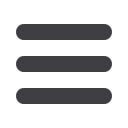
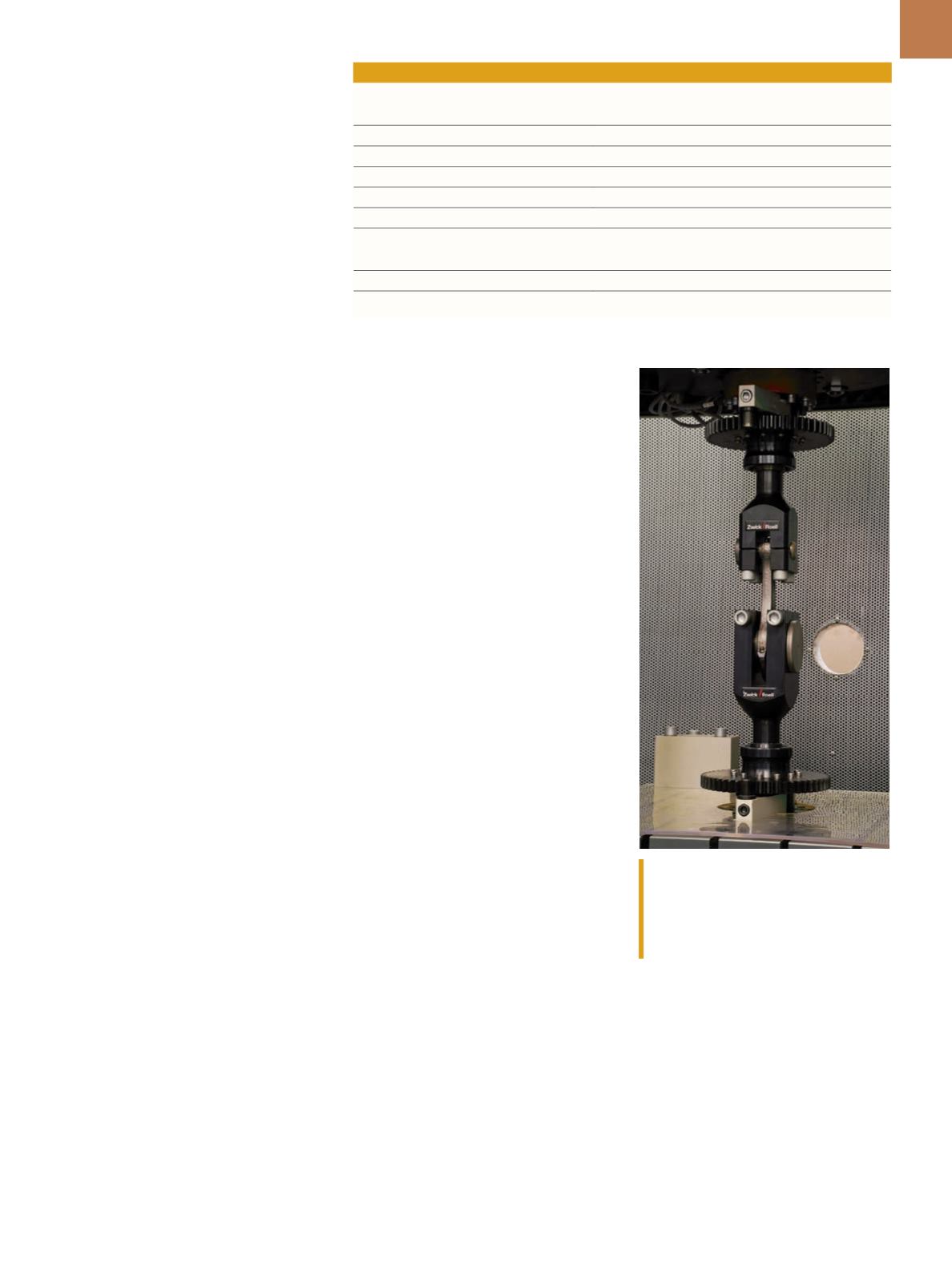
A D V A N C E D
M A T E R I A L S
&
P R O C E S S E S |
A P R I L
2 0 1 5
1 9
P
owder metallurgy is a process that
produces metal alloys in pow-
der form, consolidates them into
shapes, and then sinters them to achieve
final geometry and properties. Sintering
involves producing a hard solid metal or
ceramic piece from a starting powder.
