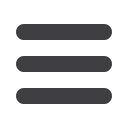
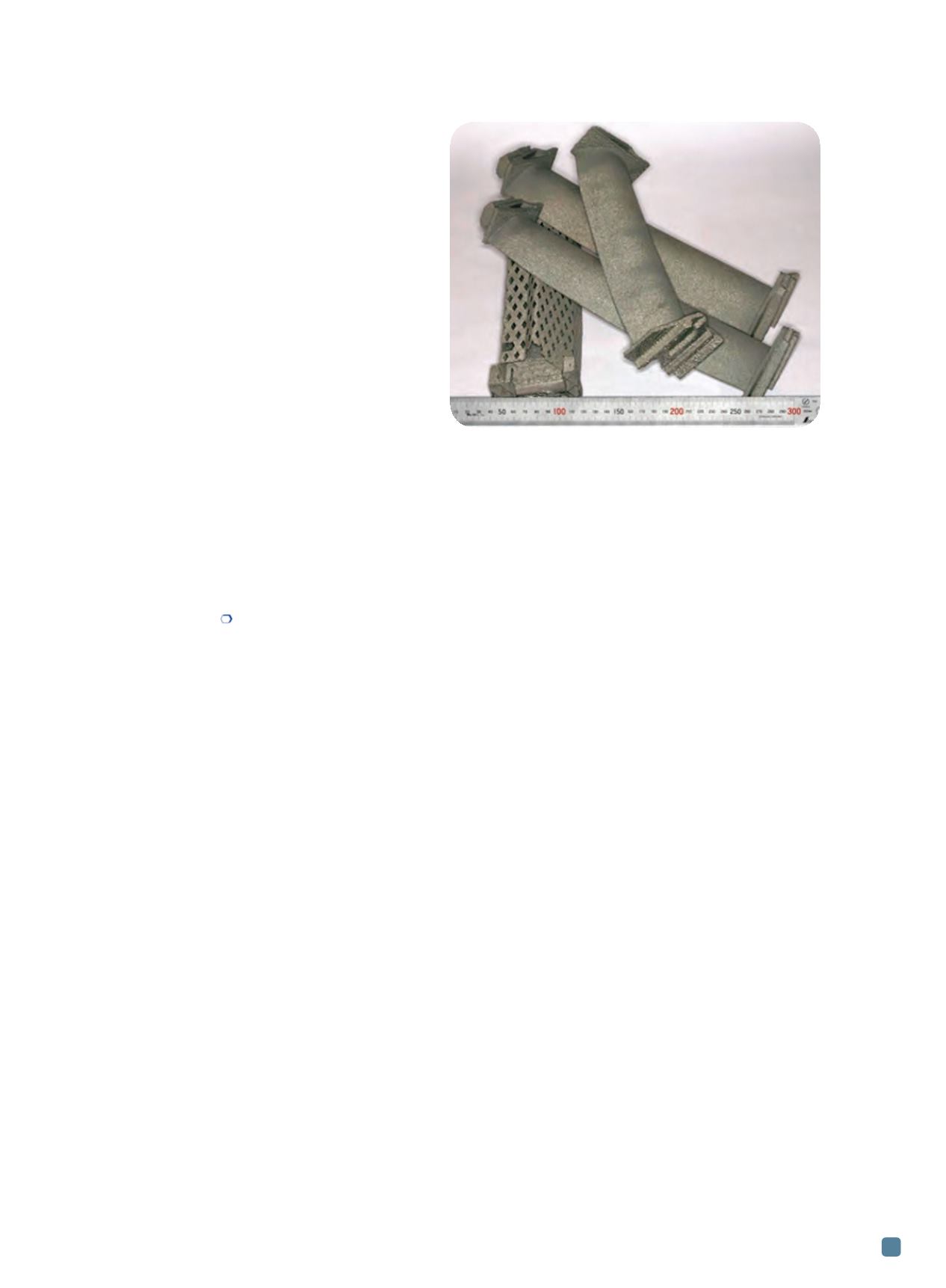
any metal powder, including Ti
2
AlNb, can be used given
that the particle size falls in the specified range and segre-
gation is expected to be minimal. Two major concerns re-
garding AM parts are columnar grains in the build
direction and residual stress due to high solidification
rates. For aerospace, complex AM processes must be de-
veloped to meet stringent property requirements estab-
lished by traditional manufacturing methods such as
casting and forging. One major challenge is to devise a
means of rapidly qualifying AM parts in order to take full
advantage of the compression of production cycle time.
Another challenge is to develop a comprehensive cost
model for this manufacturing process
[24]
. These factors are
just as important to the acceptance of new production
methods as the AM technology itself.
Summary
Introducing any new material is an enormous under-
taking. It is important to realize that it took more than 50
years of research for γ-TiAl to mature before GE Aircraft
Engines introduced it into the low-pressure turbine (LPT)
of GEnx engines, specified in the Boeing 787 in 2005. De-
spite the immaturity of current Ti
2
AlNb alloys compared
to γ-TiAl, they offer a well-balanced property profile as well
as good formability. Over time, further improvements can
be expected with the development of more complex com-
positions and processing.
Acknowledgment
The authors are grateful to Prof. Jim Williams for reviewing
this article.
For more information:
Wei Chen is a senior research scientist
at the Science and Technology on Power Beam Processes
Laboratory, Beijing Aeronautical Manufacturing Technology Re-
search Institute, Beijing 100024, China,
werner_nju@163.com.
