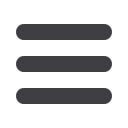
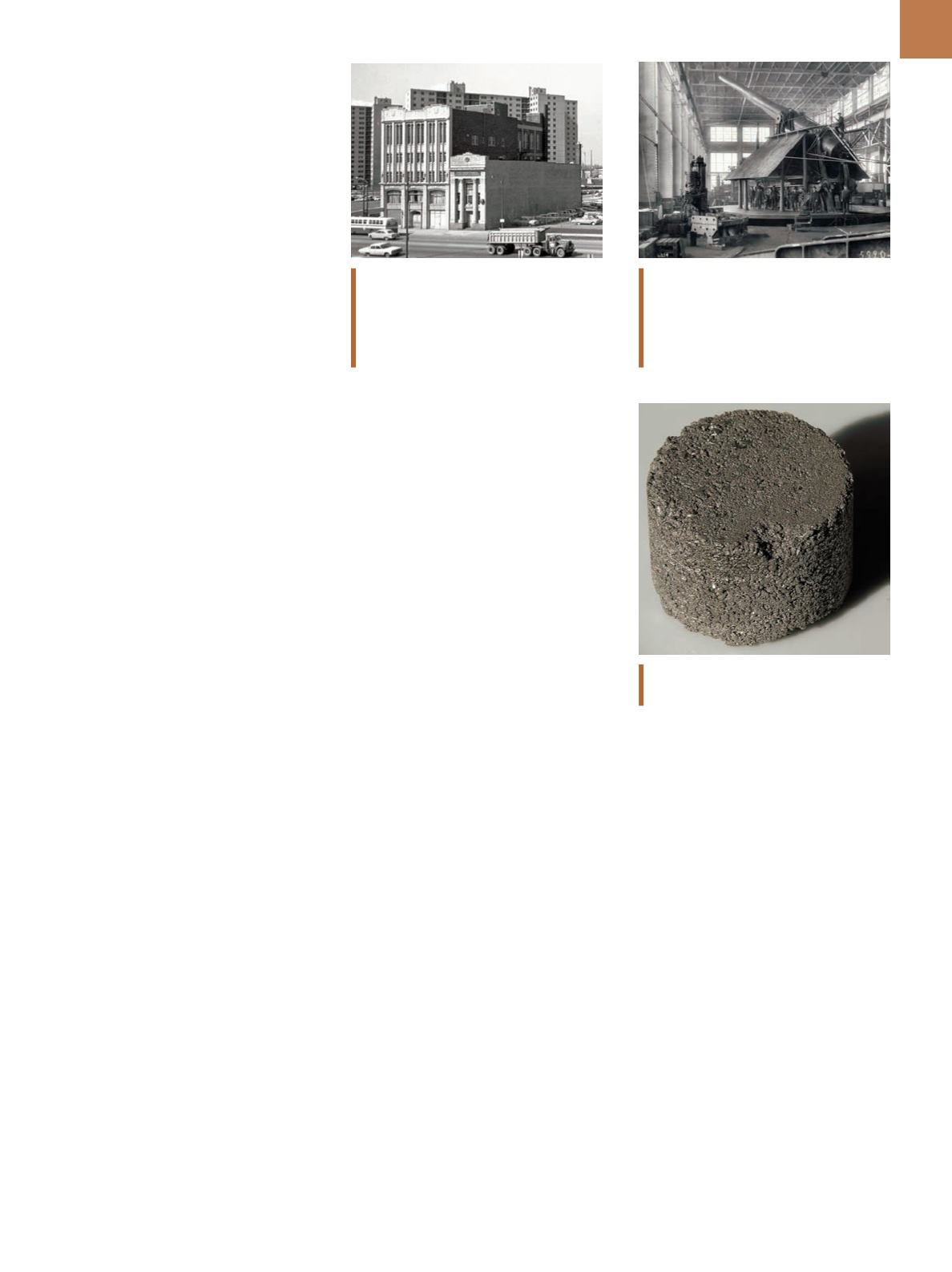
A D V A N C E D
M A T E R I A L S
&
P R O C E S S E S |
A P R I L
2 0 1 5
3 5
TECHNICAL CHALLENGES
A much more serious technical
problem occurred in early 1954 while
attention was focused on future needs
and supply issues. The Pratt & Whit-
ney Engine Division and The Douglas
Aircraft Co. received shipments of met-
al that was brittle. Sheet metal tore
and engine parts cracked under very
low stresses. The problem was quick-
ly traced to high hydrogen contents.
