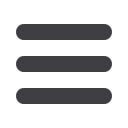
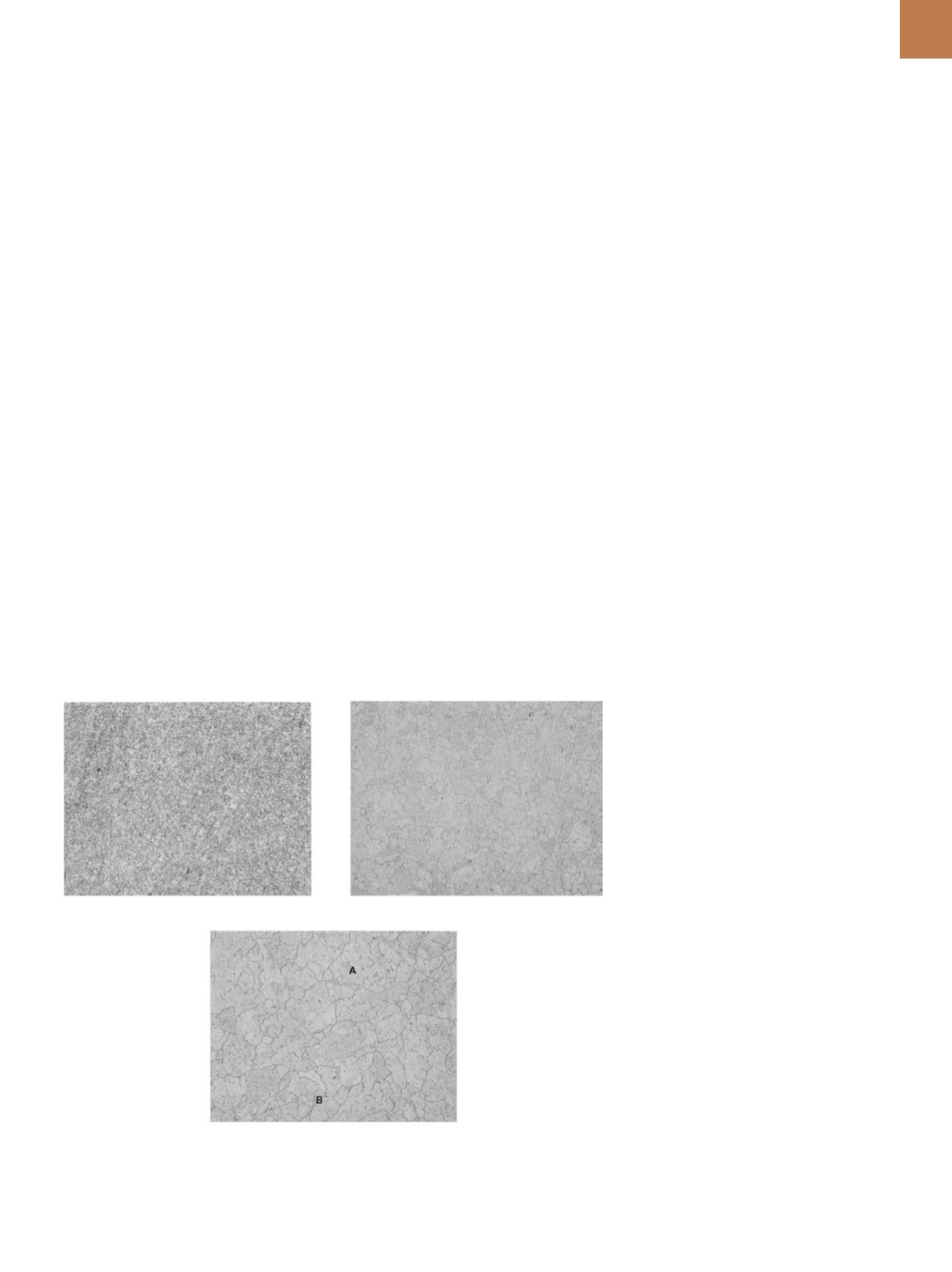
A D V A N C E D
M A T E R I A L S
&
P R O C E S S E S |
A P R I L
2 0 1 5
2 5
PRODUCT CONTAMINATION
A manufacturer of industrial-scale
bakery equipment was advised of a
problem where bread rolls produced
in its equipment were contaminated
by black marks on the bread’s surface
(Fig. 1). Relevant questions in this case
include: Is contamination on bread rolls
related to the machine, operator, work
environment, or processing variables?
