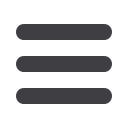
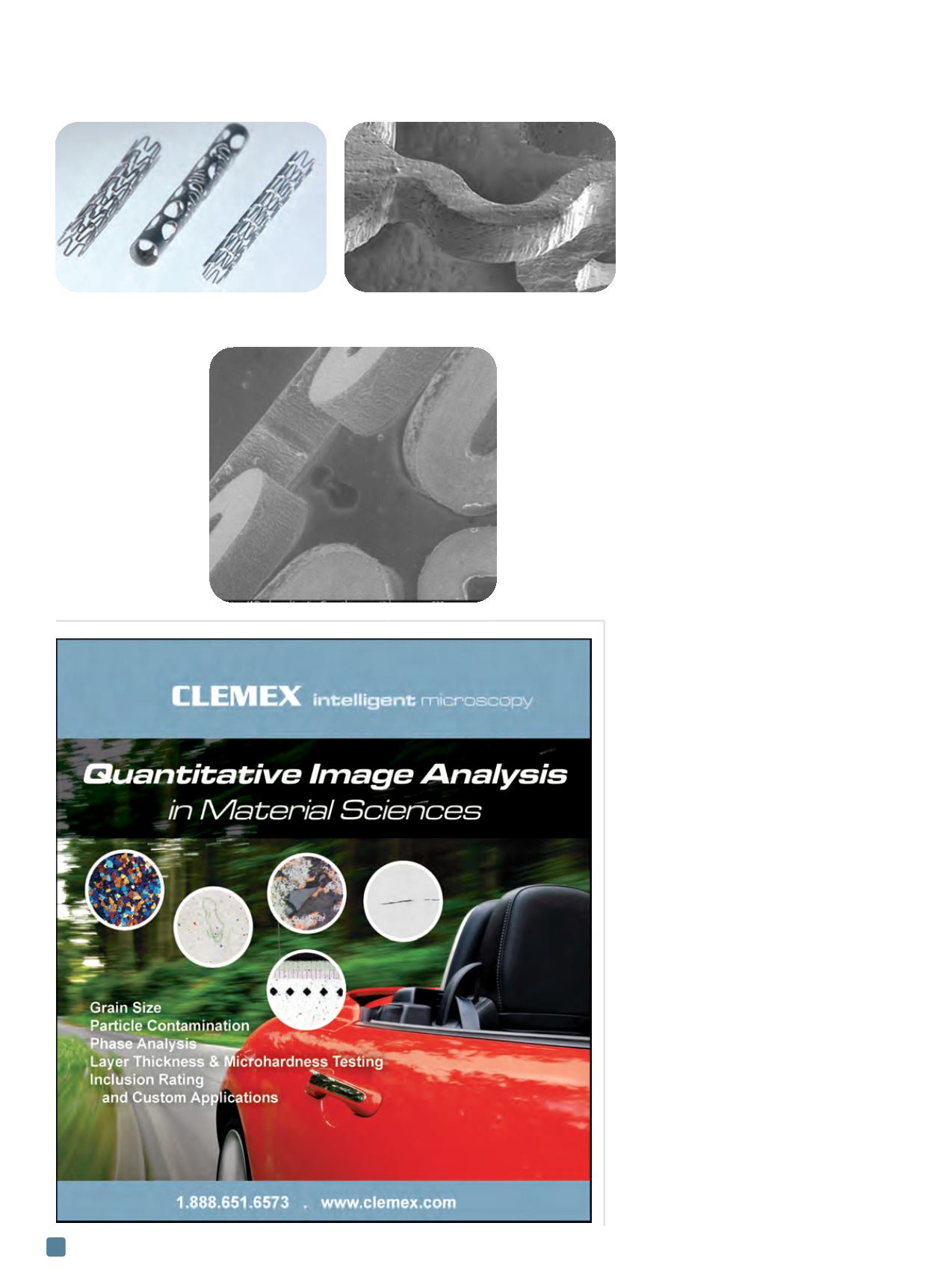
then cleans up around the edges,
followed by electropolishing. These
steps are time consuming and can
also cause the part to become brittle,
deformed, and potentially exhibit mi-
crocracks. Yields are in the 70%
range, with significant loss of end
product.
By contrast, the fs laser is a dry for-
mat—no water or heat is introduced in
the part. The number of steps is drasti-
cally reduced; the part is machined and
then undergoes an electrochemical process to round the
edges. Part integrity is improved, several steps are elimi-
nated, and yields are closer to 95%.
Figure 3 shows the high cutting quality of the fs
laser when working with nitinol stent material. Using
the fs laser prevents burr, and the slight roughness of
the cutting edge achieves a suitable precondition for
the electropolishing process. Removal rate in this ex-
ample is 0.25-5 mm/sec and material thickness up to
400 µm is possible.
Femtosecond laser technology is also the only avail-
able process appropriate for machining medical prod-
ucts out of new bioabsorbable polymers, which can be
safely implanted in the body for controlled lengths of
time before absorbing, without causing
harm or adverse interactions. Next-gen-
eration advanced bioabsorbables (also
called aspirants) provide an alternative
to traditional polymers or metal com-
ponents and are being designed to meet
precise degradation rates and other
specifications.
Bioabsorbable materials can be ma-
chined into any profile used for stents,
but must be processed correctly without
inducing heat. Failure to do so could lead
to crystallization, which degrades the ma-
terial’s structure and lifespan as well as its
ability to dispense medicine at the correct
rate. Also, because bioabsorbables dis-
solve, they cannot be cleaned like most
plastics, and cannot come into contact
with any liquid solutions.
Bioabsorbables are already being
used for coronary stents in the Euro-
pean Union, although they have not
yet received FDA approval for use in
the U.S. Mostly composed of poly-
esters, primarily homopolymers and
copolymers of poly(lactic acid) and
poly(glycolic acid), bioabsorbables are
showing promise for a variety of uses,
including cardio stents for patients
who may have been stented numerous
times and can no longer tolerate a tra-
ditional fixed stent. The material is
ADVANCED MATERIALS & PROCESSES •
NOVEMBER-DECEMBER 2014
28
Fig. 3 —
Cut quality for nitinol stent. Nitinol stents (left). Close-up of a 100-µm-thick nitinol stent
(right). Edges feature the same finish as the material surface.
Fig. 4 —
Disk fs laser
cut of a
bioabsorbable stent.