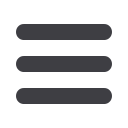
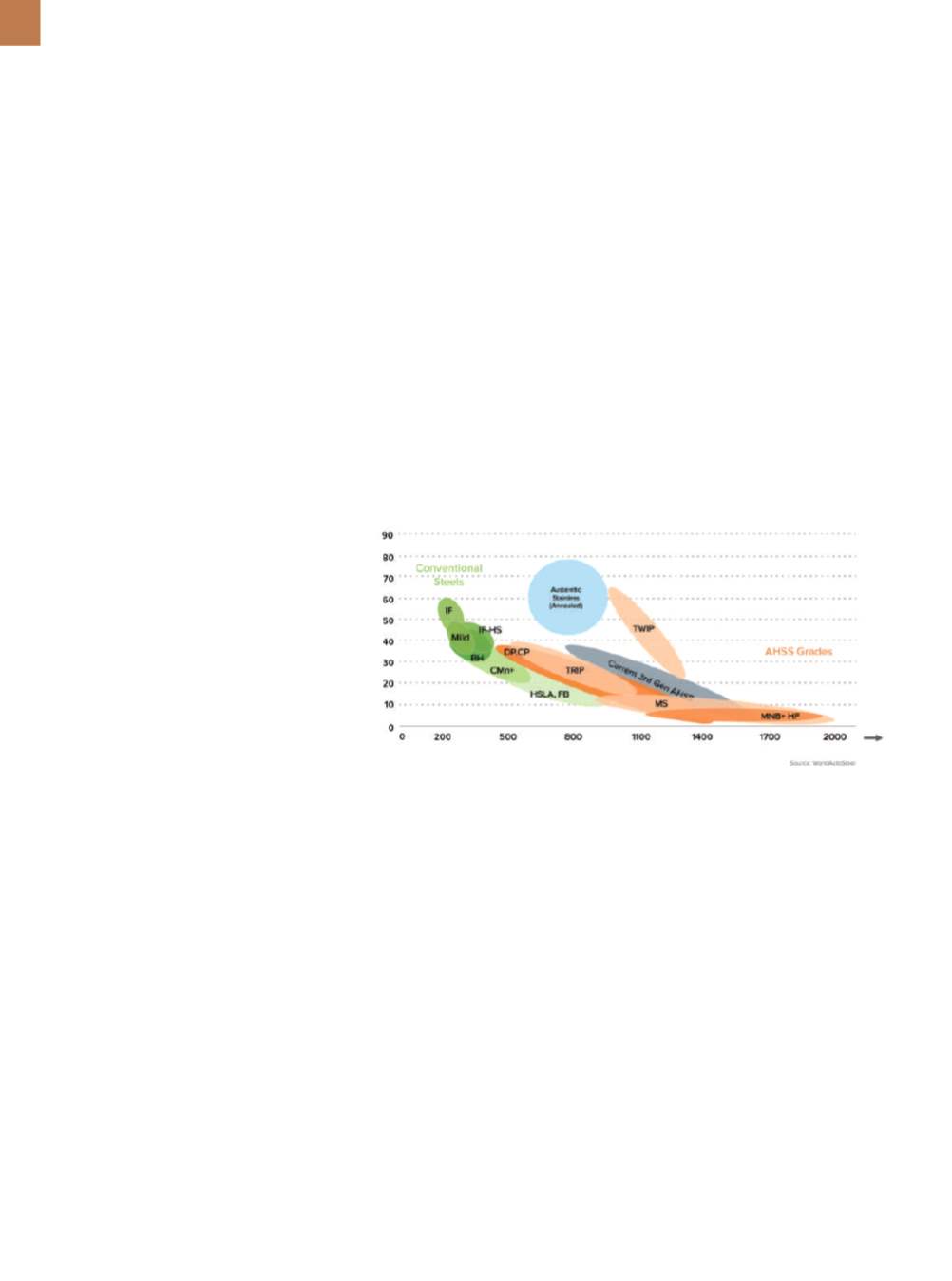
A D V A N C E D M A T E R I A L S & P R O C E S S E S | J U L Y / A U G U S T 2 0 1 6
2 2
TECHNICAL SPOTLIGHT
DESIGNING THIRD GENERATION
ADVANCED HIGH-STRENGTH STEEL
FOR DEMANDING AUTOMOTIVE
APPLICATIONS
By effectively mitigating the historical paradox between strength and
ductility, a new alloy enables an entire family of automotive sheet
steel to meet today’s lightweight automobile requirements.
T
here has long been a struggle
among
materials
scientists
over the paradoxical relation-
ship between a metal’s strength and
ductility. The inability of traditional
materials to meet the dual demands
of both high-strength and easy form-
ability has opened the door for alter-
native materials in applications such
as automotive lightweighting. Existing
advanced high strength steels (AHSS)
require a tradeoff: High strength parts
can either be designed using more
limited geometries or produced using
more expensive methods such as hot
stamping. Both approaches are less
than ideal.
The existing pattern of strength
and ductility relationships in auto-
motive steel alloys is demonstrated
by the well-known
banana plot
from
WorldAutoSteel (Fig. 1). Conventional
steels (green) represent the backbone
of the global economy—they are strong
enough for many applications and
demonstrate high formability, which
allows them to be inexpensively shaped
for a wide variety of uses.
The known AHSS (orange) trade
much of that formability for increased
strength. The one exception is twinning
induced plasticity (TWIP) steels, which
seemed to solve the problem but are
limited in use due to multiple factors
including delayed fracture. Austenitic
Fig. 1 —
WorldAutoSteel banana plot illustrates steel grades used in automobiles.
stainless steels present another option
for achieving the desired properties,
but their cost is prohibitively expensive
for automotive body structures as well
as many other applications.
THIRD GENERATION
AHSS PROPERTIES
Automakers
have
established
properties for third generation AHSS to
meet industry needs (Fig. 2). A number
of ways to design new steels to over-
come existing challenges are being
explored, including variants on quench,
partitioning, and tempering. However,
these types of steels typically cannot
deliver total elongation higher than
20%, which is inadequate for forming
advanced automotive parts.
A different approach to overcom-
ing the existing strength and ductility
paradox to achieve the desired prop-
erties required for third generation
AHSS is being taken at NanoSteel,
Providence, R.I.
[1]
. Conventional steel
constituents in novel ratios are used
while new mechanisms are harnessed
for creating the nanoscale structure.
This approach results in a targeted for-
mation called a
mixed microconstituent
structure
, enabling the sheet to exhibit
the desired AHSS properties.
In the new structure, two distinct
microconstituents act synergistically
on a local level during deformation.
By varying the volume fraction of the
microconstituents in the final sheet
material, many different outcomes for
Elongation, %
Tensile strength, MPa