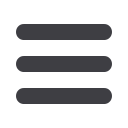
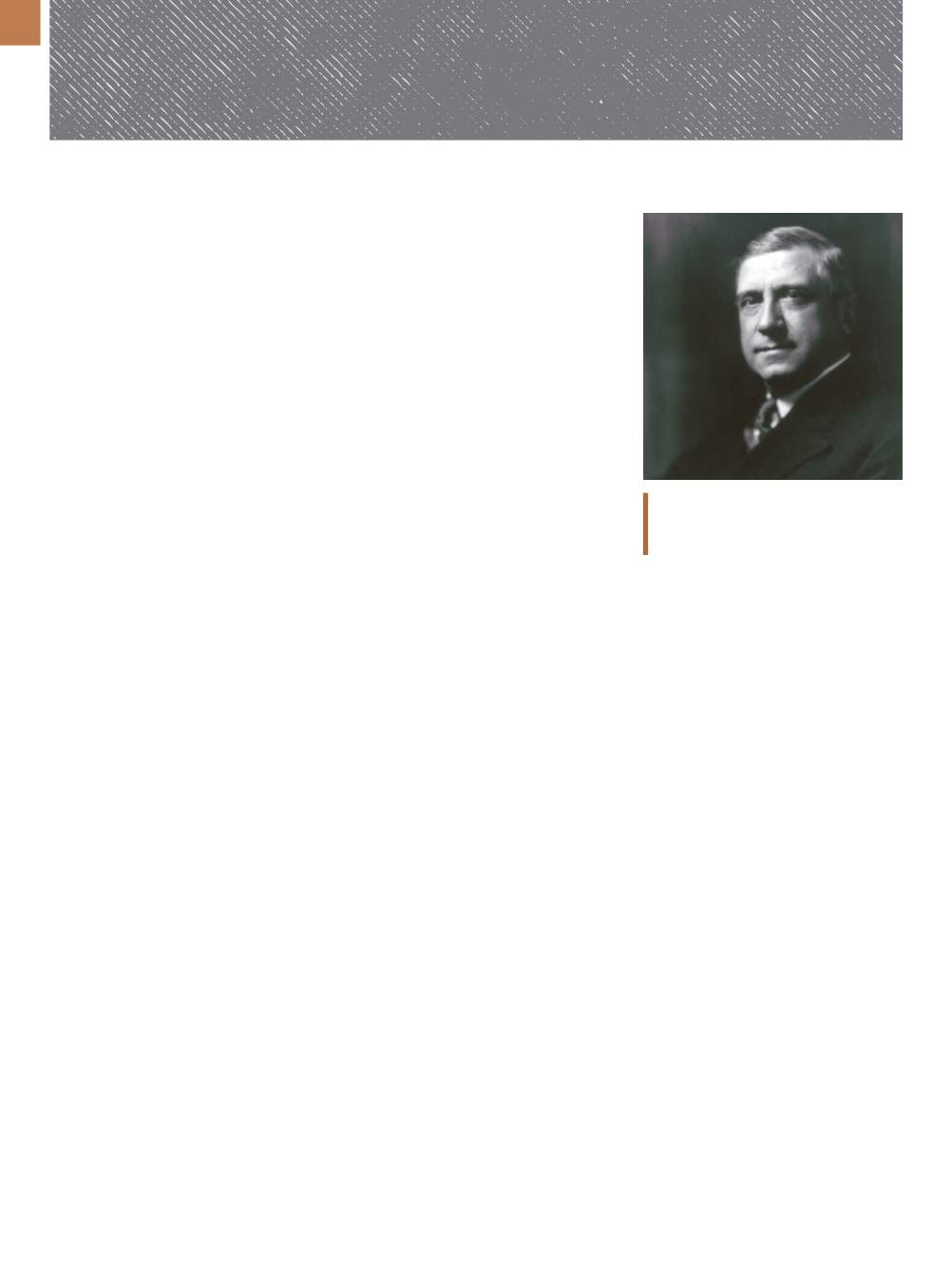
A D V A N C E D M A T E R I A L S & P R O C E S S E S | J U L Y / A U G U S T 2 0 1 6
2 6
METALLURGY LANE
Metallurgy Lane, authored by ASM life member Charles R. Simcoe, is a continuing series dedicated to the early history of the U.S.
metals and materials industries along with key milestones and developments.