Is it a health hazard? The chemical
analysis of the contaminant was deter-
mined using Fourier transform infrared
(FTIR) spectroscopic analysis.
FTIR reveals that the black marks
are associatedwithburning/overheating
of corn meal used as a release agent in
the baking process. Further investigation
determined that the conveyor belt mesh
cleaning system was not effective in re-
moving excessive cornmeal that stuck to
the mesh, which eventually burned and
stuck to the dough surface and created
the black marks. Thus it is clear that the
black marks were not due to defects in
the manufacturing process, nor a faulty
design, but were caused by inadequate
maintenance of cleaning equipment du-
ring continuous operation.
PREMATURE HEATING
ELEMENT FAILURE
Heating elements failed in a furnace
that had a specified maximum operating
temperature of 1200°F, which translat-
ed to a heating element temperature of
1825°F. The user claimed the elements
failed even though the maximum tem-
perature of the furnace was never set
higher than 1200°F. Relevant questions
regarding this failure include: Is the heat-
ing element material at fault? Is it the
heat treater’s error? Is it due to a faulty
temperature sensor/controller? Is it due
to operator error of inadvertently setting
the furnace temperature too high? How
high did the temperature go before the
element failed? The answers to these
questions were determined using optical
metallography as shown in Fig. 2.
The heating element material was
a Ni-Cr-Fe base electrical-resistor ma-
terial containing 0.014% Ti, 0.043% Nb,
0.029% C, and 0.006% N. Microalloy
precipitates coarsen or melt
[2-6]
at high
temperatures and therefore do not pre-
vent grain growth, which sometimes
leads to abnormal growth. The tem-
perature of the elements must have
exceeded 1900°F for niobium nitride/
carbonitride precipitates in this materi-
al to go into solution. The normal heat-
ing element operating temperature was
1825°F maximum, meaning the heating
element probably failed due to abnor-
mal operating conditions of excessive
furnace temperature, either due to a
faulty temperature setting or faulty tem-
perature sensor/controller.
INJECTION NOZZLE
FATIGUE FAILURE
Metal quality is an important fac-
tor in machine component failure, such
as the injection molding machine at
the center of this case. Visual and ste-
reomicroscopic examination of crack
interfaces of the component revealed
that cracking occurred due to metal fa-
tigue initiated at multiple locations on
the fillet radii of two threads on the out-
side surface (Fig. 3). Fracture surfaces
did not reveal any corrosion products,
abnormal contact patterns, or temper
colors, suggesting that component op-
erating conditions during service were
not aggressive.
Metallurgical examination indicat-
ed that the material’s heat treatment,
microstructure, hardness, and bulk
chemical composition met relevant
standards and drawing specifications.
However, a large cluster of coarse non-
metallic inclusions was observed at one
location in the microstructure (Fig. 4).
Scattered, large inclusions were also ob-
served in other locations. Electron mi-
croscopy of the fracture surface reveals
a large number of secondary-phase par-
ticles and inclusions clustered around
crack initiation regions. Most of these
particles contained Cr, C, S, and Si, sug-
gesting that chromium carbide precipi-
tated on preexisting silicate and sulfide
inclusions.
One of the particles had a glassy
appearance and contained significant
amounts of C, K, and Ca. This particle
is most likely from the ironmaking op-
eration in the blast furnace. Sources for
K are iron ore and coke ash, while Ca
comes from the basic flux, such as lime
(CaO) used for desulfurizing iron. Large
clustered inclusions in a material signifi-
cantly decrease its fatigue resistance and
toughness by serving as crack initiation
(a)
(b)
(c)
Fig. 2 —
(a) Microstructure of original heating element showing fine-grained austenite, mag:
100×; (b) microstructure of used heating element showing coarse-grained austenite, mag: 100x;
and (c) example of a mixedmicrostructure and abnormal grain growth in the failed heating
element (A = coarse grains, B = fine grains; mag: 200×). Etchant was modified Marble’s reagent
[1]
.