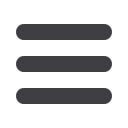
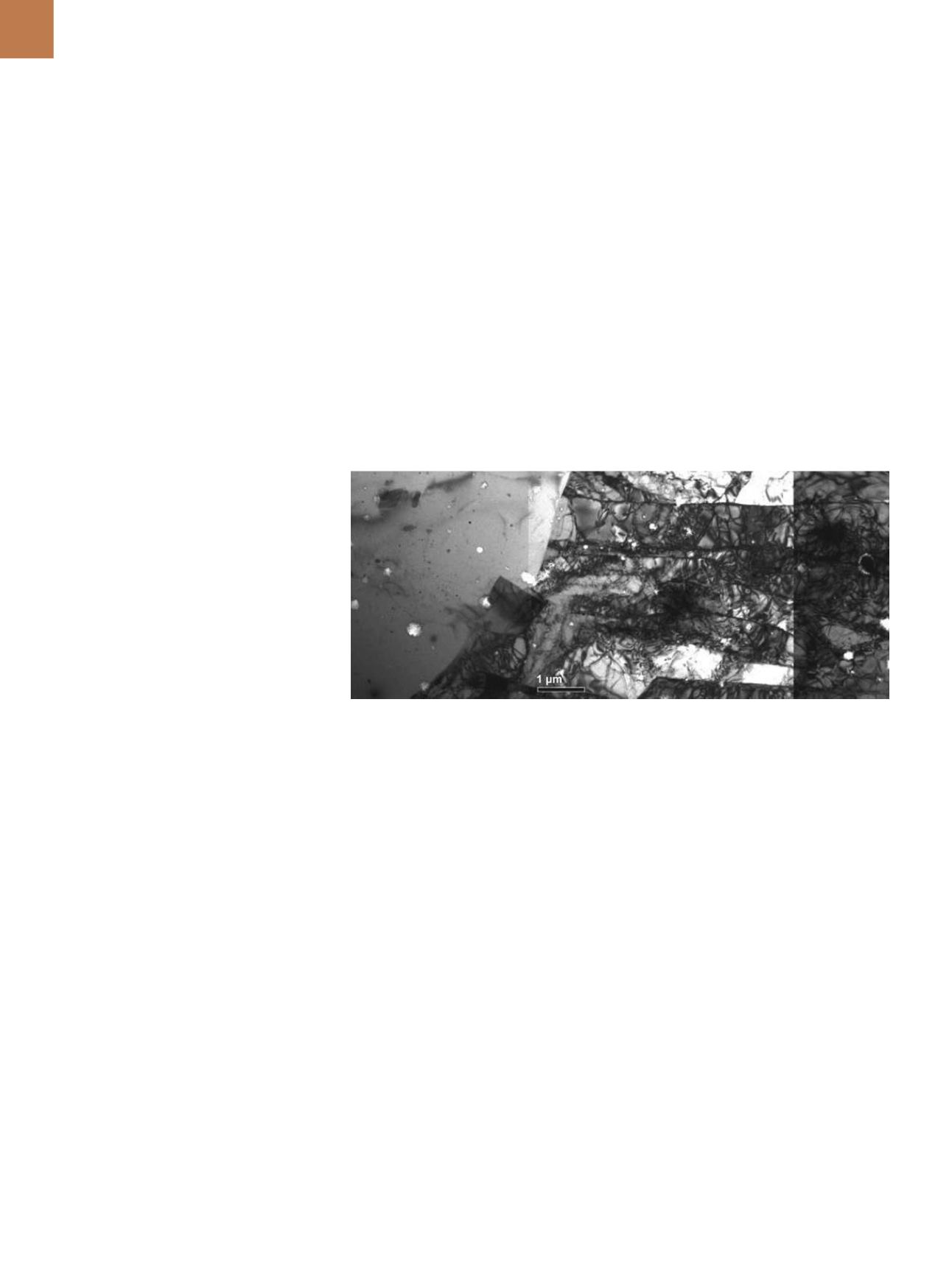
A D V A N C E D M A T E R I A L S & P R O C E S S E S | A P R I L 2 0 1 5
2 8
OVERVIEWOF STATIC
RECRYSTALLIZATION IN
MAGNESIUMALLOYS
This article presents a broad overview of key annealing processes such as recovery,
recrystallization, and grain growth in magnesium and its alloys.
Shanta Mohapatra
Jayant Jain
Indian Institute of Technology Delhi, New Delhi
M
agnesium and its alloys are re-
ceiving a lot of attention in to-
day’s structural and automotive
industries due their lightweight nature,
thus improving fuel economy and min-
imizing exhaust emissions
[1]
. However,
wider usage is restricted by limited form-
ability at room temperature due to their
hcp structure
[2]
. Grain refinement and
texture modification are considered to
be effective ways of improving magne-
sium’s poor formability performance at
room temperature
[3]
. Controlling grain
structure and crystallographic texture
can be achieved by thermally actuat-
ed processes such as recrystallization,
which can soften and restore the ductility
and formability of deformedmaterial.
The majority of research work to
date focuses on dynamic recrystalliza-
tion in wrought magnesium alloys
[4-7]
,
with comparatively little work on static
recrystallization
[8,9,10]
. This is mainly due
to the limited deformation capabilities
of magnesium alloys at low tempera-
ture. However, based on recent efforts
to improve ductility with alloying addi-
tions
[11,12]
and strain path changes
[10,13]
, it
is timely to review the experimental work
on static recrystallization in these alloys.
Note that no attempt is made to compile
the status of modeling and simulation
studies on recrystallization. This article
explores the role of recovery in recrys-
tallization behavior, evolution of recrys-
tallization microstructure and texture,
current understanding of grain coarsen-
ing in magnesium alloys, and concludes
with a perspective on future research.
RECOVERY
It is generally observed that mag-
nesium and its alloys exhibit incom-
plete recrystallization
[9,10,14]
. In most
cases, this is due to the occurrence of
intense recovery prior to recrystalliza-
tion
[9,10]
. The recovery process reduces
the system’s available stored energy,
thus keeping some grains from re-
crystallizing. The extent of recovery
depends on stacking fault energy
(SFE). Magnesium features a stacking
fault energy of 125 mJ/m2, very close
to metals like Al (166 mJ/m2) and Ni
(90 mJ/m2), therefore favoring an oc-
currence of intense recovery
[3]
. The
work of Okrutny
[15]
and subsequently
Liang
[10]
clearly demonstrates the for-
mation of subgrain structures in AZ31
magnesium alloys (TEM image, Fig. 1).
The addition of alloying elements
changes the SFE. For example, add-
ing Li and Gd to magnesium alters
the SFE, which eventually affects the
recovery kinetics
[12,16]
. The concept of
static recovery is not as thoroughly
studied in magnesium alloys com-
pared to other light metals like alumi-
num. For example, in aluminum alloys
the interaction of precipitates with
dislocations inhibits the recovery pro-
cess
[17]
. However, no such information
exists with regard to magnesium al-
loys. More work is required to explore
the recovery process as well as factors
that may affect the kinetics, leading to
better understanding of the recrystal-
lization phenomenon.
Fig. 1 —
TEM image illustrating the formation of sub-grain structures in AZ31 magnesium alloy
when deformed to a strain of ~0.1 followed by annealing at 250°C for 1800 s
[10]
.