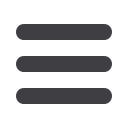
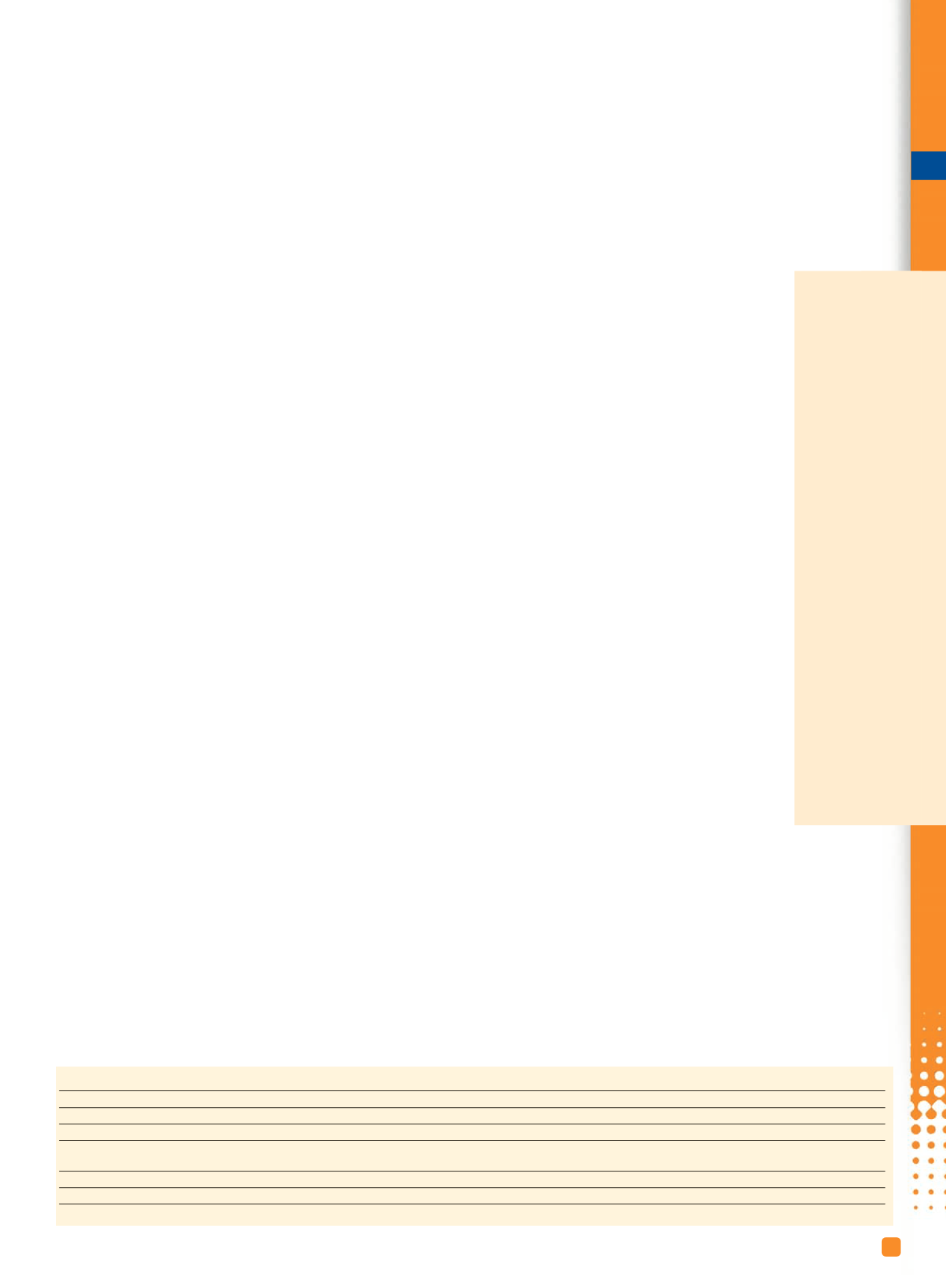
i
T
S
S
e
9
ADVANCED MATERIALS & PROCESSES •
NOVEMBER-DECEMBER 2014
59
W
orkplace safety is not a subject that typically captivates an
audience, but in thermal spray environments, hazards of all
types are faced on a daily basis. Unlike truly dangerous workplaces,
such as shipyards or construction sites, where situational awareness
is necessary to stay alive and well, the extra cost and time of safety
programs can make them unattractive in comparatively comfort-
able thermal spray shops. However, compelling reasons to embrace
the safety topic still exist. The first part of this article series [August
2014
iTSSe,
p 7] addresses dust and fume hazards.We will now ex-
plore noise, mechanical hazards, and other safety issues common in
thermal spray environments.
