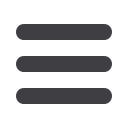
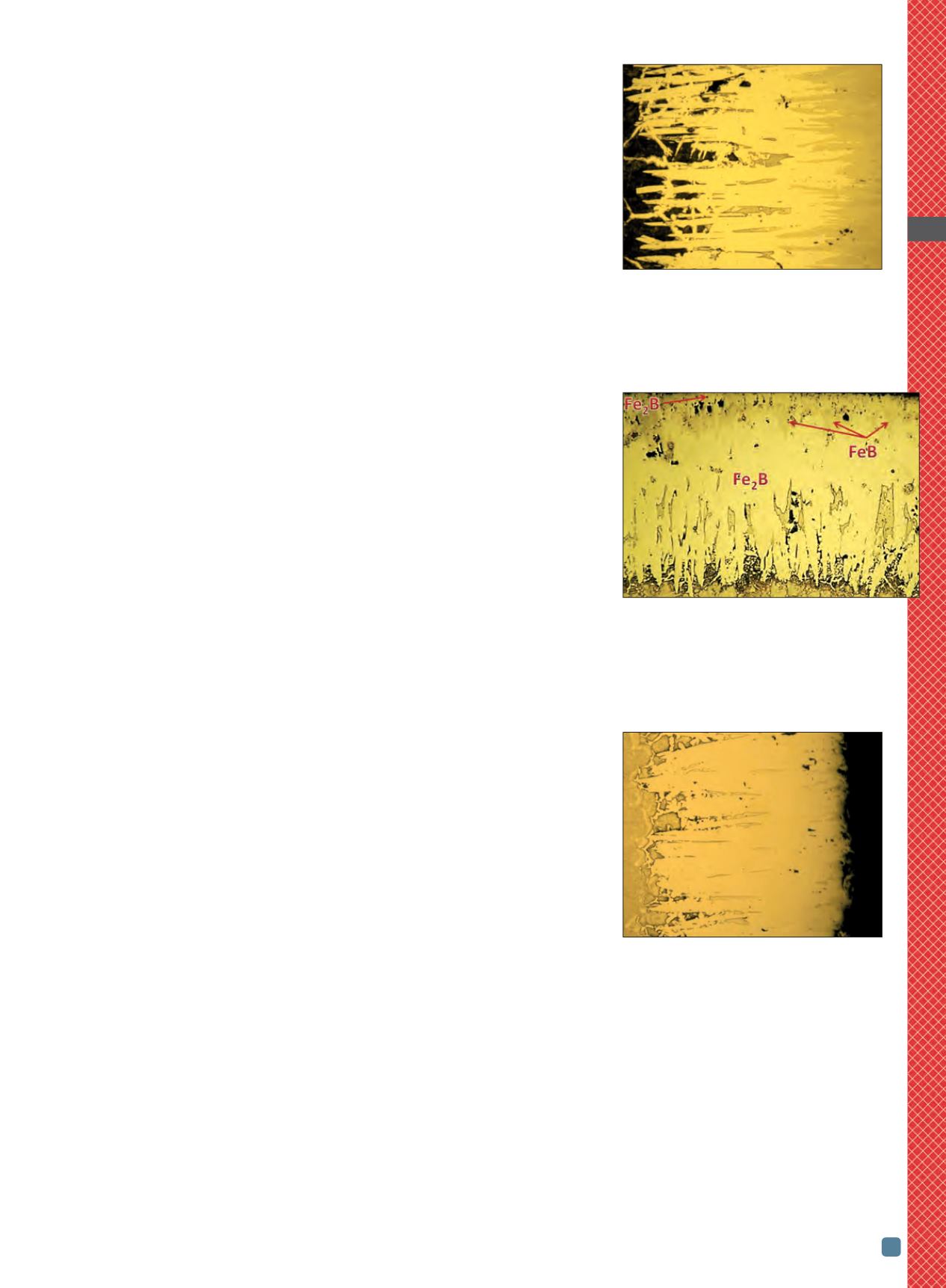
ADVANCED MATERIALS & PROCESSES •
NOVEMBER-DECEMBER 2014
43
HTPRO
9
formed at the surface. However, the dif-
fusion treatment on the piece was in-
sufficient to reduce all of the FeB
present. The near surface has fully re-
verted from FeB (darker teeth) into
Fe
2
B (lighter teeth), but there is still
some FeB present at depths between
0.001 and 0.002 in. that was not con-
verted into Fe
2
B. It is crucial in this
process to ensure that spalling does not
occur between the boost and diffuse
steps and that the diffuse process is suf-
ficient to ensure that all FeB is reduced
into Fe
2
B by the end of the process.
