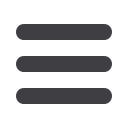
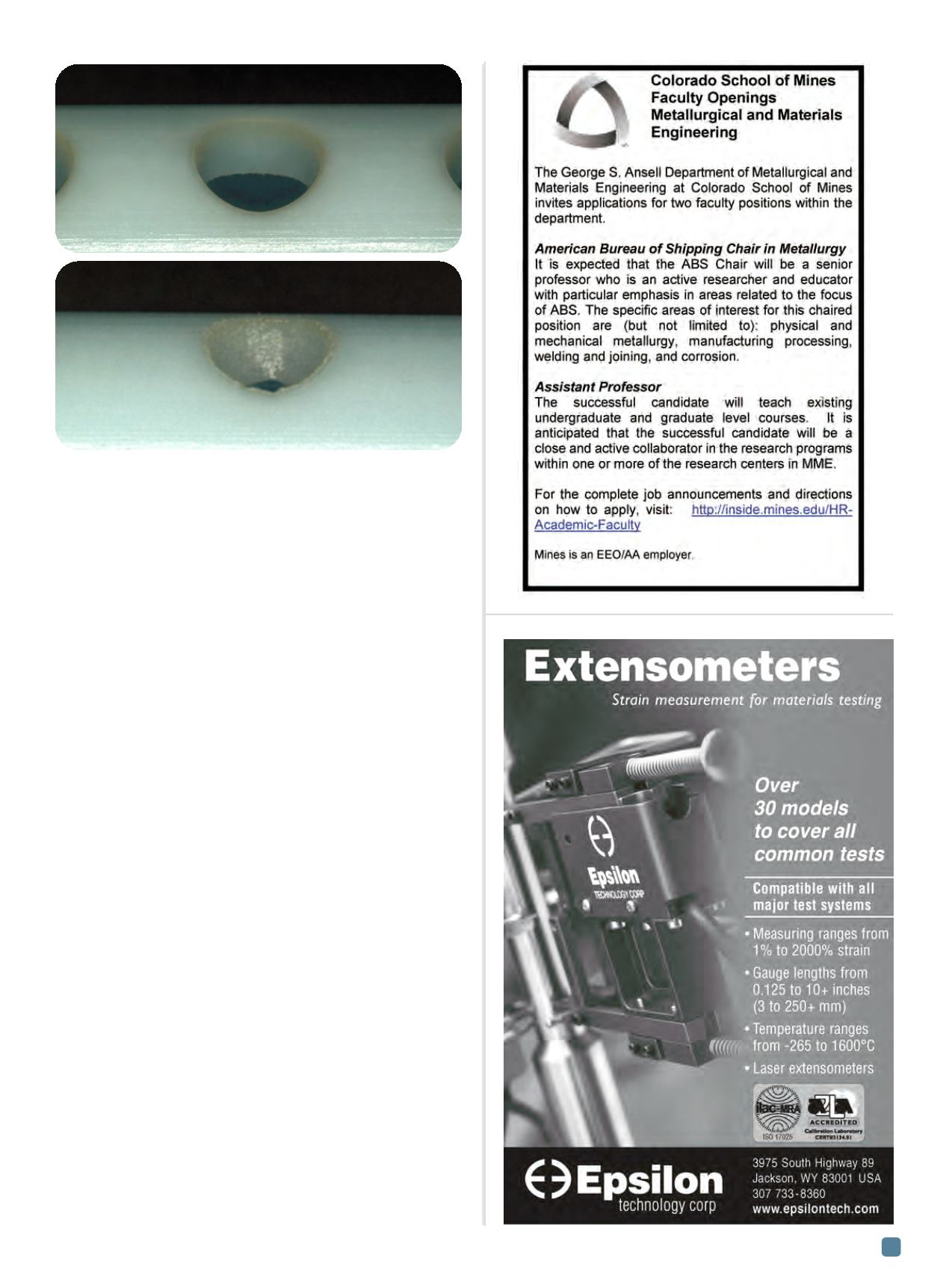
ADVANCED MATERIALS & PROCESSES •
NOVEMBER-DECEMBER 2014
27
creating channels in panels for electrodes, fs lasers are now ad-
vancing into a new wave of machining capabilities, and many
medical devices are suitable candidates given the high cost of
machined components.
In addition to minimized post processing, fs disk lasers
create unique features previously impossible due to quality
concerns, particularly in polymer processing. Figure 2
shows a comparison of a nanosecond 355-nm source and a
1030-nm fs disk laser source processing polypropylene.
The disk fs hole shows little taper, no melting, and no heat
effect distortion around the hole, enabling product design
freedom to maximize functionality without compromising
manufacturing.
Femtosecond lasers for medical devices
The edge quality possible with a femtosecond laser for
both metals and plastics makes it useful for machining heart,
brain, and eye stents (both nitinol and cobalt-chrome),
catheters, heart valves, and polymer tubing. The nearly cold
cutting process allows very fine feature sizes to be cut into
the thinnest material, while maintaining mechanical and ma-
terial integrity. Internal water cooling is unnecessary for even
the smallest diameter nitinol tubes.
Quality improvements and reduced post processing require-
ments have made fs laser technology a promising theoreti-
cal possibility, but until about six years ago there was little
commercial interest in its use for medical devices due to con-
cerns about the expense and slow speed compared to other
technologies. That changed when an ROI tool was developed
to illustrate the true cost of post processing. The tool can be
used to determine overall costs, including laser equipment
purchase, post processing capabilities, and machine and han-
dling time. Calculations demonstrate that femtosecond lasers
are actually faster, because they reduce several time consum-
ing post processing steps.
For example, the coronary stent—one of the first devices to
be manufactured with a fiber laser—must first be machined,
then honed, and finally deburred. A chemical etch process
Fig. 2 —
Comparison of 1030-nm fs disk laser (top) to a 355-nm ns
laser (bottom) when drilling polypropylene.