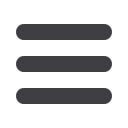
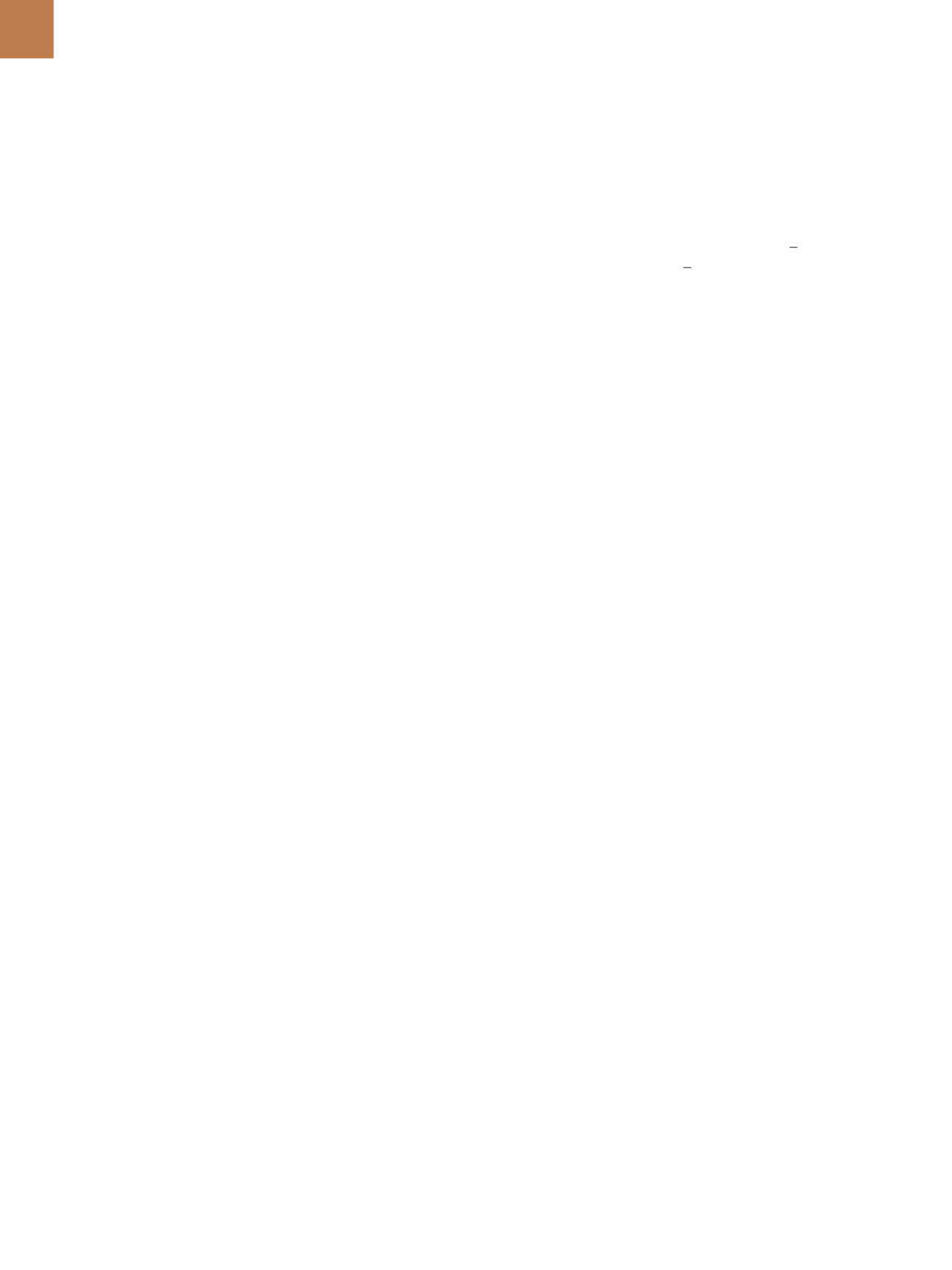
A D V A N C E D M A T E R I A L S & P R O C E S S E S | A P R I L 2 0 1 5
3 0
stored energy required to drive the re-
crystallization. Moreover, the volume of
material associated with contraction/
double twinning is favorably oriented
for basal slip
[23]
. This results in localiza-
tion of slip within the twinned regions
and, as a result, high stored energy. It
could also lead to eventual formation
of shear bands
[21]
.
Orientation of grains nucleating at
contraction and double twins are dif-
ferent than the initial texture of the ma-
terial
[14]
. This affects the overall recrys-
tallized texture, but only for the initial
annealing stage. On further annealing,
this effect diminishes and finally arrives
at incomplete recrystallization. One hy-
pothesis is the occurrence of immense
recovery prior to recrystallization,
which absorbs most of the stored en-
ergy of the deformed sample. Also, the
nuclei originating from the twins grows
very slowly, thereby failing to consume
the entire specimen. As a consequence,
nucleation starts occurring at the grain
boundaries that have an attribute of
retaining the initial texture of the ma-
terial. Nevertheless, it appears that
in order to have an observable effect
on recrystallization texture of mag-
nesium, the number of contraction/
double twins per unit area of the de-
formed sample must be increased and
with less number of grain boundaries.
