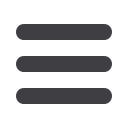
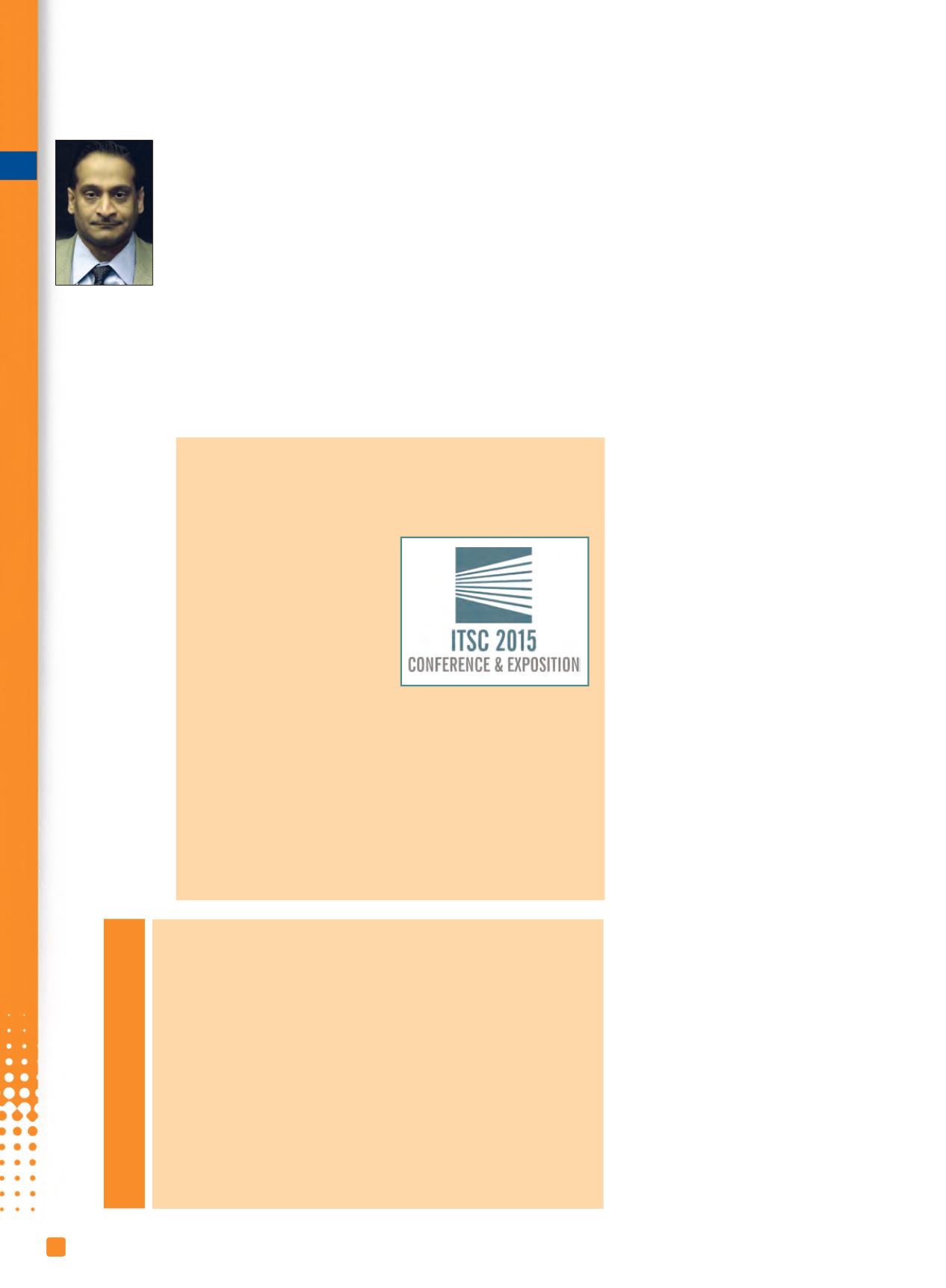
A
dvancements in technology ultimately benefit the whole of society. Cost reductions from longer equip-
ment life and efficiency improvements, cleaner environments, shorter recovery times for hospital patients,
and improved communication methods are among the many benefits routinely experienced today. Thermal
spray has become integrated in many products as an enabling technology and in manufacturing processes as
critical tooling, making it one of the most important surface modification methods available.