THE INTEGRATED STEEL INDUSTRY—PART II
INTEGRATION OF THE STEEL INDUSTRY CONTINUED
WITH THE RISE OF BETHLEHEM STEEL CORP.
B
ethlehem Steel Corp. debuted as
Bethlehem Iron Co. in 1860 with
blast furnaces and rolling mills
for wrought iron railroad rails. The com-
pany hired John Fritz fromCambria Iron
Co. in Johnstown, Pa., as general man-
ager. After making iron rails for several
years, Bethlehem contracted with Alex-
ander Holley to build one of the first
Bessemer plants to convert to steel.
They installed four Bessemer convert-
ers and new rolling mills for steel rails.
The plant went onstream in 1873 with
annual capacity of 35,000 tons and a
reputation as the finest plant in the U.S.
However, it was a small plant and
its eastern location was problematic as
rail use was moving west. Under Fritz’s
leadership, the company built facilities
for making large forgings and heavy
plate, including armor plate for the
Navy. Previously, these products were
imported from England and Germany
due to a lack of domesticmanufacturers.
BethlehemSteel was soon recognized as
a producer of ship propeller shafts, large
gun barrels, and heavy battleship armor
equal to any provided from overseas.
The principals put the company up
for sale after the turn of the 19th cen-
tury. Charles Schwab bought 160,000
shares—giving him controlling inter-
est—while he was still president of U.S.
Steel Corp. When he was forced out of
“The Corporation,” he turned his full
attention to developing Bethlehem
Steel from a minor steelmaker into a
competitor to his former company. The
sale included several shipyards that
became a large part of Bethlehem’s
future production and profits.
When World War I started in
1914, the federal government passed
a Neutrality Act to keep the U.S. from
becoming involved in the conflict. This
prevented trade in armaments with
England, France, and Russia. Schwab
ignored the act, as did many other com-
panies, and received orders for gun bar-
rels, armor plate, and ammunition from
all three allies. Bethlehem Steel opened
a munition plant to supply this overseas
trade and as the war continued over four
years, it became the largest manufactur-
ing plant in artillery shells in the world,
making 750,000 shells per month. In
addition, it produced 60% of all finished
guns built for the U.S. market.
GROWTH AND PROFITS
DURING WWI
The company shipped 6 million
tons of steel during the war period and
went from 15,000 to 94,000 employ-
ees. The shipyard received orders for
freighters and destroyers, significantly
adding to profits. Earnings in 1916 were
$62 million, with Schwab receiving
$2.4 million in dividends and new
stock worth $17 million. With these
wartime profits, Bethlehem purchased
the Pennsylvania Steel Co. for $32 mil-
lion. They acquired the Steelton plant
built by Edgar Thomson and Tom Scott
during the age of Bessemer Steel and
a newer deep-water plant at Sparrows
Point, Md. Bethlehem now had annual
capacity of 2.2 million tons, exceeding
all competitors except U.S. Steel. In the
last two years of the war, Bethlehem’s
earned income was $111 million.
ACQUISITIONS DURING
THE 1920s
Bethlehem used its wartime prof-
its to acquire other steel companies.
In 1922, the company purchased the
Lackawanna Steel Co. outside Buffalo,
N.Y., for $54 million—raising its annual
capacity to 5.5 million tons. A year later,
it bought the Midvale Steel Co. for $95
million, which included Cambria Steel
where John Fritz had invented the three-
high rolling mill and William Kelly had
worked on his air blowing process. Beth-
lehem renamed Cambria Steel the John-
stown Mill. The addition of both Midvale
and Johnstown increased Bethlehem’s
annual capacity to 10 million tons.
Integrating these various steel
operations to improve efficiency and
lower overhead cost proved to be a
greater challenge than expected. This
would require a major effort during the
following two decades, as Bethlehem
had acquired older plants in need of
significant maintenance and upgrad-
ing. As part of the work, the company
modernized and added capacity to the
Sparrows Point plant, which became
one of the largest in the country.
THE GREAT DEPRESSION
As industry collapsed during the
Great Depression, steel shipments
reached lows not seen during the previ-
ous 20 years. In 1932, Bethlehem oper-
ated at just 20% of capacity with a loss
of $19million. When the recovery started
Charles M. Schwab, former president of
Carnegie Steel, was CEO of Bethlehem
Steel from 1904 to 1939. Circa 1918.