References
1. G. Lutjering, J.C. Williams, Titanium, 2nd ed., Springer-
Verlag, Berlin, 2007.
2. C. Leyens, M. Peters, Titanium and Titanium Alloys: Fun-
damentals and Applications, Wiley-VCH Verlag GmbH & Co.
KGaA, Weinheim, 2003.
3. M.J. Blackburn, D.L. Ruckle, and C.E. Bevan. Research to
Conduct an Exploratory Experimental and Analytical Investi-
gation of Alloys, AFWAL, Wright-Patterson, OH, 1978.
4. J. Kumpfert and C.H. Ward, Titanium Aluminides in Ad-
vanced Aerospace Materials, H. Buhl (ed.), Springer Verlag,
Berlin, p 73-83, 1992.
5. D. Banerjee, et al., A New Ordered Orthorhombic Phase
in a Ti
3
Al-Nb Alloy.
Acta Metall. Mater.
, Vol 36, p 871-882,
1988.
6. C.J. Boehlert, et al., The Microstructural Evolution in Ti-
Al-Nb O+Bcc Orthorhombic Alloys,
Met. Trans. A
, Vol 30, p
2305-2323, 1999.
7. A.K. Gogia, High Temperature Titanium Alloys,
Defense
Sci. J.
, Vol 55, No. 2, p 143-173, 2005.
8. D. Banerjee, Deformation of the O and α2 Phases in the
Ti-Al-Nb System.
Phil. Mag. A.
, Vol 72, p 1559-1587, 1995.
9. K. Muraleedharan, et al., Transformations in a Ti-24Al-
15Nb Alloy: Part II, A Composition invariant β/O transfor-
mation.
Met. Trans. A.
, Vol 23, p 417-431, 1992.
10. S.C. Gill and J.A. Peters, Production of Low Oxygen Con-
tamination Orthorhombic Ti-Al-Nb Intermetallic Foil,
Scripta
Mater.
, Vol 35, p 175-180, 1996.
11. D. Banerjee, R.G. Baligidad, and A.K. Gogia, Engineering
Multiphase Intermetallics, Structural Intermetallics, H.J.
Hemker, et al., (ed.), TMS, Warrendale, PA, 2001.
12. H.T. Kestner-Weykamp, C.H. Ward, et al., Microstruc-
tures and Phase Relationships in the Ti
3
Al+Nb System,
Scripta
Met. Mater.
, Vol 23, p 1697-1702, 1989.
13. C.G. Rhodes, Order/Disorder Temperature of the BCC
Phase in Ti-21Al-26Nb,
Scripta Mater.
, Vol 38, p 681-685,
1998.
14. Y. Mao, S.Q. Li, et al., Microstructure and Tensile Proper-
ties of Orthorhombic Ti-Al-Nb-Ta Alloys,
Intermetallics
, Vol
8, p 659-662, 2000.
15. Y.B. Ke, H.P. Duan, and Y.R. Sun, Effect of Yttrium and Er-
bium on the Microstructure and Mechanical Properties of Ti-
Al-Nb Alloys,
Mater. Sci. Eng. A
, Vol 528, p 220-225, 2010.
16. F. Tang, S. Nakazawa, and M. Hagiwara. Effect of Boron
Microalloying on Microstructure, Tensile Properties and
Creep Behavior of Ti-22Al-20Nb-2W Alloy.
Mater. Sci. Eng.
A
, Vol 315, p 147-152, 2001.
17. L. Germann, et al., Effect of Composition on the Mechan-
ical Properties of Newly Developed Ti
2
AlNb-based Titanium
Aluminide,
Intermetallics
, Vol 13, p 920-924, 2005.
18. J.W. Zhang, et al., Research and Application of Ti
3
Al and
Ti
2
AlNb Based Alloys,
The Chinese Journal of Nonferrous Met-
als
, Vol 20, p 336-341, 2010.
19. C.H. Ward, J.C. Williams, and A.W. Thompson, Mi-
crostructural Instability in the Alloy Ti-25Al-10Nb-3V-1Mo,
Scripta Met.
, Vol 24, p 617-622, 1990.
20. C. Leyens, Environmental Effects on Orthorhombic Alloy
Ti-22Al-25Nb in Air Between 650° and 1000°C,
Oxid. Met.
,
Vol 52, p 475-503, 1999.
21. S.G. Warrier, S. Krishnamurthy, and P.R. Smith. Oxidation
Protection of Ti-aluminide Orthorhombic Alloys: An Engi-
neered Multilayer Approach.
Met. Trans. A
, Vol 29, p 1279-
1288, 1998.
22. I. Gibson, D.W. Rosen, and B. Stucker. Additive Manufac-
turing Technology. Springer Science and Business Media,
LLC, New York, NY, 2010.
23. L.E. Murr, et al., Metal Fabrication by Additive Manufac-
turing Using Laser and Electron BeamMelting Technologies,
J. Mater. Sci. Tech.
, Vol 28, p 1-14, 2012.
24. W. Peter, et al., Current Status of Ti PM: Progress, Oppor-
tunities and Challenges.
Key Eng. Mat.
, Vol 520, p 1-7, 2012.
ADVANCED MATERIALS & PROCESSES •
MAY 2014
27
Fig. 6
—
g
-TiAl LPT blades made by EBM additive
manufacturing. Courtesy of Avio S.p.A.