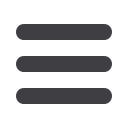
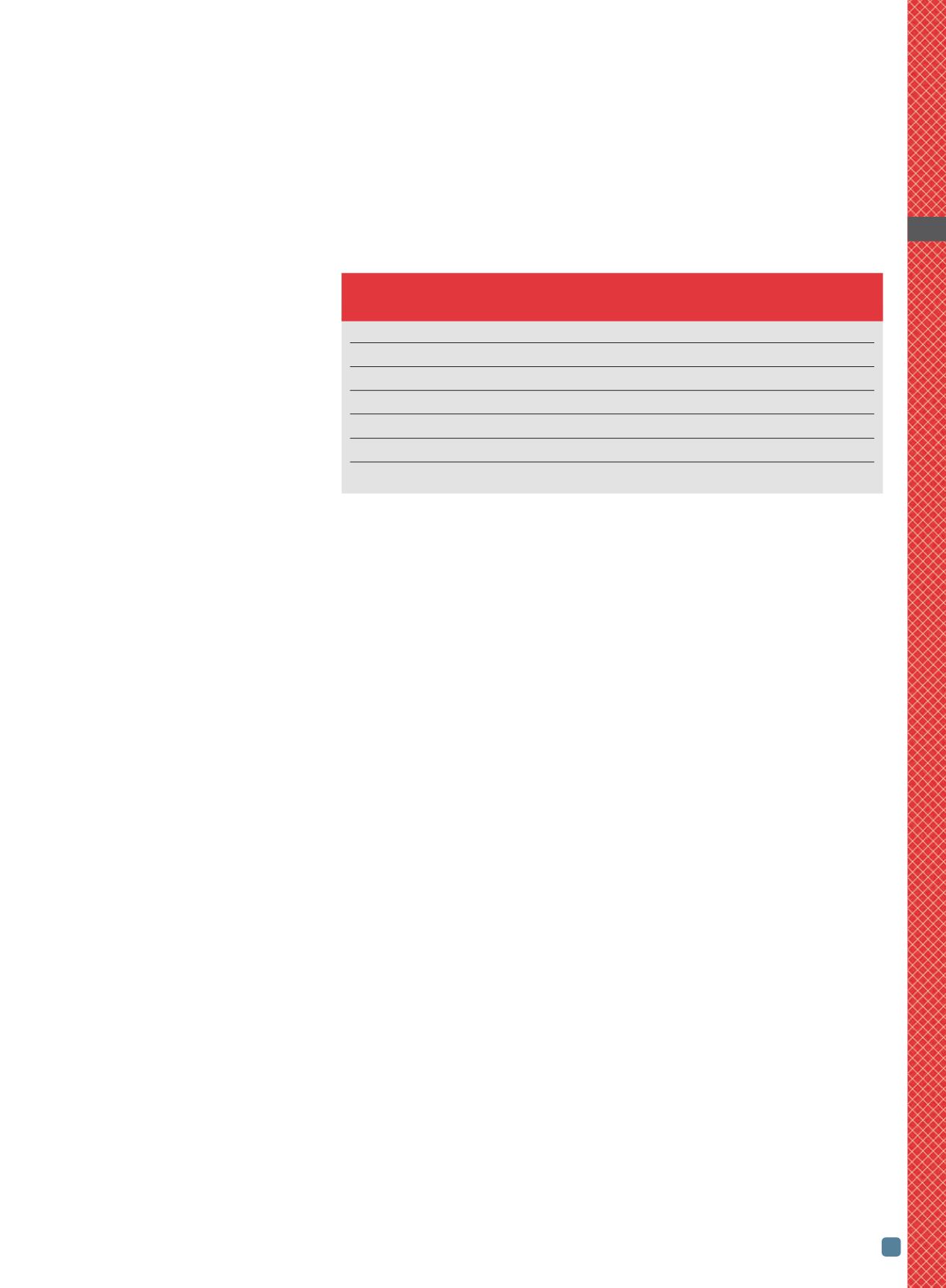
Boriding (also known as boronizing) is a
diffusion-based case-hardening process
for metals that creates an ultrahigh hard-
ness case (1500–2200 HV) below the
surface of the parts being treated. It pro-
duces exceptional wear resistance for
metal parts that operate in severely abra-
sive and erosive operating conditions
and also improves anti-galling proper-
ties. Boriding typically more than triples
the service life of high wear parts
compared with other traditional heat
treatments such as carburizing, carboni-
triding, nitriding, nitrocarburizing, thin
PVD coatings, and platings like hard
chrome. Boriding creates a wear layer
with higher hardness than many wear
resistant thermal spray coatings, such as
tungsten carbide and chrome carbide. It
is not mechanically bonded to the sur-
face, but instead is diffused below the
surface of the metal, making it less prone
to peeling and breaking off treated parts.
