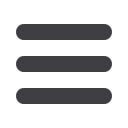
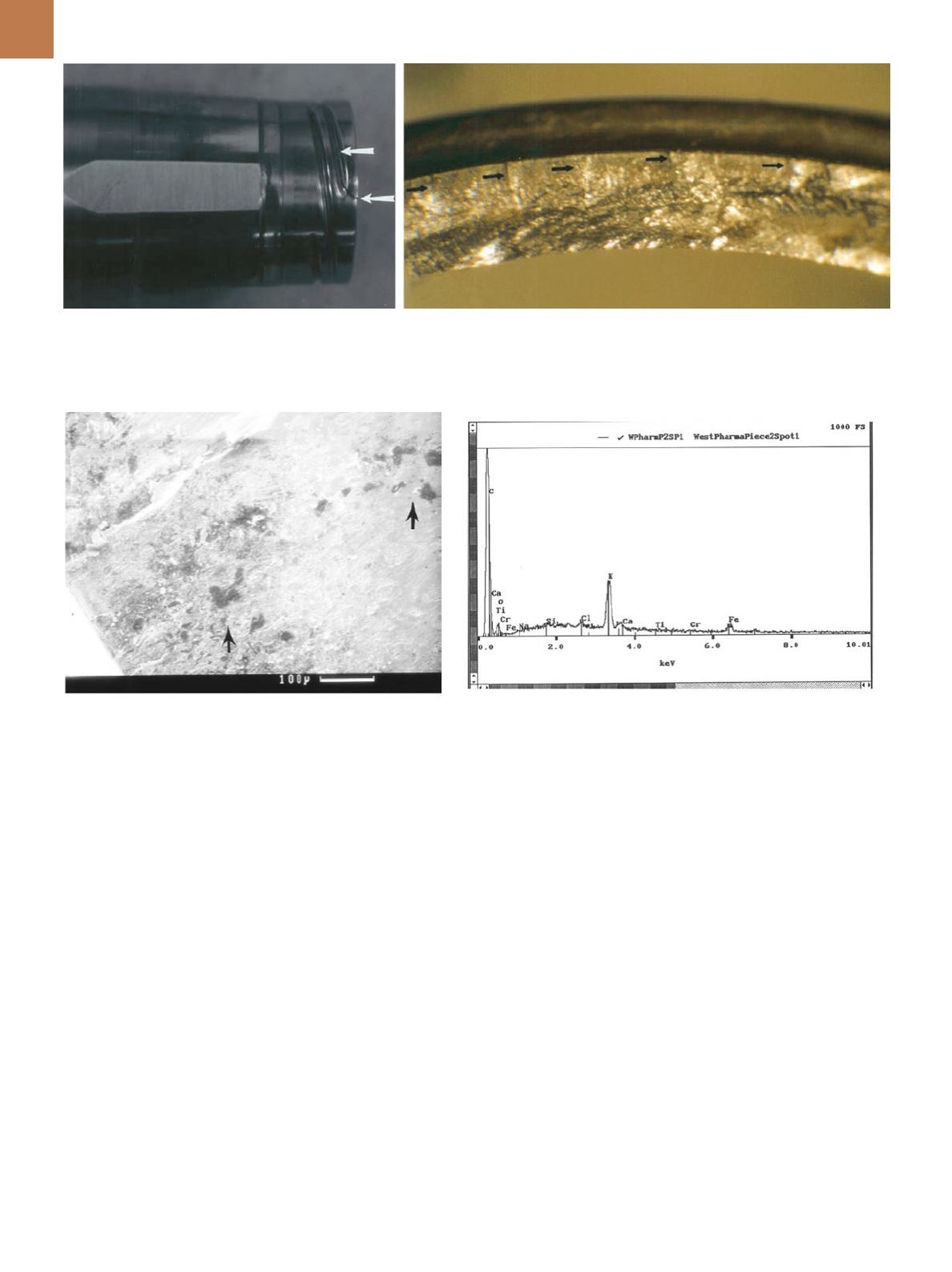
A D V A N C E D M A T E R I A L S & P R O C E S S E S | A P R I L 2 0 1 5
2 6
sites. Therefore, it was concluded that
fatigue cracking of the component was
facilitated by inadequate steel quality,
i.e., lack of cleanliness.
SHEAR OVERLOAD FAILURE
OF GAS PIPELINE BRACKET
A leaking underground gas pipe-
line resulted in a house explosion, caus-
ing grievous personal injury. The exca-
vated pipeline revealed that two pieces
separated, causing a massive gas leak.
Extensive failure investigations boiled
down to one question: Did the failure
occur over a period of time or was it due
to a single catastrophic event? Analysis
of the fracture surfaces of the brackets
Fig. 3 —
(a) Cracked injection-molding machine component, and (b) stereomicrograph of the crack interface revealing a multiple origin fatigue
failure suggested by ratchet marks (black arrows).
(a)
(b)
(a)
(b)
Fig. 4 —
(a) SEM image at failure initiation zone with a ratchet showing clusters of inclusions and precipitates (arrows), mag: 160×, and (b) energy
dispersive spectroscopy (EDS) spectrum of an inclusion indicates peaks for C, K, Ca, Cl, and Cr. This particle has probably come from the ironmaking
operation in the blast furnace where sources for K are iron ore and coke ash while Ca is from the basic flux, such as lime (CaO), used for desulfuriza-
tion of iron ore.
holding the pipes together provide the
answer. Figure 5 shows the fractogra-
phy of one of the brackets, clearly indi-
cating a sudden shear overload failure.
It was eventually concluded that the
pipeline pieces separated from each
other due a landslide event in the val-
ley not far from the location where the
pipeline was buried, and the failure was
mainly caused by the natural disaster
rather than human error.
~AM&P
For more Information:
P.A. Mano-
har is an associate professor, Robert
Morris University, Engineering Depart-
ment, John Jay 119B, 6001 University
Blvd., Moon Township, PA 15108-1189,
manohar@rmu.edu, www.rmu.edu.Acknowledgment
The author thanks Modern Indus-
tries Inc., Erie, Pa., for permission to
publish the photographs. The work was
carried out at the company’s Pittsburgh
laboratory.
References
1. G.F. Vander Voort and H.M. James,
Wrought Heat-Resistant Alloys,
Metallog-
raphy and Microstructures
, Vol 9,
ASMHandbook
, ASM International,
p 305-329.
2. K. Narita, Physical Chemistry of the
Group IVa (Ti, Zr), Va (V, Nb, Ta) and the
Rare Earth Elements in Steel,
Trans.
ISIJ
, Vol 15, p 145, 1975.