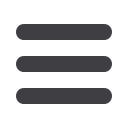
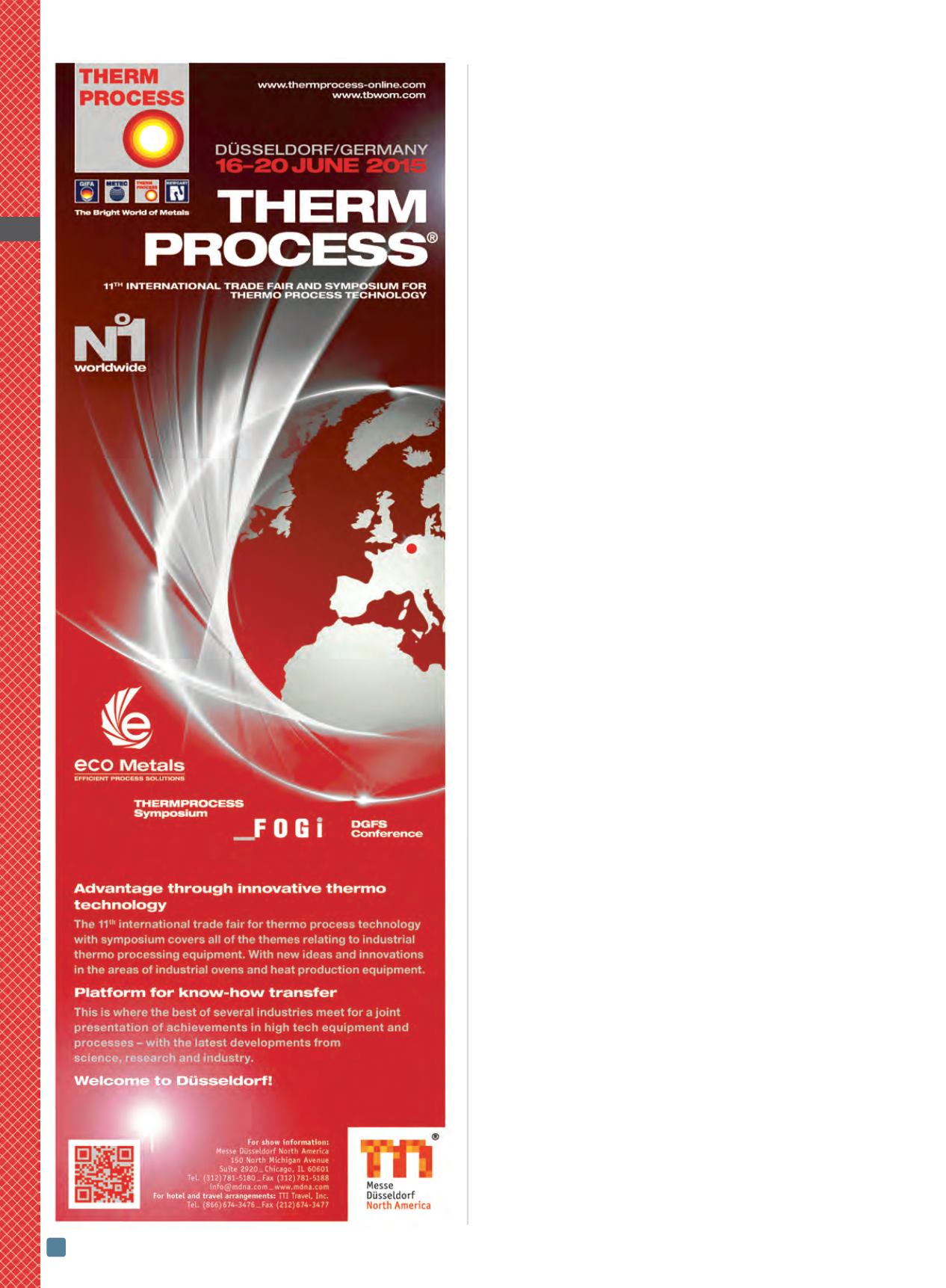
ADVANCED MATERIALS & PROCESSES •
NOVEMBER-DECEMBER 2014
46
HTPRO
12
standards and guidelines for properly measuring hardness of
the case and heat affected zone, as well as a review of issues
and complications related to different hardness measuring
techniques are also included. Case studies of pattern specifi-
cations are presented, and special attention is given to proper
monitoring of induction processes, destructive and nonde-
structive testing, and quality assurance.
The new handbook also includes in-depth analysis of ways to
develop robust, efficient, and high-quality processes; the for-
mation of initial, transient, and residual stresses and their ef-
fect on the performance of heat treated components, shape
distortion, and cracking potential. Studies have been con-
ducted to evaluate stress formation during heating and spray
quenching in workpieces with classical shapes and parts with
geometrical irregularities such as fillets, diameter changes,
and holes. For example, Figs. 3 and 4 show finite-element
mesh with nodal locations in the proximity of an oil-hole and
the variation of maximum principal stress during spray
quenching, respectively
[2]
. A quench delay has a significant ef-
fect on the appearance of transient and residual stresses.
Selection of critical process parameters and review of induc-
tor designs, heat pattern control, intricacies in using magnetic
flux concentrators, and spray quench design considerations
are included as well.
Another topic area covers subtleties in determining tempera-
ture requirements when induction heating plain carbon and
alloy steels, superalloys, titanium, aluminum and copper al-
loys, and other materials prior to hot and warm working.
Novel technological developments in heating billets, bars,
tubes, rods, and other metallic workpieces, as well as a con-
cept for controlling a billet’s true temperature are discussed.
Development of optimization procedures, principles of mul-
tiobjective optimization, and strategies for obtaining optimal
process control algorithms based on various technological
criteria, real-life constraints, and cost functions (e.g., maxi-
mizing throughput, temperature uniformity, energy effective-
ness, minimizing required shop floor space, metal loss, etc. is
also explored.).
Failure analysis and prevention, which are associated with
product quality, process cost-effectiveness, downtime losses,
and other issues are discussed as well. Many publications cov-
ering failure analysis are devoted primarily to heat treating
processes other than induction, therefore several articles in
this handbook discuss various aspects of failure analysis of
components heat treated using electromagnetic induction.
Typical defects, abnormal characteristics, and root causes of
different failures are discussed, as well as the effects of metal-
lurgical factors and abnormalities such as excessive grain
coarsening, presence of decarburized layers, inclusions,
seams, laps, mixed structures, and overheated and burned
steels. Causes of surface, transverse, and longitudinal internal
cracks and their prevention are reviewed.
The new volume also includes good practices in designing
and fabricating long-lasting inductors and ways to avoid their
premature failures. A fishbone diagram of premature failure