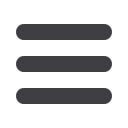
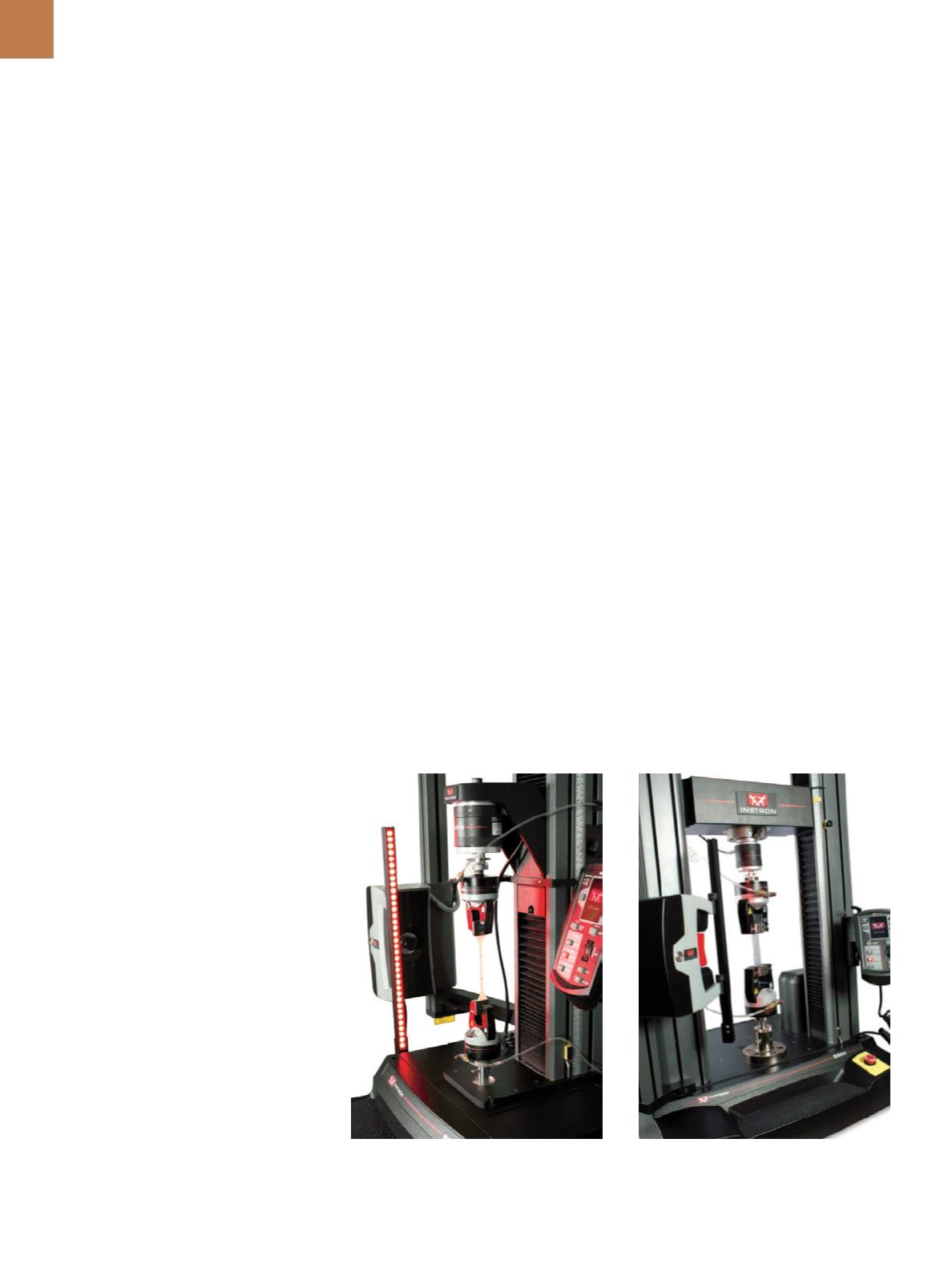
A D V A N C E D M A T E R I A L S & P R O C E S S E S | A P R I L 2 0 1 5
2 2
TECHNICAL SPOTLIGHT
NON-CONTACTING EXTENSOMETRY
EXCELS INSTRAINMEASUREMENT
S
tress and strain are the two funda-
mental components of a materials
test. When a material is put under
a compressive or tensile load,
stress
is the
load relative to the cross-sectional area
of the material, while
strain
refers to how
much it elongates. Both stress and strain
data provide important material charac-
teristics such as stiffness, yield stress or
yield point, ultimate tensile strength, and
total elongation. Many industries require
use of calibrated and verified equipment
tomeasureamaterial’sstressandstrain—
usually with a universal testing machine,
load cell, and an integrated extensometer
or strainmeasurement device.
Various extensometers are com-
mercially available for a wide range of
materials and provide accurate strain
data for specific applications. Often this
strain data must be of the highest ac-
curacy and repeatability, as many crit-
ical material characteristics depend on
accurate, early-in-test strain data. The
resulting characteristics can be used
as quality control benchmarks, and/or
material selection criteria in research
and development with great impact on
the final components.
TESTING STANDARDS
Most industries, such as polymer,
steel, and carbon fiber composite man-
ufacturing, have regulated procedures
for testing raw materials before they
can be sold. These processes are most
commonly governed by organizations
such as the International Organization
for Standardization (ISO), Geneva, and
ASTM International, West Conshohock-
en, Pa. Other standards organizations
exist globally and typically make small
adaptations to the most common ISO
and ASTM standards.
Testingstandardsvaryinstringency,
some requiring very low accuracy instru-
mentation and some requiring high ac-
curacy, high-resolution instrumentation
to characterize materials. The stringen-
cy usually correlates with the materi-
al’s end use. Composites, metals, and
polymer manufacturing tend to have
the strictest extensometry requirements
within the materials testing sector due
to the material’s stiffness and use in crit-
ical applications.
EXTENSOMETERS:
BASICS AND BENEFITS
Extensometry can be broken down
into two fundamental categories: con-
tacting and non-contacting. As their
names suggest,
contacting extensome-
ters
require contact with the materials
testing specimen, whereas
non-contact-
ing extensometers
use technologies like
video or lasers to measure elongation.
Non-contacting extensometry offers
a wide range of benefits in materials
tests. Depending on the specific ap-
plication, non-contacting extensom-
etry may be the only option for strain
measurement.
Non-contacting:
The most obvious
feature of non-contacting extensome-
try is that it does not come in contact
with the specimen during tests. This is
important for delicate materials, such
as biomedical tissues, paper, and even
some polymers. For some fragile ma-
terials, contacting extensometry can
affect important strain-based calcu-
lations like modulus or yield. Heavy
contacting devices can damage fragile
specimens causing them to bend and
deform during the test, and/or can dig
into the material’s surface with sharp
edges, causing weakening at contact
points and thus premature failure.
High accuracy:
Both BS EN ISO
6892-2:2011 and BS EN ISO 527-1:2012—
the two most common global tensile
testing standards—require very accu-
rate extensometry (ISO9513:1999 Class 1).
Non-contacting extensometer technolo-
gy uses a combination of lighting, fans,
and high-resolution digital cameras to
achieve the accuracy needed for these
Fig. 1 —
Polarized LED lighting on the
Instron AVE2 increases extensometer
accuracy by removing ambient light effects.
Fig. 2 —
Film testing conducted on the
Instron AVE2.