Noise
Noise is a common workplace hazard in thermal spray opera-
tions. Excessive noise exposure not only damages hearing, but also
can cause tinnitus (ringing in the ears), stress, hypertension, and
sleep disturbance. Because excessive noise is common in thermal
spray applications, a variety of methods are available to ensure the
safety and health of technicians. Table 1 outlines the actions required
per noise level at key time-weighted-average exposures.
Because most thermal spray guns continually emit noise in
excess of 95 dBA several layers of protection are required. The
most effective is a hearing conservation program in which em-
ployees’ hearing is tested annually by a professional in a con-
trolled environment. Regular testing enables detection of hearing
changes before permanent damage occurs. Environmental con-
trols, such as sound deadening enclosures and isolated control
rooms, can also shield technicians from noise and substantially
lower exposure. Wearing earplugs and earmuffs in close proxim-
ity to processes is also required.
Mechanical hazards
Though less obvious than noise and dust, mechanical hazards
are also common in thermal spray environments. Modern industrial
robots are some of the best engineering tools available for limiting
operator exposure to both dust and noise. However, robots move
at much faster speeds than humans, and with greater force and
agility. Even when running familiar programs, robotic motion can
sometimes be unpredictable. Therefore, it is essential to stay well
outside a robot’s range of motion. To ensure this, most robotic sys-
tems incorporate either mechanical or electronic means for restrict-
ing the arm’s movement about its base axis—creating a safe zone
where the robot cannot reach. Whether restricted or not, a robot’s
range of motion should be marked on the floor around it. Door in-
terlocks and external enabling devices also ensure that safety en-
closures are fully closed and operators are outside before the
automatic robot program is initiated.
Miscellaneous hazards
Other hazards, such as electrical (both high voltage and
high current), compressed gas, and material handling systems
are also present in thermal spray environments. Plasma and
twin wire arc spray systems both use high current, low volt-
age power supplies—similar to many commercial welding
power supplies—that are designed for safe industrial use.
However, due to the nature of spray operations, nearly every
electrical gun presents a shock hazard—
particularly because conductive metal dust
and water from cooling lines are often pres-
ent, as is abrasive grit, which can deterio-
rate electrical insulation.
Compressed gases, such as bottled oxy-
gen, fuel, or shielding gas, bulk liquid or
gaseous storage, or even compressed shop
air, are also often found in production facil-
ities and pose a constant threat of leaks.
Safe handling practices, such as ensuring all
gas bottles are secured from tipping and
venting all equipment at the end of a shift,
can minimize this threat.
Conclusions
This article covers basic hazards found in
thermal spray environments. Regarding com-
pliance, in addition to following workplace
safety regulations, OSHA typically only re-
quires completion of three basic forms:
• Form 300—Log of Work-Related
Injuries and Illnesses
records basic
information about each occurrence of a
recordable injury or illness.
• Form 301—Injury and Illness Incident
Report
is completed for each recordable
incident of a work-related injury or
illness, and includes details about the
individual case, including any treatment
given and the likely cause.
• Form 300A
summarizes all incidences recorded for the
calendar year on Form 300, and for most businesses is
the only form that must be annually submitted to OSHA.
Evidence of an organized safety program, including regu-
lar training documentation, will likely go a long way toward
demonstrating maintenance of a safe workplace in the event
of an audit. These topics and many others (sidebar) afford
ample training opportunities. Given the range of topics, safety
can easily become a regular part of workplace
conversations.Training materials and much more are available
online at osha.gov.
iTSSe
Safety in Thermal Spray Settings: Part 2
Much of the following material was developed by members of
ASM International’s Thermal Spray Society Safety Committee.
TABLE 1 — NOISE EXPOSURE GUIDELINES
Noise exposure*
Required actions
<85 dBA (action level)
Recommend hearing protection use.
>85 dBA to <90 dBA (permissible exposure limit) Hearing conservation program (HCP), exposure monitoring, provide hearing protection devices.
>90 dBA
Provide hearing protection and HCP; feasible engineering and administrative controls must
be implemented above 90 dBA.
<105 dBA (integrated)
Same as above; supply and ensure use of earplugs and earmuffs.
<115 dBA
Workers are not permitted to be exposed to sound levels above 115 dBA.
*Eight-hour time-weighted-average exposure
COMMON SAFETY
TOPICS IN
THERMAL SPRAY
ENVIRONMENTS
Safety orientation
Bloodborne pathogens
Confined spaces
Control of hazardous
energy (lockout/tagout)
Electrical safety
Emergency response
plans
Fire extinguisher use
Hazard communication
Hazardous materials
storage and handling
Hazardous waste
Hearing conservation
Hoists and cranes
Housekeeping
Machine guarding
Medical surveillance
Personal protective
equipment
Powered industrial
trucks (forklifts)
Respiratory protection
Spill prevention
Storm water control