Boriding is performed by diffusing
boron atoms into a metal surface and al-
lowing the boron to react with elements
present in the substrate to form metal-
boride compounds. Upon diffusing
enough boron into the surface, a metal-
boride compound layer with high hard-
ness precipitates and grows below the
surface of the part. Different types of
metal-boride layers are possible, the
composition of which depends on the
material being treated. For example,
iron-boride layers form in steels and cast
irons and nickel-boride layers form in
nickel-base alloys. Other compounds
possible include cobalt and titanium
borides. This article discusses only
boriding of ferrous alloys.
Two iron-boride compounds formed
when boriding steel are Fe
2
B (at lower
boron concentrations) and FeB (at higher
boron concentrations), each having dif-
ferent structures, densities, and mechan-
ical properties as shown in Table 1
[1]
.
Single-phase Fe
2
B layers
. As boron dif-
fuses into a steel surface, concentration
at the surface starts out at zero and be-
gins to increase until the concentration
just below the surface reaches a level
where Fe
2
B compounds begin to pre-
cipitate and grow. Fe
2
B is the first
phase to form, as it contains a lower
boron concentration (33%) than FeB,
which requires 50% boron concentra-
tion. A solid continuous single-phase
Fe
2
B layer forms below the surface and
grows deeper over time as boron con-
centration increases. An Fe
2
B single-
phase layer is the ideal result and is the
desired microstructure after boriding
ferrous materials.
Dual-phase Fe
2
B-FeB layers
. Boriding the
part for longer times to create a deeper
case makes it more likely the boron con-
centration just below the surface will ex-
ceed 33%, which leads to the formation of
the more boron-rich FeB compound in
addition to the already formed Fe
2
B.
Powder pack cementation is the most
commonly used method for boriding. A
drawback of the process is that the
boron activity of the powder pack is
fixed; it cannot be varied during the
process. This makes it impossible to per-
form a diffusion process similar to the
boost-diffuse methods used in carburiz-
ing and two-stage Floe nitriding. In
these processes, carbon and nitrogen
potentials of the furnace atmosphere can
be reduced to lower values during later
stages of the process to avoid oversatu-
rating the surface with excessive carbon
or nitrogen, which are responsible for
carbide networking, excessive retained
austenite, and/or nitride networking.
Therefore, boriding to deeper case
depths with a fixed high boron activity
during the entire process eventually
oversaturates the surface with boron,
forming a second FeB layer on the out-
side of the original Fe
2
B layer.
Most commercially available boriding
powders create high boron activity lev-
els, and are good for quickly forming
high-quality thin boride layers with
short cycle times. However, there is a
limit to the depth of the single-phase
layer that can be formed with longer
cycle times before undesirable FeB be-
gins to precipitate resulting in a dual-
phase FeB-Fe
2
B layer. The limit on depth
depends on the material as each one has
a different boron diffusivity rate.
Plain carbon and lower alloy steels gen-
erally have higher boron diffusivity rates
and enable rapid diffusion to deeper
depths without a buildup of high boron
concentration at the surface. More
highly alloyed steels have lower boron
diffusivity rates, which tends to trap
boron near the surface. This increases
surface boron concentration, forming
ADVANCED MATERIALS & PROCESSES •
NOVEMBER-DECEMBER 2014
41
DEEP CASE BORIDING
FOR EXTREME WEAR RESISTANCE
HTPRO
7
THE ABILITY TO PRODUCE DEEPER CASE BORIDE LAYERS THAT ARE NOT PRONE TO SPALLING
MAKES THE BORIDING PROCESS COMPETITIVE WITH SOME CONVENTIONAL DEEP-CASE
AND THICK-COATING PROCESSES.
Craig Zimmerman* and Nick Bugliarello-Wondrich,*
Bluewater Thermal Solutions
*Member of ASM Heat Treating Society
TABLE 1 — PROPERTIES AND CHARACTERISTICS
OF IRON-BORIDE COMPOUNDS
FeB
Fe
2
B
Boron content, wt%
16.23
8.83
Structure
Rhombic
Tetragonal
Residual stress on cooling
Tensile
Compressive
Coefficient of linear thermal expansion,
´
10
-6
/K
23
7.9–9.2
Hardness (HV0.1)
1900–2100 1800–2000
Density, g/cm
3
(lb/in.
3
)
6.75 (0.244)
7.43 (0.268)