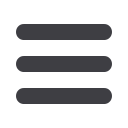
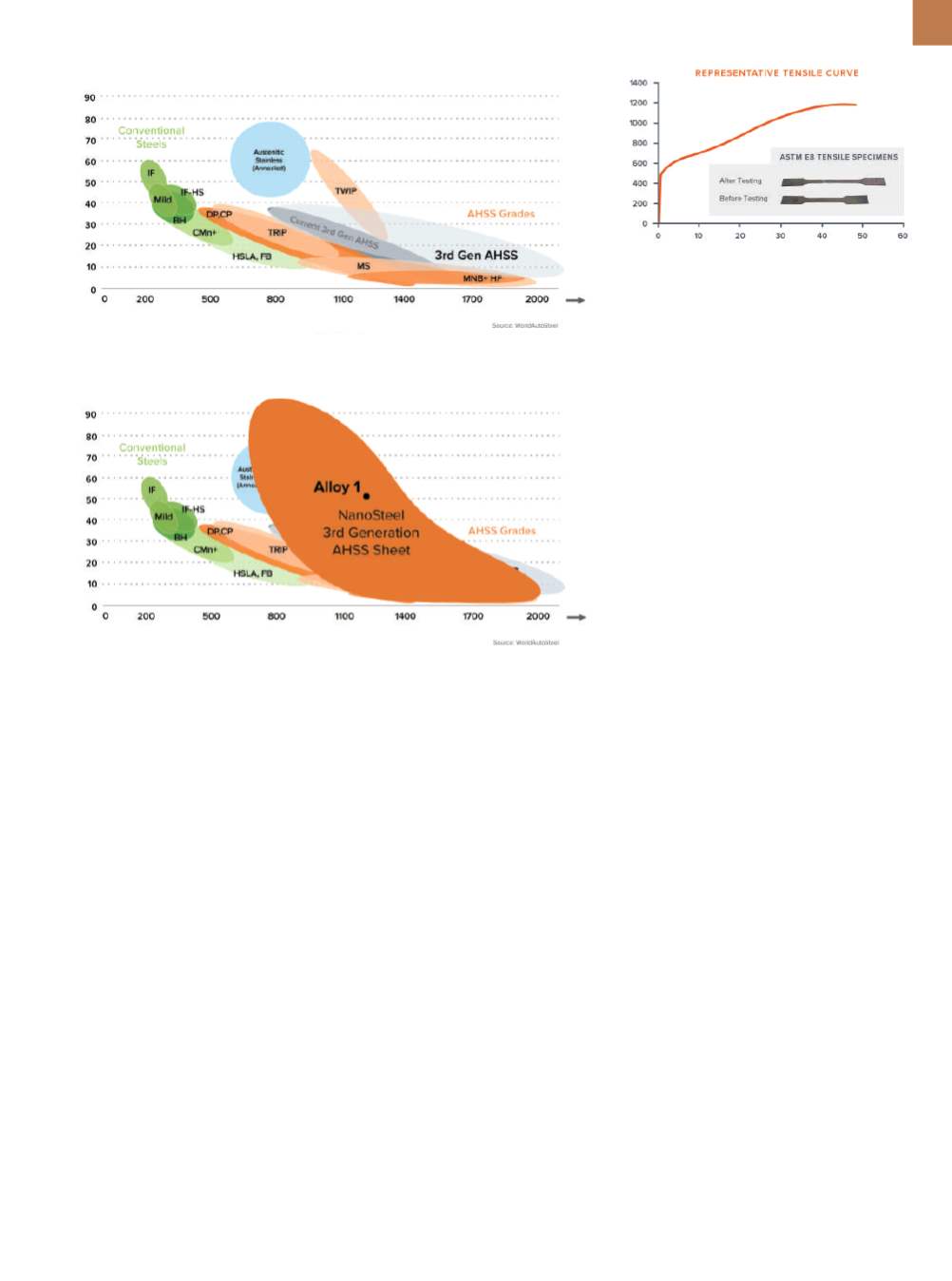
A D V A N C E D
M A T E R I A L S
&
P R O C E S S E S | J U L Y / A U G U S T
2 0 1 6
2 3
strength and ductility are possible, as
seen in Fig. 3. This article focuses on
one sheet steel design produced from
example Alloy 1.
TARGETED MICROSTRUCTURE
FORMATION
The properties of each alloy
depend on the chemistry as well as spe-
cific steel mill processing parameters.
For example, Alloy 1 has a proprietary
iron-based alloy chemistry that, when
processed, results in ultimate tensile
strength of roughly 1200 MPa with aver-
age elongation of 50% (Fig. 3) as seen in
the tensile stress-stain curve in Fig. 4.
The two microconstituents that
comprise these alloys enhance prop-
erties through their ability to act syn-
ergistically.
Microconstituent A
consists
of micron-sized austenitic grains with
dislocation networks and nanopre-
cipitates. This constituent, with its
larger grain sizes, mainly supports high
ductility in the final steel with strength-
ening through nanoprecipitation.
The second component,
microcon-
stituent B,
is comprised of nanoscale
ferritic grains with nanoprecipitates
that form during deformation. This pro-
vides strength due to the combination
of nanoscale grain sizes and nanopre-
cipitation with both the austenite and
transformed ferrite contributing to
ductility. These two components (~50%
each) in the
mixed microconstituent
structure of Alloy 1 can be seen in Fig. 5.
PROCESSING AND
FINAL PROPERTIES
The way in which industrial steel is
made is a key factor in the mixed micro-
constituent structure formation in the
final sheet. In the steel mill, an alloy is
continuously cast into slabs using stan-
dard high-throughput mill equipment.
The cast alloy then solidifies into den-
dritic structures with austenite grains
and interdendritic pinning phases con-
taining nanoprecipitates (Fig. 6). The
properties at this point demonstrate
tensile strength of around 600 MPa and
elongation below 15%.
In the next stage, slabs are heated
in the tunnel furnace to within 50-100°C
of the melting point. Hot rolling the
slab reduces thickness and forms a
hot band, which is then air cooled and
spooled into a coil. The hot-band mate-
rial structure is seen in the second stage
of Fig. 6 (the nanomodal structure). The
nanomodal structure sees significant
structural refinement taking place as
grain size is reduced, leading to signif-
icant property improvement. At this
stage, the hot band material features
the required tensile strength of about
1200 MPa and elongation over 40%.
Next comes cold rolling, where
material strength is further developed.
Cold rolling is done in multiple passes,
depending on the starting thickness
of the hot band and desired thick-
ness of the cold rolled sheet. The high
strength nanomodal structure of the
resulting cold rolled sheet occurs due
to extensive deformation through dis-
location mechanisms with phase trans-
formation. The structure consists of
transformed nanoscale ferrite grains,
retained austenite, and nanoprecipi-
tates. The effect of this phase transfor-
mation is demonstrated by increased
strength, in the case of Alloy 1 to over
1600 MPa with an associated reduction
in elongation to about 15%.
At this point, the material must be
annealed to restore ductility before it
can be used in an automotive structural
Fig. 2 —
WorldAutoSteel banana plot with target properties for third generation AHSS.
Fig. 3 —
Modified WorldAutoSteel banana plot with property ranges achievable through a new
approach to developing third generation AHSS.
Fig. 4 —
Tensile stress-strain curve for Alloy 1
and view of corresponding ASTM E8 tensile
specimens before and after deformation.
Elongation, %
Tensile strength, MPa
Elongation, %
Tensile strength, MPa
Engineering stress, MPa
Engineering strain, %