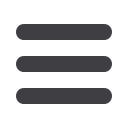

31
ADVANCED MATERIALS & PROCESSES •
NOVEMBER-DECEMBER 2014
of aluminum, compared with 200,000 tons in Ger-
many. Preparing for war drove the German demand.
By 1943, when wartime production reached its peak,
the U.S. produced 835,000 tons against 250,000 tons
in Germany. In addition, Canadian production in-
creased from 75,000 tons in 1939 to 450,000 tons in
1943. Overall production for the five war years
reached 4 million tons in the U.S. and Canada versus
1.4 million tons in Germany.
To meet the increased demand, numerous alu-
minum plants were financed by the U.S. government,
but were built and operated by Alcoa. These plants
included four to produce aluminum oxide, eight to
reduce the oxide to metal, and 10 to manufacture fin-
ished product. These government plants produced
twice the aluminum of the Alcoa owned plants. After
the war, the government plants were sold to Reynolds
Metals Co. and Kaiser Aluminum and Chemical Co.,
ending the Alcoa monopoly that had existed since
1888. With the new aluminum industry, the old sys-
tem of identifying alloys was modified. The new sys-
tem used the 2000 series for aluminum-magnesium
alloys. Thus, 24S became 2024 and remains a major
high-strength alloy, although stronger alloys have
been developed for the most critical applications.
Modern alloy introductions
Aluminum that contains zinc, magnesium, and
copper was originally studied in Germany. Alloys fea-
turing zinc as a major alloying element exhibit very
high strengths, but are prone to crack under stress
when exposed to corrosion. Nevertheless, research
on these alloys was performed at Alcoa and the first
commercial composition was 76S, used for aircraft
propellers in 1940. Later, stress corrosion cracking
was significantly reduced by adding small amounts
of chromium to the alloy. This lead to the commercial
alloy 75S (now 7075), which contains 5.5 % zinc. This
innovative alloy was introduced during WWII as the
structural metal on Boeing’s B-29 Superfortress long-
range bomber. The 75S alloy could be artificially aged
to design strengths of 73,000 psi, while a modified
version with 6.8% zinc (7178) introduced in 1951 can
develop strengths as high as 78,000 psi.
A more recent alloy developed by Alcoa called
7055 contains 8.0% zinc, 2.3% copper,
and 2.0% magnesium, and provides
exceptionally high compression
strength. Strength levels of 90,000 psi
are achieved in plate and 97,000 psi in
extrusions. This strength level is 10%
higher than the best previous alloy
and 25% higher than the original alu-
minum-zinc alloy, 7075, developed
during WWII. In 2002, Alcoa re-
ceived the ASM International Engi-
neering Materials Achievement
Award for the development of 7055.
These latest high-strength alloys
from Alcoa are used on the Boeing
777, with the main structure of the plane constructed
of two basic aluminum alloys. Because they are the
most highly stressed components, the upper wings are
built of 7055 alloy. The lower wings are constructed of
modified versions of 2024, specifically 2224 and 2324.
They have lower impurity content, which improves
toughness. The fuselage is made of 2524, another ver-
sion of 2024 that contains even lower levels of impuri-
ties for greater toughness.
Aluminum has come a long way since its early
days of pots and pans. With the discovery of precip-
itation hardening as a mechanism for increasing its
strength, aluminum now holds a major position in
modern technology as a structural metal with un-
limited use.
*More information on precipitation hardening is in-
cluded in “The Discovery of Strong Aluminum,”
Advanced Materials & Processes,
p 35-36, Aug. 2011.
For more information:
Charles R. Simcoe can be reached at
crsimcoe1@gmail.com.
For more metallurgical history, visit
metals-history.blogspot.com.
The Douglas DC-3, the first successful passenger plane,
was built with 24S alloy, 4% Cu and 1.5% Mg. From 1935
until production ceased in 1945, 18,000 were built for
commercial and military use. Public domain image.
The Boeing B-17 Flying Fortress and nearly all of the
300,000 planes built during WWII used the 24S alloy. The
aluminum industry tripled in output to meet wartime
demand. Public domain image.
The Boeing 777
uses several new
alloys developed by
Alcoa. Alloy 7055
contains 8% Zn,
2.3% Cu, and 2.0%
Mg. Other new
alloys are
modifications of
2024 with lower
impurities. Courtesy
of United Airlines.
The Alcoa Building,
erected in 1953 in
Pittsburgh, was the
first all-aluminum-
clad high-rise, built
to serve as the
company’s
headquarters.
Public domain
image.