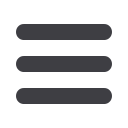

A D V A N C E D
M A T E R I A L S
&
P R O C E S S E S | J U L Y / A U G U S T
2 0 1 6
2 7
Eugene Grace (hand on face) testifying
before Congress in 1955. Grace was
president of Bethlehem Steel from
1916-1945 and chairman of the
board from 1945-1957.
the high production and profits they
had enjoyed for 10 years had come at an
unsustainable cost. While the domestic
steel industry was busy building new
capacity with the open hearth process
that had dominated steelmaking for
over 50 years, new technology was com-
ing onstream in Europe and Japan. First
was the basic oxygen furnace (BOF),
which used oxygen blown through the
heat of molten metal to convert it to
steel. This novel process could convert
cast iron from the blast furnaces to steel
in 45 minutes compared with 8 hours in
the open hearth. The process had been
invented in Austria and was installed in
other countries as new open hearths
were erected at Sparrows Point. One
small U.S. producer, McClouth Steel
Co., had built a 35-ton unit in 1954 and
Jones and Laughlin Steel Co. built sev-
eral in 1959. This would leave the two
biggest steel companies in the U.S.
with new open hearth shops that would
become obsolete in the 1960s.
The second new technology that
was developing overseas was the con-
tinuous casting machine. Molten metal
from the steelmaking furnaces was
ladled into a machine that allowed
solidification as it moved through the
unit and a semifinished product left the
machine. This process eliminated the
old system of casting molten metal into
large ingots that had to be reheated and
reduced to semifinished products either
by forging or in a rolling mill. Bethlehem
Steel would require many years and
billions of dollars to convert its mills to
these new processes.
For more information:
Charles R.
Simcoe can be reached at crsimcoe1@
gmail.com.
Bethlehem Steel supplied the steel and built the Golden Gate Bridge, which
opened in 1937. Courtesy of Ryan J. Wilmot/Wikimedia Commons.
Bethlehem Steel’s corporate headquar-
ters in Bethlehem, Pa.
The USS Massachusetts (BB-59) was
built at the Bethlehem Fore River
Shipyard during WWII.
in 1933 and beyond, the increased busi-
ness was in lighter flat-rolled products
for the automobile and appliance mar-
kets in the Midwest. Bethlehem only
had one mill that could reach this mar-
ket—the Lackawanna plant where the
company had installed continuous hot
rolling mills for sheet in 1937.
CONTRIBUTIONS
DURING WWII
With the start of WWII in Europe,
Bethlehem received $300 million in
orders from England. (Recall that it was
production for overseas orders during
WWI that allowed Bethlehem to accu-
mulate excessive profits.) This time,
orders went through the War Production
Board instead of J.P. Morgan in London,
therefore limiting profits. During WWII,
Bethlehem’s greatest contribution was
in its shipyards. Shipbuilding employ-
ment increased from 7000 to 182,000,
accounting for 95% of employment
growth for the entire corporation. In
four years, Bethlehem built 1127 ships,
produced 73 million tons of steel, and
furnished the Navy with one-third of its
needs for armor plate and gun forgings.
1950s SEES RENEWED GROWTH
The 1950s were very productive
and profitable for the steel industry, as
demand for steel exceeded that of WWII.
At times, Bethlehem operated at 100%
of capacity with an average of 150,000
employees. Total net income for the
period 1950-1959 was $1.37 billion. With
these reserves, the company added
5 million tons of steel to its annual
capacity, bringing the total to 20 million
tons. In 1954, Bethlehem attempted to
acquire Youngstown Sheet and Tube
to gain additional markets in sheet
products in the Midwest. However, the
merger was prevented by the Justice
Department on grounds that it would
violate the ClaytonAntitrust Act. In 1956,
Bethlehem announced a program to
expand production to 23 million annual
tons. Two million would be at Sparrows
Point, increasing that plant to 8 million
tons with a 10th blast furnace and a new
open hearth shop. When expansion was
complete in 1958, Sparrows Point was
the largest steel mill in the world. All of
this optimism was based on steel con-
sumption continuing well into the next
decade or two.
However, in early 1959 the entire
steel industry failed to understand that