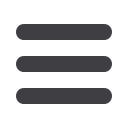
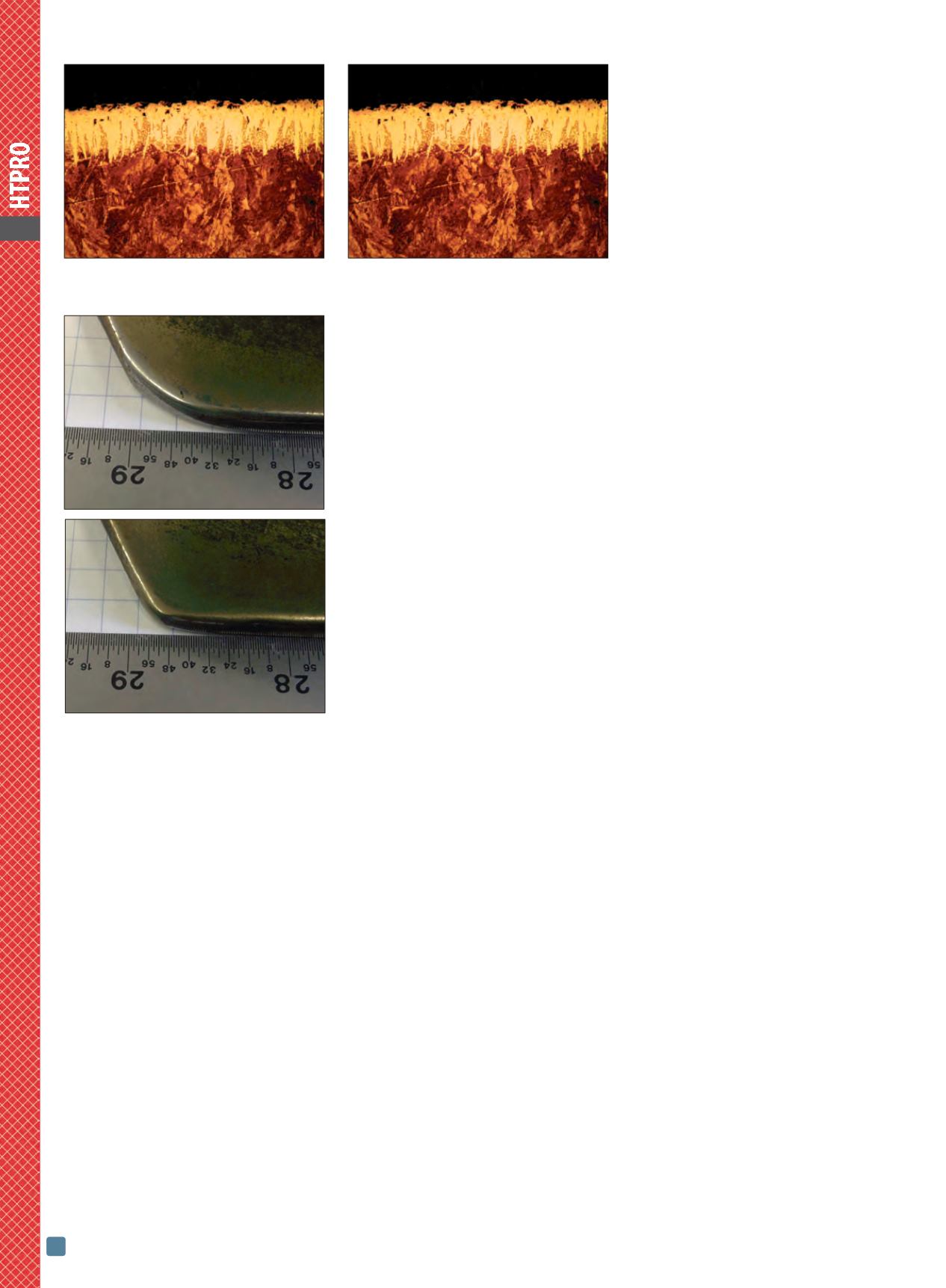
ADVANCED MATERIALS & PROCESSES •
NOVEMBER-DECEMBER 2014
44
HTPRO
10
inately Fe
2
B with only minor traces of
FeB present at the surface.
