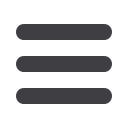
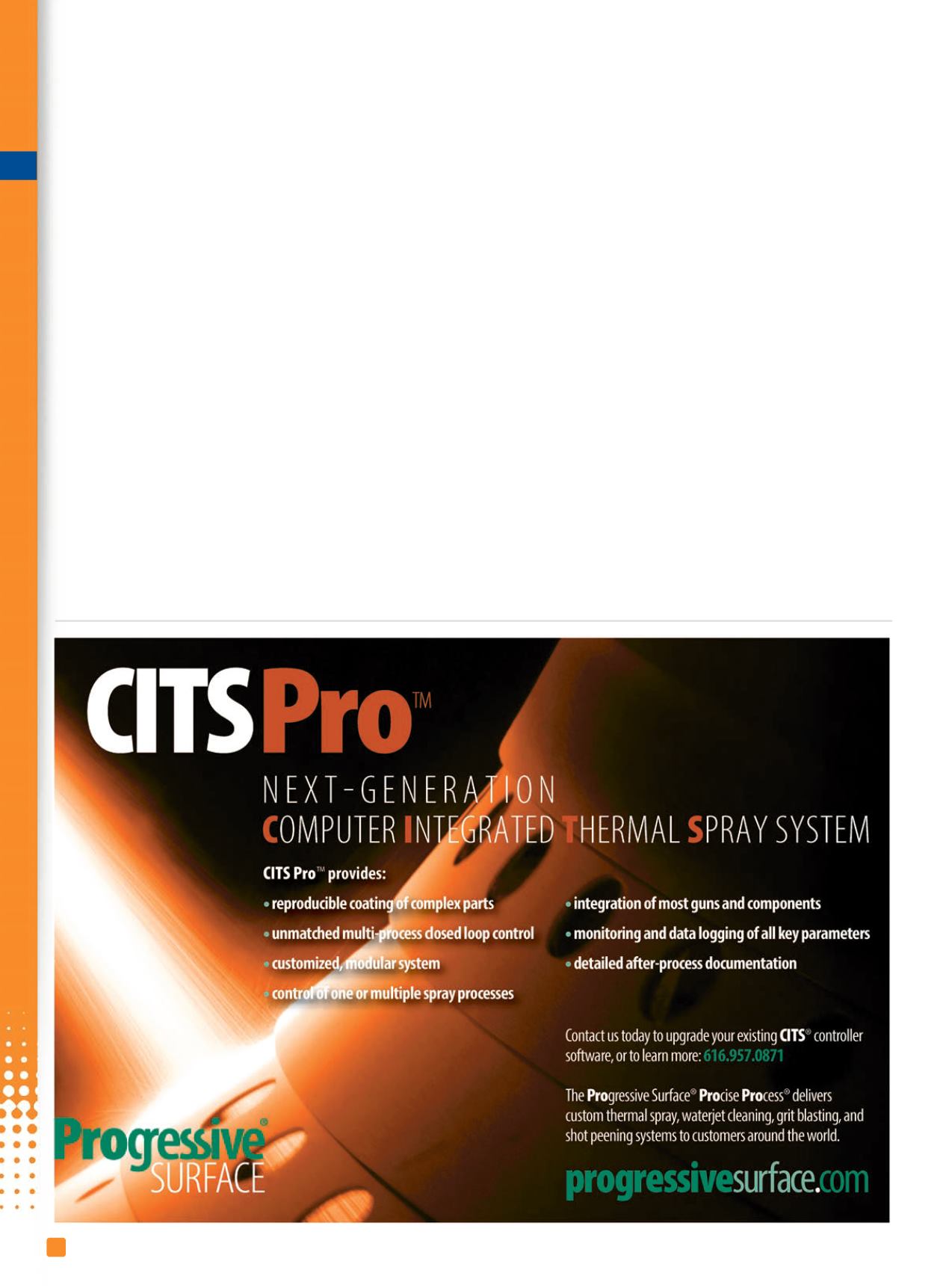
ADVANCED MATERIALS & PROCESSES •
NOVEMBER-DECEMBER 2014
56
i
T
S
S
e
6
Sensors provide a direct measure of heat flow to com-
ponents exposed to high temperatures or other harsh envi-
ronments. Heat flux sensors can be printed directly onto
parts or integrated as sensor plugs or inserts. Sensors offer
fast response times vital for optimal control system im-
plementation and do not require water cooling. Direct
write technology is also well suited for construction of
multilayer sensor architectures such as the thermopiles
shown in Fig. 3.
Printed sensors, heaters, and fine feature patterns offer a
low profile design without the need for water cooling, high
temperature resistance, and have no adhesive/carrier limita-
tions. They also feature high sensitivity and fast response
time, are available in custom sizes, and can be printed onto
parts or as standalone sensors.
Printed heaters
High quality heaters can be printed onto polymer lami-
nates and onto conformal metallic structures. Uniform thick-
ness control and precision patterning enable high heat flux
heaters (500 W/cm
2
) to be successfully deployed in applica-
tions ranging from aerospace and automotive to the electron-
ics industry. In addition, heater patterns can be combined
with thermocouples for closed loop control and embedded
within a ceramic coating.
Heaters feature high efficiency, low contact resistance,
and the ability to quickly heat parts. They also offer high tem-
perature resistance, no adhesive/carrier limitation, high heat
flux, high reliability (by eliminating adhesive-related fail-
ures), and a reduced need for redundancy. Heaters can be
printed directly onto complex conformal surfaces as well.
Examples of heaters printed using direct write technology
are shown in Fig. 4.
Printed conductors and antenna patterns
Direct write copper conductor networks can replace
conventional wiring techniques with integrated wiring
schemes for a variety of power management and signal dis-
tribution applications. Incorporating wiring networks onto
components and structures, in either surface mount or em-
bedded configurations, enhances reliability and eliminates
cumbersome wiring bundles. Conductor trace networks are
customizable and exhibit exceptional electrical properties
and durability.
Direct write can also be used to fabricate antenna pat-
terns onto air vehicle structures. Copper patterns are
printed directly onto composite structures with features
conforming to complex surface contours. Integrated com-
munications eliminates the need for protruding structures
such as radomes, which are often detrimental to operation,
particularly for aerodynamic surfaces. Design iterations
aimed at tuning performance characteristics can be rap-
idly incorporated into the process, in turn expediting new
product development.
Direct write technology combines antenna design and
performance modeling with conformal fabrication to enable
multiple antennas that span different frequency bands
(VHF/UHF/GPS) to be incorporated onto a single structure