Countless research papers are published annually detailing new developments in thermal spray coatings for
the gas turbine market. Driving forces include efficiency and longevity enhancements. Even a 1% efficiency gain
can translate to millions of dollars in savings for utility providers. Typically, increases in gas inlet temperatures
enable efficiency improvements. As such, constant research and development in new low-conductivity thermal
barriers has resulted in recent implementation by some OEMs. Higher firing temperatures also require improve-
ments for other coatings used in the turbine such as abradables, bond coats, and wear coatings. Ceramic
components in next-generation turbines, especially SiC-SiC composite materials, will also require more reliant
environmental barrier coatings (EBCs) as protection in high moisture and molten salt environments.
Thermal spray coatings for medical applications offer further opportunities for improvement. Plasma sprayed
titanium and hydroxyapatite for implants as well as alumina for laparoscopic procedures are well established.
Generally, plasma sprayed titanium and hydroxyapatite are not hydrophilic, but next-generation coatings will
have this requirement to shorten recovery
times. This will likely require post pro-
cessing of sprayed coatings.
Coatings applied to tooling and fix-
tures used for semiconductor processing
always demand high-quality formulas to
decrease particulates and improve yield.
Higher density, highly adherent, cost ef-
fective yttria and alumina coatings will
need to be applied to better control par-
ticulate matter as the node size de-
creases. This may require better
application equipment such as cascading
guns, or at least pulse width modulated
power supplies, to improve upon conven-
tional spray systems.
In this final 2014 issue, yet another
emerging thermal spray technique is pre-
sented—an innovative direct write
method using plasma spray. A special
aperture system enables fabrication of
thermocouples, antennas, and other sen-
sors directly onto components thereby
creating “smart structures,” illustrating
the emerging markets and technologies
available for thermal spray. Also included
in this issue is the second part of a safety
article that reviews best practices in the
thermal spray industry.
Be sure to share all of your innova-
tions at next year’s International Thermal
Spray Conference and Exhibition. This
mega event is being co-Located with
AeroMat and Microstructural Characteri-
zation of Aerospace Materials and Coat-
ings from May 11-14 in Long Beach,
California. We hope to see you there!
Rajan Bamola
iTSSe co-editor
Surface Modification Systems Inc.
i
T
S
S
e
EDI TORIAL
2
ADVANCED MATERIALS & PROCESSES •
NOVEMBER-DECEMBER 2014
52
Thermal spray advances
into emerging markets
International Thermal Spray
Conference and Exposition
(ITSC) 2015
ITSC, taking place May 11-
14, 2015, in Long Beach, Calif.,
is the world’s foremost interna-
tional conference and exposition
for thermal spray technologists,
researchers, manufacturers, and
suppliers. The conference is co-
located with both AeroMat and
Microstructural Characteriza-
tion of Aerospace Materials and Coatings. Whether attendees are
thermal spray experts, experienced engineers or scientists, or new
to the field, the 2015 ITSC technical program features something
for everyone—from the latest in advanced technology, research,
and development to a wealth of resources about processes that can
be applied immediately to impact critical issues such as corrosion,
wear, and abrasion. The conference also features a special presen-
tation by John Grotzinger, chief scientist and head of strategic
planning for NASA’s Mars Exploration Rover mission. Visit
asminternational.org/web/itsc-2015/homefor more information.
EDUCATION
Introduction to Thermal Spray
Education Course
February 9-10, 2015
ASM Headquarters, Materials Park, Ohio
Instructor: Mr. Richard A. Sayman
Thermal spray has evolved from a technology designed to be a cost ef-
fective method of repairing worn components and machined parts to
a process used to provide improved part performance and add longer
life to components. As the thermal spray profession has changed, so
has the need to ensure safe and consistent methods for thermal spray
operators. ASM International brought together the leaders in the Ther-
mal Spray Society to compile their knowledge and experience in a
comprehensive, easy to understand course.
Visit
asminternational.org/educationfor more details.