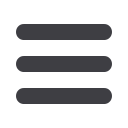
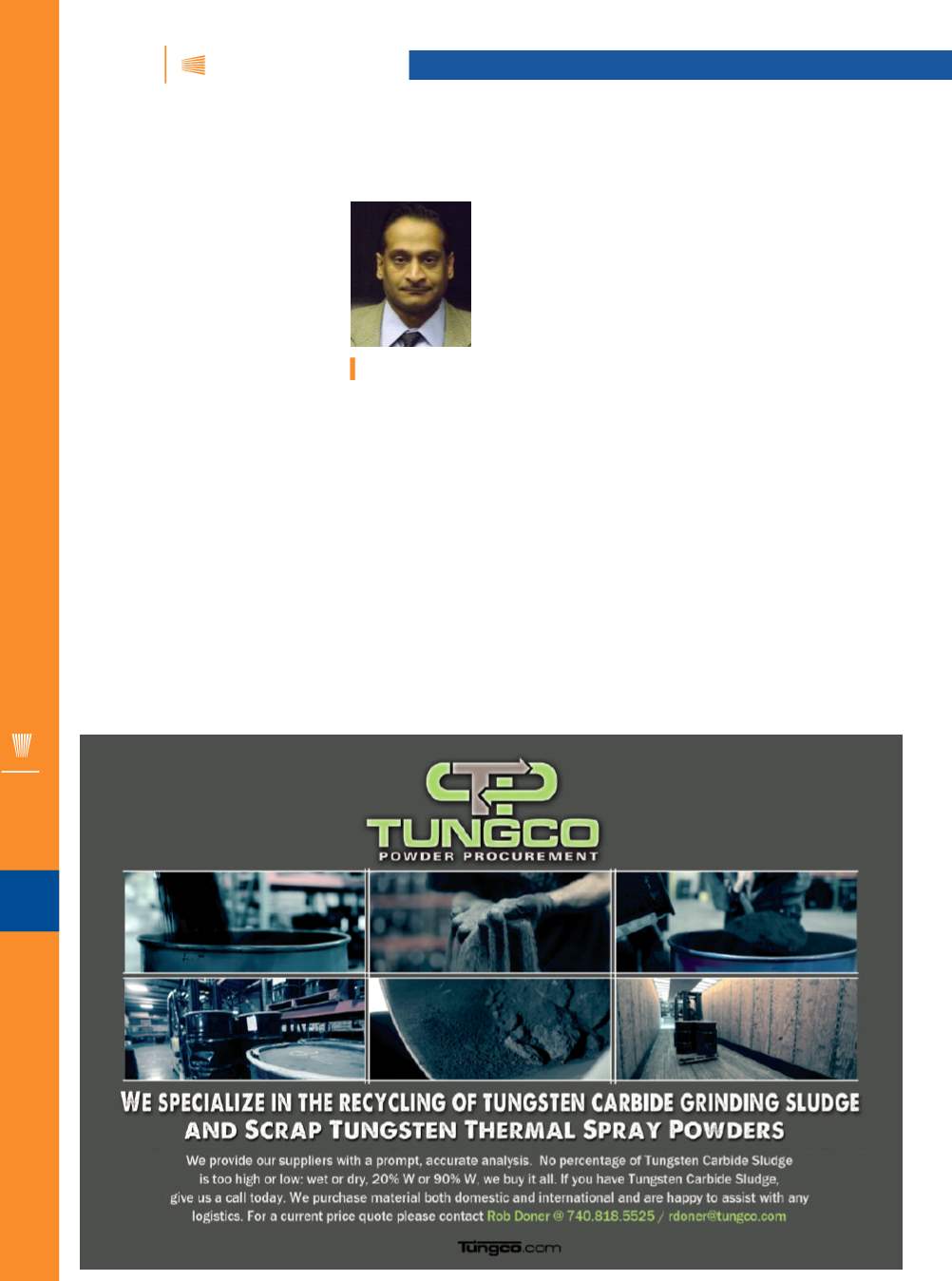
EDITORIAL
iTSSe
TSS
A D V A N C E D M A T E R I A L S & P R O C E S S E S | J U L Y / A U G U S T 2 0 1 6
3 2
iTSSe
TSS
2
THERMAL SPRAY SEES AUTOMOTIVE
SECTOR GROWTH
T
he ITSC 2016 conference and expo-
sition took place in May in Shang-
hai, and featured various sessions
on using thermal spray in automotive
and industrial applications. The plenary
lecture by Andreas Gollwitzer of BMW
titled “The Development of the China
Auto Market and its Significance for the
BMW Group” reflects the importance of
increased use of thermal spray in the
automotive industry. AsGollwitzer points out, BMWsawa com-
pounded annual growth rate of 28%between 2009 and 2015.
Further, ITSC’s automotive session included five papers
with subjects ranging from new technology to manufacture
ball bearings to thermal barriers to cold spray for reactive
brazing and the implementation of highly integrated industrial
manufacturing lines for spraying of cylinder blocks.
Improving coating density is important for industrial
applications in severe service such as pumps and valves
operating in highly corrosive and/or erosive environments.
Here, technology is evolving based on deposited materials.
Cermets, such as cemented carbides, lend particularly well
to deposition, using extremely fast velocities such as from
high velocity air fuel (HVAF) and newer higher firing rate det-
onation systems.
Further advantages of higher velocity systems include
improved adhesion and generally lower oxidation and disso-
lution of carbides. Dense, low oxide containing metallic alloys
can be applied using HVAF, but at times refractory metal-
lics and alloys such as tantalum or molybdenum are better
applied using shrouded or chamber contained plasma sys-
tems. This is particularly true when spraying at steep angles
where particles deposited using high velocity systems have a
tendency to slide.
Plasma spray remains the predominant method of
applying ceramics with amove toward systems with improved
voltage and current control, such ascascaded guns and pulse
width modulated power systems. Here, the lower power fluc-
tuations result in more stable thermal and velocity history for
particles, leading to improved coating properties.
I hope that future conferences will emphasize broader
application ranges for thermal spray. For example, it would
be interesting to see nuclear engineering for both power and
medicinal applications covered more thoroughly. Dual fabri-
cation of sensors and packaging, as well as coatings that func-
tion as catalytic surfaces, are also hot topics.
Rajan Bamola
iTSSe
co-editor
Surface Modification Systems Inc.
Bamola