One way to accomplish this is to in-
crease the initial grain size of the ma-
terial, because more twins are formed
in large-grained structures and will
also simultaneously decrease the grain
boundary area
[14]
. The other possibility
is to probe the significance of second
phase particles on contraction twin nu-
cleation and growth. Recent work
[24,25,26]
on precipitate-containing magnesium
alloys suggests that precipitates are
capable of increasing the number and
density of extension twins, but restrict-
ing their growth.
In many alloy systems, large par-
ticles or dispersoids were used to suc-
cessfully modify grain structure by
affecting the recrystallization process
and recrystallization texture via parti-
cle simulated nucleation (PSN)
[27]
. The
size, spacing, and amount of particles
are key parameters that can affect the
recrystallization process
[28]
. Very few
attempts have been made to study the
significance of the effect of dispersoids
and these variables on the recrystalli-
zation of magnesium alloys. The effect
of large Mn-rich dispersoid particles
(size > 1 µm) on recrystallization of Mg-
Mn alloy was studied by Robson and col-
leagues
[27]
. Their results suggest that the
matrix surrounding the particles under-
goes a rotation, which is consistent with
that observed in other alloy systems
where PSN occurs. The new recrystal-
lized grainswere formed in the deformed
zone around the hard particle. The ori-
entation of those grains was significantly
different from the parent orientation of
the grain. However, the overall density of
such grains was so small that their effect
on global texture was minimal.
One key issue highlighted above
is the incomplete recrystallization in
magnesium alloys. This is often at-
tributed to insufficient stored energy.
However, with recent alloying efforts
(e.g., Y, Gd, Li, etc.)
[16,12,29]
and strain path
changes (e.g., cross rolling, multidirec-
tional forging)
[10,13]
, it is possible to store
higher energies at low temperatures.
For example, AZ31 magnesium alloy
accommodated an equivalent strain up
to 0.77 by cross rolling
[10]
. The greater
the amount of stored energy, the faster
the recrystallization kinetics. The same
work also shows that at higher strains
other potent sites for nucleation such as
twin-twin interactions, as well as twin
grain boundary interactions, increase
substantially
[10]
. Grains originating from
these sites also exhibit widely different
orientations, providing an opportunity
to alter recrystallization texture.
GRAIN GROWTH
IN MG ALLOYS
Generally, recrystallized grains in
magnesium undergo abnormal grain
coarsening
[30,31]
. Under certain circum-
stances, some grains grow excessively
compared to others and can increase in
size to a few centimeters. This phenom-
enon is referred to as abnormal grain
growth, secondary recrystallization,
or discontinuous grain coarsening
[17,18]
.
Abnormal grain growth occurs either
when normal grain growth is obstruct-
ed or some grains have specific favor-
able features for growing faster than
their neighbors. Many factors can cause
abnormal grain growth, such as pres-
ence of second-phase particles, texture,
and surface effects
[17,18]
.
Magnesium exhibits abnormal
grain growth behavior when subjected
to severe annealing conditions, i.e., at
high temperatures and for prolonged
heating periods
[30,31]
. According to Perez
et al.
[31]
, grains with {1120} orientation,
i.e., {1120} plane of grains parallel to the
sheet plane surrounded by grains with
basal texture, give rise to a boundary
of high misorientation and mobility.
This allows specific grains to grow fast-
er than others. The reason is that in a
strongly textured material, the HAGBs
exist between prismatic and basal
planes having higher energy and mobil-
ity as compared to other grain bound-
aries, thus helping the former to grow
faster. In some cases, even under mod-
erate annealing conditions, magnesium
reveals secondary recrystallization in
specific areas, for example, the outer
surface of an extruded sheet
[30]
.
When an extruded AZ31 magne-
sium alloy is subjected to annealing
at 450°C for three hours, the outer sur-
face witnesses abnormal grain growth
(Fig. 3). A texture gradient occurs along
the thickness of the sheet. In compari-
son to inner layers, the outer surface ex-
periences a large amount of shear, thus
more stored energy is available to initi-
ate abnormal grain growth. In another
study, grain growth kinetics were inves-
tigated on an AZ31 magnesium alloy in
the 350° to 450° C temperature range
[32]
and no evidence of abnormal grain
growth was found. This implies that
there must be some critical temperature
above which abnormal grain growth oc-
curs in magnesium. It should be noted
that compared to other light metals such
as Al, very limited information is avail-
able on the role of solute elements and
precipitate particles on abnormal grain
growth in magnesium alloys.
SUMMARY
The recovery process has a strong
influence on the recrystallization phe-
nomenon. However, current under-
standing of recovery in magnesium and
its alloys is very limited. This incomplete
understanding suggests that recovery