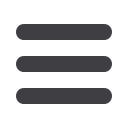
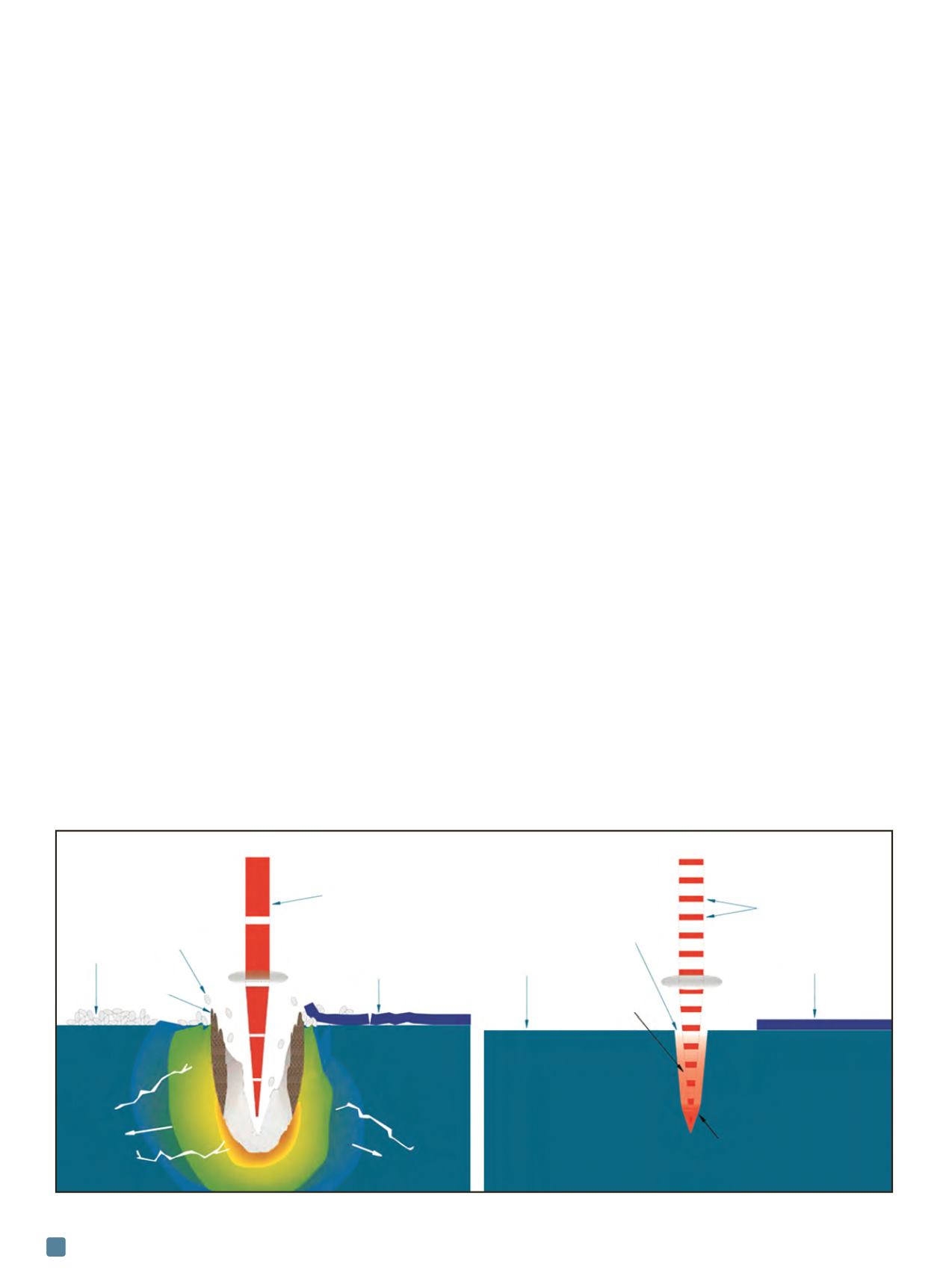
ADVANCED MATERIALS & PROCESSES •
NOVEMBER-DECEMBER 2014
26
M
icrosecond (ms) fiber lasers have been success-
fully used in medical device applications such as
hypo tube and stent cutting for years. While pre-
cise and fast, parts require a number of post processing op-
erations after they are cut, which can damage mechanically
delicate parts and add cost. A new ultra-short femtosec-
ond (fs) laser technology produces pulses that do not leave
a thermal fingerprint on parts. These disk-based femtosec-
ond lasers offer sub-400 fs pulses, high beam quality, and
peak power that enable a high quality cold ablation cutting
process rather than a melt ejection process. Resulting cuts
require minimal post processing and the small beam size
allows machining of very fine details.
The process works well for production of medical de-
vices such as catheters, heart valves, and stents, for med-
ical and glass cutting and marking applications, and
3D-structuring of ceramic material for dental implants.
Perhaps the most interesting potential use involves an en-
tirely new class of bioabsorbable materials—polymers that
safely remain in the body for a certain time before absorb-
ing. They are being developed as an alternative to tradi-
tional polymers or metal parts.
In the past, fs lasers were considered too slow for com-
mercially viable operations. However, recent studies eval-
uated cutting time per part and post processing steps, and
demonstrate a return on investment for a disk femtosec-
ond laser in less than 12 months (in many cases), especially
for high value components. A key aspect of realizing the fs
laser’s potential is the system platform. Two companies
working to address this issue include Jenoptik and Miyachi
America, who are jointly developing both stage and scan
head platforms to achieve new levels of quality and preci-
sion for micro treatment.
Femtosecond laser basics
Femtosecond (fs) light pulses are ultra-short pulses
(USPs). One fs equals 10
-15
seconds and as a calibration
point, a 300 fs pulse equates to a physical pulse length of
only 90 µm. Because there is no thermal processing as
there would be in nanosecond (ns) pulses, USPs offer cer-
tain advantages, including:
• Unchanged material characteristics without
thermal tension
• No shock waves or structural changes
• Smooth processed surfaces without microcracks
• Elimination of melting effects and structural changes
• Surface damage is eliminated and rework or post
processing is not required
• Cleaning is unnecessary and there is no debris
• Clean surfaces due to lack of ejected material
• Smooth edges because there is no recast layer
Figure 1 shows these effects on an application using a
long pulse laser (for example, µs) compared to that of an
ultra-short pulse laser like an fs laser.
Femtosecond laser technology is not new—it has been
widely used in institutions and research centers for more
than 30 years, but commercial fs technology that can en-
dure an industrial environment with 24/7 qualification was
only developed within the last decade. Originally used for
wafer dicing and scribing of P1, P2, and P3 solar panels or
Femtosecond Laser Processing
Overcomes Barriers for Use
in Medical Device Manufacturing
TECHNICAL SPOTLIGHT
Fig. 1 —
Schematic processing comparison of microsecond to femtosecond lasers.
Long pulse
laser beam Ultra-short
laser pulses
Ejected material No recast layer
Surface debris
Damaged surface No debris No damaged surface
Recast layer
Plasma plume
Heat affected zone No microcracking No heat transfer
Microcracking
to surrounding material
No melt zone
Melt zone
Shock waving No shock waving Hot, dense ion/electron soup
Heat transfer to (i.e., plasma)
surrounding material
Application with long pulse laser (µs)
Application with ultra-short pulse laser (fs)