(2). The entire boriding process can be
carried out at lower boron potentials so
FeB never forms. This requires the devel-
opment of a customized boriding powder
different from most of the standard com-
mercially available boriding powders.
With many different boron sources, acti-
vators, and diluents available to choose
from, a wide array of different results are
possible through the development of cus-
tomized boriding powders. However, each
grade of material will boride differently as
they all have different boron diffusivity
rates necessitating a different customized
powder for each material. Another draw-
back of boriding at lower boron potentials
is that the boron enters the parts very
slowly, requiring longer cycle times. Sub-
stantial knowledge, testing, experimenta-
tion, and research are required to develop
customized deep-case boriding powders
for different materials and desired boride
layer depths.
(3). A method where a boost-diffuse type
process comparable to gas carburizing
and gas nitriding, such as electrolytic
salt-bath boriding, could be used. The
method involves immersing parts into a
borax salt bath held at austenitizing tem-
peratures. Parts are connected to a dc
power supply (cathodes) and graphite
plates are connected to the powder sup-
ply and immersed into the salt bath (an-
odes). Boriding occurs as electric current
flows through the system with borax re-
acting with both parts and anodes to free
up boron atoms that diffuse into the part
surfaces. The boost-diffuse process is
possible because boriding only occurs as
electric current is applied. When current
is off, boron continues to diffuse into the
parts at austenitizing temperature. Thus,
a deeper boride layer forms while reduc-
ing the boron concentration at the sur-
face of the parts. The process, called
phase homogenization in electrochemi-
cal boriding (PHEB), was developed by
G. Kartal, S. Timur, V. Sista, O.L. Eryil-
maz, and A. Erdemir
[2]
.
The process has not yet gained wide-
spread industrial acceptance due to var-
ious problems such as salt residues being
difficult to remove from parts, difficul-
ties in building and maintaining a borax
salt-bath furnace, and questions about
reliability and safety of high electrical
current flowing through a high-tempera-
ture borax salt bath. Another concern is
the ability to maintain uniform electrical
connectivity of the parts to the fixtures
as the fixture material degrades.
(4). Another boost-diffuse boriding
process could use boriding gases in an at-
mosphere furnace for a portion of a cycle
and then replace the boriding gases with
an inert gas, or adjust the gases to reduce
the boriding potential during later stages
of the process. Bluewater Thermal Solu-
tions is developing this type of process,
but details are proprietary and are not
discussed at length here.
Results of deep-case boriding
Bluewater Thermal Solutions has devel-
oped several deep-case boriding processes,
which are currently being performed com-
mercially. Parts treated using these
processes outperform conventionally
borided parts with shallower boride layers
in several applications including oilfield
drilling equipment, industrial pumps, high
wear agricultural machinery parts, and
ground-engaging tools, all subject to harsh
abrasive and erosive wear conditions.
Materials including 1018 plain carbon
steel, 4140 alloy steel, and O1, A2, D2,
and S7 tool steels have been deep case
borided with a single-phase Fe
2
B layer
with no spalling problems. Steels like
1018 and 4140, traditionally borided to a
depth of 0.003 to 0.005 in., are now able
to be deep case borided to a depth of
0.010 to 0.020 in. Tool steels like O1, A2,
and S7, traditionally borided to a depth
of 0.001 to 0.003 in., can be deep case
borided to a depth of 0.008 to 0.012 in.
Martensitic and PH grade stainless steels,
traditionally borided to a depth of 0.001
in., can be borided to a depth of 0.004 in.
with no spalling problems. Figure 6
shows a photomicrograph of 4140 alloy
steel deep case borided to a depth of
0.015 in. where the structure is predom-
Fig. 4 —
AISI 4140 alloy steel deep case
borided to a depth of 0.020 in. using
commercially available boriding powder. The
boride layer consists of about 50% FeB
(dark colored teeth near surface) and 50%
Fe
2
B (lighter teeth) below the FeB layer, an
undesirable condition prone to spalling.
Fig. 5 —
AISI 4140 alloy steel deep case
borided to a depth of 0.011 in. followed by a
vacuum diffusion treatment. Some FeB near
the surface converted back to single-phase
Fe
2
B (light colored teeth) while some FeB
(darker teeth) is still present at slightly
deeper depths. Single-phase Fe
2
B is
present below.
Fig. 6 —
AISI 4140 alloy steel deep case
borided to a depth of 0.015 in. consisting of
nearly 100% single-phase Fe
2
B with only
minor traces of FeB (darker colored teeth)
near the surface.