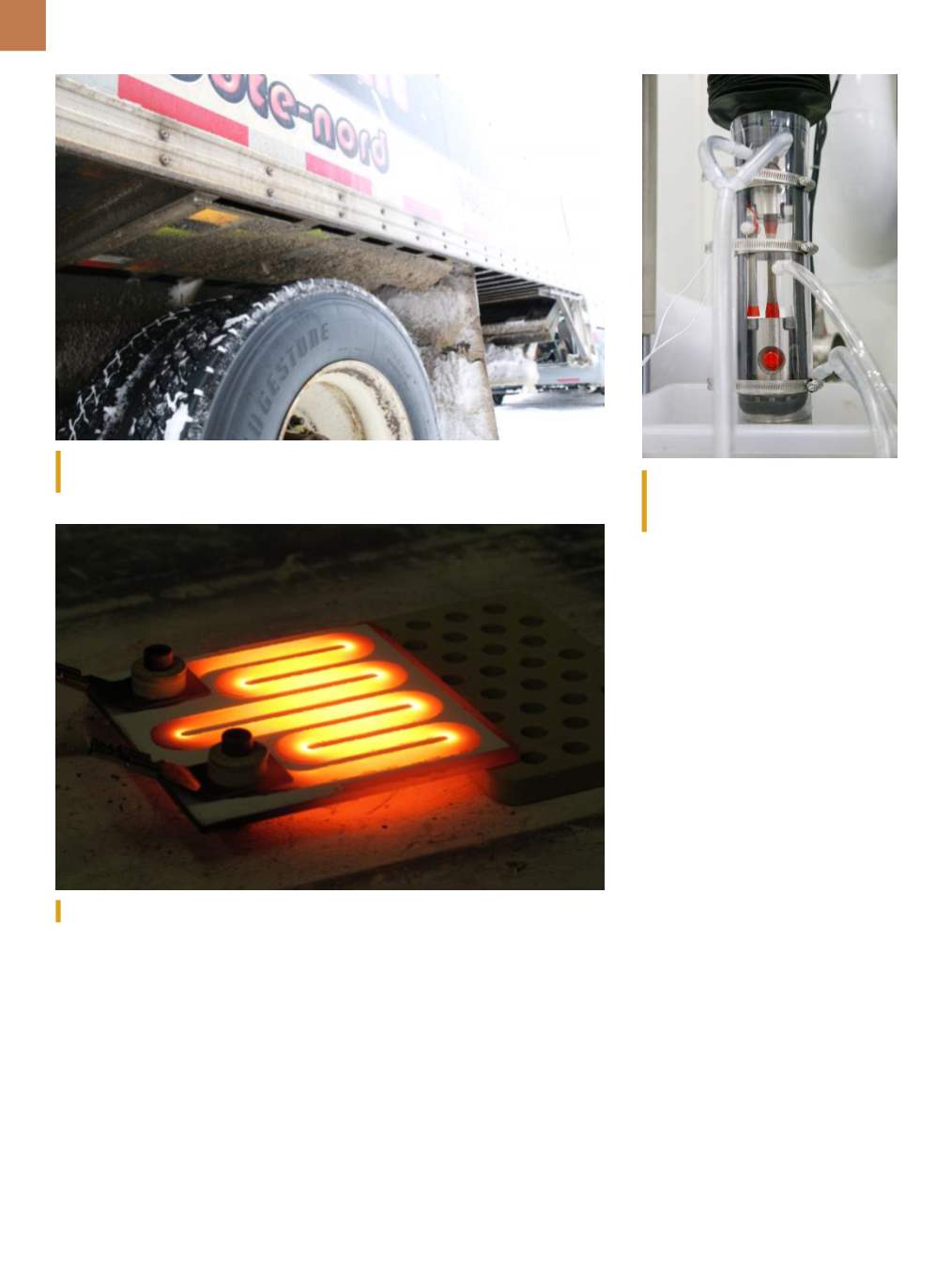
A D V A N C E D M A T E R I A L S & P R O C E S S E S | O C T O B E R 2 0 1 6
2 8
to answer as the spectrum of options
continues to grow. Fatigue design, data,
and life evaluation are thought to be
important aspects in order to answer
these questions.
Corrosion is not a new problem in
the transportation industry. However,
the recent use of multi-material struc-
tures designed to reduce vehicle weight
comes with its share of new challenges,
particularly in terms of galvanic corro-
sion, stress corrosion cracking, and fili-
form corrosion. To address this, ALTec
is banking on a strategy that marries
in-service data, laboratory exposure,
and digital simulation to test new prod-
ucts and solutions. It has already recre-
ated the effects of 150,000 km in-service
field use in an accelerated process that
takes just four days to execute in the
lab environment.
MEMBER TESTIMONIES
Verbom is an aluminum compo-
nent manufacturer as well as tool and
die systems supplier who joined ALTec
to better meet the needs of its automo-
tive clients such as Tesla. “We know that
the clock is ticking for OEMs, that cor-
porate average fuel economy standards
are getting exponentially stricter each
year, and that vehicle manufacturers
are all looking to win the lightweighting
race. Innovation is what attracted us
to ALTec, as well as the leverage we get
from working as a group.” says Nicolas
Bombardier, director of R&D at Verbom.
“We brought in a structural piece from
a client that was impossible to produce
through a conventional drawing pro-
cess, to explore if hot stamping could
be an answer. Because it is a structural
piece, the alloy’s mechanical properties
and its thermal treatment are of utmost
importance. In a short time span, ALTec
has already helped us simulate the
process and produce a few prototypes.
We’re also benefitting from the project
to develop heating coatings for intelli-
gent molds, which are extremely useful
for die casting and extrusion.”
Rio Tinto, a major materials sup-
plier who is both a partner and member
of the initiative, is leveraging ALTec’s
research in assembly, specifically when
it comes to the weldability of new alu-
minum alloys. Joseph Langlais, R&D
casting manager and Jerome Four-
Painted aluminum samples exposed to in-service conditions for determination of chipping
and blistering resistance.
Fatigue-corrosion cell designed for in-situ
electrochemical monitoring of crack
initiation and propagation.
Plasma deposited heater in operation at 600°C.