A variety of metal alloys can be used,
including precious metals. Historically,
iron was extracted by hand from metal
sponge and ground into a powder for fi-
nal melting or sintering.
Using solid state sintering, met-
al powder is placed into a mold or die.
Once compacted into the mold, the
powder is heated to a high tempera-
ture. Under heat, bonding takes place
between the porous aggregate particles
and once cooled, the powder bonds to
form a solid piece.
Powder processes can generate
a wider range of products than what
is possible through direct alloying of
fused materials. Alloying requires com-
plete melting of the base materials and
consideration of solid-liquid phases in
order to achieve the desired combina-
tion of metals. For this reason, powder
metallurgy processes offer advantages
over casting, extrusion, and forging.
Advanced technologies expand on
this basic idea using additive manufac-
turing, in which parts are built to near-
net or net shape. Metal powders may
be sintered in layers, sprayed in specific
patterns, or melted by electron beams
to form parts. Nearly every alloy can be
formed into parts via powder metallur-
gy, while some alloys can
only
be made
by powder metallurgy. Powders can also
be rolled to form sheets, a method com-
monly used to produce sheet metal for
electrical and electronic components.
POWDER METAL TESTING
Maintaining powder metal quali-
ty during fabrication begins with tests
on the powders themselves. They are
checked for correct chemistry, particle
size distribution, and physical and me-
chanical properties. Components man-
ufactured by powder metal processes
are typically tested for hardness, impact
resistance, tensile strength, and density.
Castings and forgings are predom-
inantly used in the automobile industry
and for aircraft manufacture, as well as
power station construction. Casting tech-
nology is used to create complex parts
cost-effectively, with light metal castings
frequently applied to reduce weight, es-
pecially in engine manufacturing.
Where castings and forgings are
concerned, everything depends on
reliable fatigue strength data. This re-
quires that specimens, and even entire
components such as connecting rods,
undergo intensive testing under cyclic
loads. For example, some resonance
testing machines simulate operating
conditions with components charac-
terized under cyclic loads to 1000 kN at
frequencies to 300 Hz. As an example
of this type of equipment, Zwick/Roell,
Germany, offers a range of resonance
testing machines that provide an alter-
native to servohydraulic platforms.
The company’s Vibrophores sup-
port fatigue testing of materials and
components under force control or
strain control modes, while the reso-
nance drive within these systems con-
sumes very little energy and enables
testing at high frequencies, which may
be applied to reduce test time and in-
crease throughput.
TENSILE TESTING
Products made using casting
processes require very little addition-
al processing before completion. For
tensile testing, this means that either
entire specimens must be removed
from specific locations, or that whole
components must be used to deter-
mine tensile strength. Testing complete
component requires high test loads and
Test method
Properties measured
Metallography
Microstructure, particle size and distribution,
composite reinforcements
Scanning electron microscope (SEM)
Combined imaging and elemental analysis
Chemistry
Fillers, binders, contaminants
Rockwell, Brinell, Vickers
Hardness
Charpy
Impact strength
Stress rupture
Time to failure under a specified overload
Inductively coupled plasma/mass
spectrometry (ICP/MS)
Trace elements identification and amounts
X-ray fluorescence
Coating thickness
Image analysis
Particle size and shape
component-specific gripping arrange-
ments and fixturing, while component
geometries often result in specimens
with small final dimensions. For these
small and round specimens, special
specimen grips that are easy to handle
allow the use of automatic extensom-
eters on certain testing equipment. In
addition, complete components are
addressed by a comprehensive group
of accessories for gripping and fixturing.
Zwick Vibrophore systems apply the
resonance principle to enable fatigue
testing of metal specimens. Testing at
high frequencies may be done rapidly,
enabling greater overall test throughput.