A massive effort was immediately
launched to determine the hydrogen
source, safe level for specification, new
methods for hydrogen analysis, em-
brittlement mechanisms, and how to
salvage all the metal on hand. Vacuum
annealing was quickly identified as a
process for removing hydrogen from
the contaminated metal and the initial
panic gradually subsided. The hydro-
gen problem, however, did not disap-
pear. New tolerance levels were estab-
lished that required additional vacuum
melting and processing for titanium.
The producers were making prog-
ress on improvements in the manu-
facture and quality of their product,
but stronger alloys were still required.
One aircraft company complained that
they would not design titanium into
new planes unless stronger alloys were
available. Much of the titanium used
previously had been lower strength,
commercially pure (CP) titanium. For-
tunately for the industry, an alloy was
under development that would solve
the strength problem.
RESEARCH PROGRESS
AND PROBLEMS
The Armour Research Foundation
(ARF) under the direction of Max Han-
sen, a world expert in phase diagrams,
had been working on a Watertown Ar-
senal contract for alloy development.
Hal Kessler and his group were studying
various alloy systems, including those
containing aluminum and vanadium.
One of their most promising alloys con-
tained 6% aluminum and 4% vanadi-
um, Ti-6Al-4V. Sample ingots were sup-
plied to the arsenal for heat treatment,
mechanical property, and ballistic stud-
ies. The Air Force initiated a contract
at ARF to study the high temperature
properties of interest to jet engine ap-
plications. Later, ARF supplied 100-lb
ingots of Ti-6Al-4V to the engine build-
ers for evaluation. The success of this
effort soon brought the alloy to the
attention of the entire titanium world.
Titanium producers immediately began
producing the alloy, and before long it
was designed into jet engines.
Because the ARF work was done
under a Watertown Arsenal contract,
the patent belonged to the Arsenal.
The Arsenal, however, delayed its pat-
ent application because it decided to
keep the ballistic information secret.
In agreement with Watertown Arsenal,
ARF applied for a broad patent on Ti-
Al-V alloys, including the 6Al-4V com-
position. On the basis of a government-
sponsored project resulting in the ARF
patent application, one defense con-
tractor ceased paying royalties to Rem-
Cru. This precipitated a lawsuit pitting
Rem-Cru against the government and
several users and producers. The suit
was eventually withdrawn, leaving the
invention of Ti-6Al-4V unsettled. To
complicate matters further, a patent
was granted to Watertown Arsenal on
heat treating Ti-6Al-4V alloy. Now the
Arsenal, ARF, and Rem-Cru could all
claim inventing the alloy. The final word
seems to be contained in a letter from
Charles F. Hickey, Chief, Technology
Management Branch of Watertown Ar-
senal to Harold Kessler stating that he
(Kessler) was indeed the inventor of the
most important titanium alloy.
Problems with titanium process-
ing, including hydrogen embrittlement,
limited its production in 1954 to 1300
tons, hardly more than in 1953. Sponge
production, however, more than dou-
bled to 5400 tons. Metal shipped in 1955
increased to 1900 tons and sponge to
7400 tons. The main use was in jet en-
gines and the biggest customer was
Pratt & Whitney. Sponge production
moved ahead much faster than met-
al production. In addition, in a case of
one hand not knowing what the other
was doing, the government contracted
with the Japanese to exchange surplus
grains and other foods for titanium
sponge. This Japanese sponge, which
started as a trickle in 1953, reached
600 tons in 1955 and 3600 tons in 1957.
The competition forced the price of
sponge from $5 a pound to $2.25.
For more information:
Charles R.
Simcoe can be reached at
crsimcoe1@ gmail.com.The Binga Bank and Arcade Building
next to it, Chicago, were purchased by
the Armour Research Foundation and IIT
in 1952. Courtesy of IIT Archives Acc. No.
1998.199/Box YY-1/Buildings.
Harold Kessler, supervisor of alloy devel-
opment at Armour Research Foundation,
and his teamdeveloped the Ti-6Al-4V
alloy under a contract with Watertown
Arsenal, pictured here.
Titanium cylinder, 3 x 4 cm, 120 grams.
Courtesy of Jurii, Wikimedia Commons.