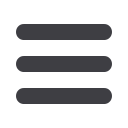
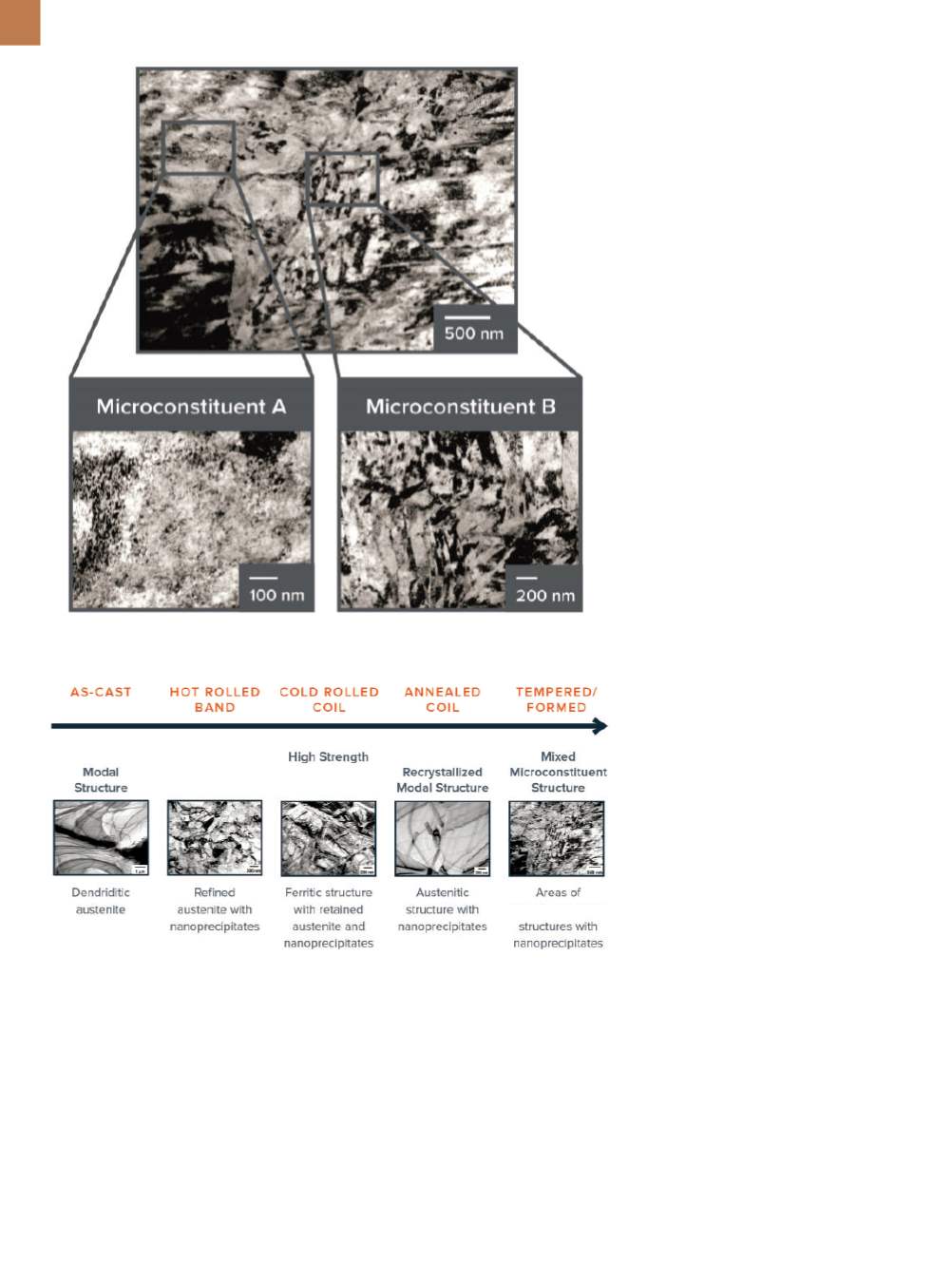
A D V A N C E D M A T E R I A L S & P R O C E S S E S | J U L Y / A U G U S T 2 0 1 6
2 4
Mixed microconstituent structure
formation occurs during steel manufac-
turing and also during the automotive
part manufacturing process—stamp-
ing, roll forming, or hydroforming.
Microconstituents generated during
deformation provide high formability
to achieve complex shapes as well as
high strength.
The complete microstructural
pathway of this new sheet steel alloy—
from the as-cast modal structure to
the final mixed microconstituent struc-
ture—occurs through typical com-
mercial sheet steel processing steps
and does not require additional meth-
ods such as rapid solidification or
quenching.
CONCLUSION
Aggressive fuel economy regula-
tions including U.S. Corporate Aver-
age Fuel Economy (CAFE) standards
have spurred the automotive market
to incorporate alternative materials
such as aluminum and composites
and create clear targets for third gen-
eration AHSS to meet the industry’s
lightweighting goals. By effectively
mitigating the historical paradox
between strength and ductility, Nano-
Steel’s alloy design pathway enables a
new family of automotive sheet steel
to meet these requirements. These
new steels are expected to offer auto-
makers affordable structural design
options that can substantially reduce
vehicle weight for more fuel efficient
cars and trucks.
For more information:
Daniel J. Brana-
gan is chief technology officer, Nano
Steel, 272 W. Exchange St., Suite 300,
Providence, RI 02903, 401.270.3549,
dbranagan@nanosteelco.com,www.
nanosteelco.com.
References:
1. D.J. Branagan, et al., “3rd Generation
AHSS: From Promise to Reality,” Invited
talk, MS&T, October 4-8, Columbus,
Ohio, 2015.
Fig. 5 —
Targetedmixedmicroconstituent structure in Alloy 1, leading to third generation AHSS
with novel properties.
Fig. 6 —
Alloy 1 structural development through the major steel processing stages leading to
the final third generation AHSS structure.
design. On an industrial scale, anneal-
ing can be either continuous or batch.
This heat treatment results in alloy
recrystallization, which removes cold-
work effects andprovides a phase trans-
formation of ferrite back to austenite.
When the recrystallized sheet structure
deforms, the targeted mixed microcon-
stituent structure is formed, resulting
in the desired combination of tensile
strength at ~1200 MPa with elongation
above 45%.
Nanomodal
Struture
austenitic and ferritic
Nanomodal
Struture