To design a process capable of creating a
specific boride layer depth comprising sin-
gle-phase Fe
2
B, each steel grade requires
different processing parameters in terms
of cycle time, temperature, and boron po-
tential for each stage of the process. For
instance, processing parameters used for
deep case boriding 1018 plain carbon steel
are quite different than the parameters for
A2 tool steel to produce a 0.015 in. deep
single-phase Fe
2
B layer.
Applications and performance
Deep case boriding of parts provides
greater depth of the ultrahigh hardness
boride layer, which extends the wear life
of parts. For example, a ground-engaging
tool manufactured with a carbide wear
insert is now being borided with im-
proved wear life. Two sets of the tool
were provided to a manufacturer for field
testing to compare service life-to-failure
of tools treated with a conventional 0.004
in. boride layer depth and a deep case
borided 0.010 in. layer depth. Figure 7
shows the microstructures of each tool
set. After multiple field trials, the manu-
facturer of these tools elected to have the
deep boriding process specified for its
tools, even at a higher cost than the con-
ventional boriding process or tools made
with a carbide insert. According to the
manufacturer, the 0.010 in. boride depth
versus the 0.004 in. boride depth is 75 to
100% more durable under varying soil
conditions. The relative wear properties
of the parts with deeper boride treatment
are superior in a cost-benefit analysis.
An oilfield drilling-tool company is spec-
ifying the deep boriding process for its
tools, which are exposed to high pressure
flow of abrasive particles. Deep boriding
improved tool performance to the point of
lasting for the entire well-drilling process
compared with previous parts that wore
out and failed during drilling, requiring
costly downtime to replace the tools.
Bluewater provided two sets each of a
conventionally borided and deep case
borided high-wear part to an agricultural
machinery manufacturer to compare wear
performance in abrasive crop and soil
conditions. Conventional boriding more
than doubled the expected life of these
parts over heat treating alone. At the point
where the conventional boride layer wore
off, the deep case borided parts still had
quite a bit of boride layer depth present
and did not showmuch signs of wear. Fig-
ure 8 shows the wear surface of the two
components where the shallow borided
part shows significant material loss while
the deep borided component shows very
little material loss due to wear.
Bluewater Thermal Solutions’ custom
designed deep-boriding processes were
successful for each project. The ability to
customize the process for different steel
grades and application requirements can
make boriding a more popular choice to
treat parts exposed to harsh wear envi-
ronments. Deep case boriding enables
producing wear layer depths comparable
to competitive processes such as carbur-
izing, nitriding, thermal spray coatings,
and hardfacing. In addition to having a
comparable wear-resistant depth, boride
layers are much harder than carburized
and nitrided cases, and have similar or
higher hardness than many flame spray
and hardface coatings, while maintaining
better dimensional tolerances than the
coating processes, which add material.
Deep case boriding could be the solution
to wear problems in many applications
where parts are exposed to extreme wear
in harsh operating environments.
HTPRO
References
1. H-J. Hunger and G. Trute, Boronizing to
Produce Wear-Resistant Surface Layers,
Heat Treatment of Metals
, 1994, 2, p 31–39
2. G. Kartal, et al., The Growth of Single
Fe
2
B Phase on Low Carbon Steel Via Phase
Homogenization in Electrochemical Borid-
ing (PHEB),
Surface and Coatings Technol-
ogy
, Vol 206, 7, Dec. 2011, p 2005–2011.
For more information:
Craig Zimmer-
mann is Director-Technical, Bluewater
Thermal Solutions, 414.573.2832 (mobile),
czimmerman@bluewaterthermal.com;
Nick Bugliarello is general manager of
Chicago Plants 1 and 3, 708.410.8000
(plant),
nbugliarello@bluethermal.com,
bluewaterthermal.com.
Fig. 7 —
AISI 4140 alloy steel ground-engaging tools conventionally borided to a depth of
0.004 in. (left) and deep case borided to a depth of 0.010 in. (right). Boride layers in both are
single-phase Fe
2
B.
Fig. 8 —
AISI 1045 plain carbon steel high-
wear agricultural machinery parts borided to
a depth of 0.005 in. (left) and deep case
borided to a depth of 0.014 in. (right). After
service on the same machine for the same
amount of time, the conventional borided
part shows significant material loss due to
wear, while the deep case borided part
shows virtually no wear.