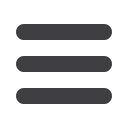
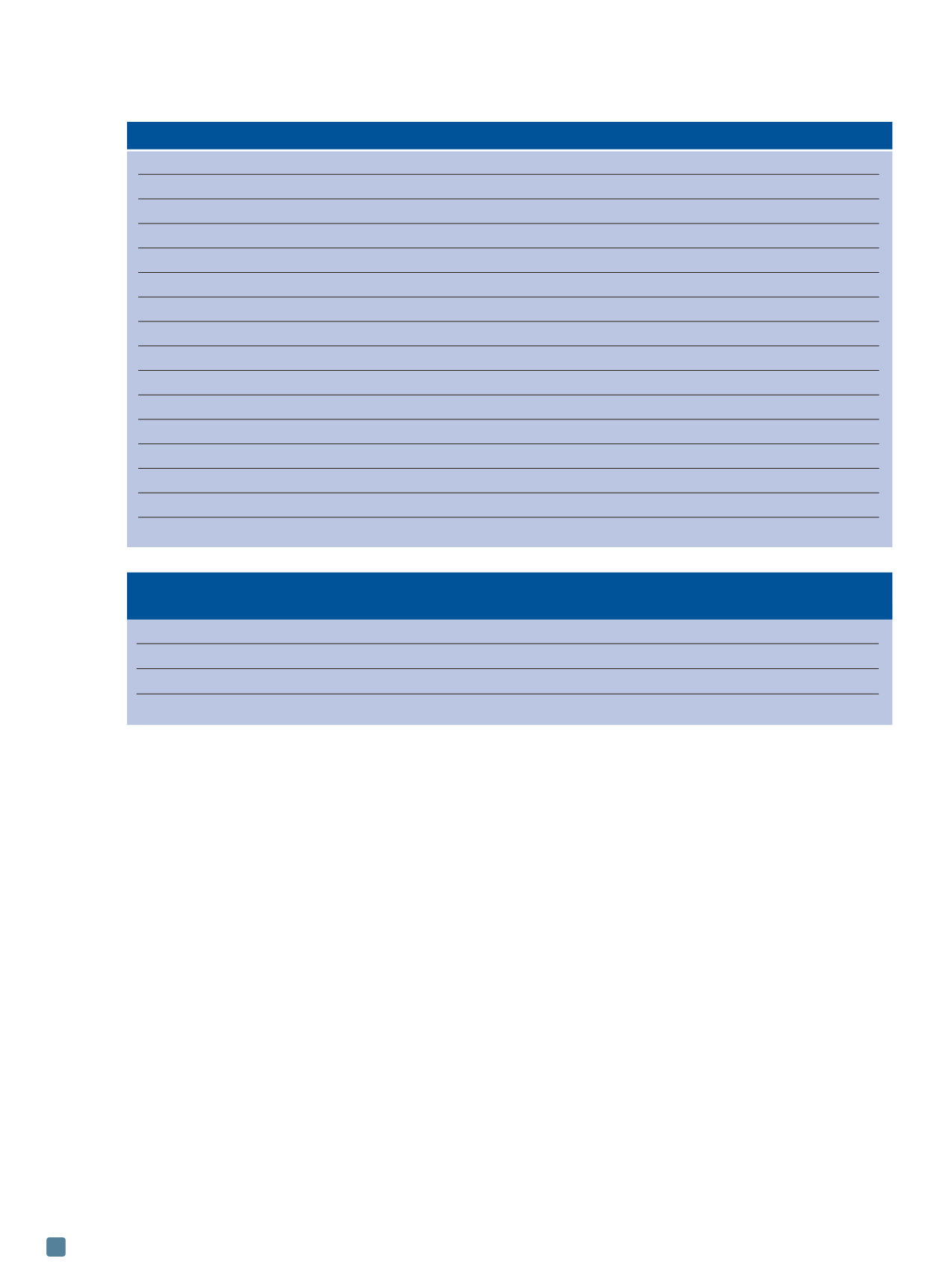
tifies some materials-related issues and introduces an
emerging technology that may affect the future of Ti
2
AlNb.
Materials Development:
In the past 30 years, composi-
tion design has played a significant role in improving the
mechanical properties of Ti
2
AlNb alloys and current ma-
terials offer a balanced set of properties. However, even
with all their attractive properties, Ti
2
AlNb alloys still pres-
ent significant challenges.
Mechanical properties such as high-cycle fatigue
(HCF), low-cycle fatigue (LCF), crack growth, fracture
toughness, and creep behavior of Ti
2
AlNb alloys have been
studied extensively. Table 2 provides an overview of the
pros and cons of Ti
2
AlNb alloys vs. other alloys.
One additional consideration regarding Ti
2
AlNb alloys
is the apparent environmental sensitivity at temperatures
above roughly 550°C. Ward, et al.
[19]
, showed that a Ti-
25Al-10Nb-3V-1Mo alloy exhibits significant, but not
total, ductility loss during tensile testing in air at tempera-
tures of 550° and 650°C. This ductility loss is most severe
when testing at lower strain rates such as 2
x
10
-4
. Testing at
higher strain rates such as 2
x
10
-1
minimized ductility loss,
which is consistent with an environmental effect. It sug-
gests that at high temperatures, oxygen and nitrogen can
dissolve interstitially or form brittle phases in the subsur-
face zone
[20, 21]
, causing early failure of Ti
2
AlNb. This point
was further confirmed by testing in vacuum where the
alloy showed excellent ductility with no significant strain
rate sensitivity. Examples of Ward’s data for tests run at
650°C are provided in Table 3.
While these ductility reductions are not catastrophic,
they are significant enough to require consideration during
design of any component used under these operating con-
ditions. Environmental protective coatings might mitigate
this effect, but the component design still must be robust
enough to function even if the coating is breached during
service. Such a practice is commonly used in cases where
similar environmental sensitivity is encountered.
New Technology:
Additive manufacturing (AM) has
gained increasing attention since 2010 and its advantages
are widely recognized
[22]
. The ability to directly produce in-
tricate shapes is remarkable. Complex shapes have been
made from spherical powder using both laser and electron
beam AM methods
[23]
. These parts are essentially in-situ
castings with high solidification rates. Therefore, the ten-
sile properties—particularly yield strength—of these parts
are expected to be somewhere between those of forging
and larger investment casting.
Avio S.p.A (Turin, Italy) demonstrated the ability to
make γ-TiAl low-pressure turbine blades (Fig. 6) using
electron beam melting (EBM) technology. Theoretically,
ADVANCED MATERIALS & PROCESSES •
MAY 2014
26
TABLE 2 — PROPERTIES OF Ti
2
AlNb VS. Ti ALLOYS AND Ni-BASE ALLOYS
[2]
Properties
Near-
a
Ti
Ti
2
AlNb
g
-TiAl
Ni-base
Density
+
+/-
++
-
HT spec. Young’s modulus
+/-
+
++
+
Coefficient of thermal expansion
+/-
+
-
-
RT ductility
++
++
-
+
Formability
+
+
-
+
Specific HT tensile strength
-
+
+/-
-
Creep resistance
-
+
+
++
Specific RT-HCF strength
+
+
-
+/-
RT crack growth
+
+/-
-
+
RT crack growth threshold
+
+/-
+/-
+/-
RT fracture toughness
+
+/-
-
++
Oxidation resistance
-
+
+
++
HT embrittlement
-
+/-
+
Embrittlement & RT fatigue
-
+/-
+
+
HT: High temperature, RT: Room temperature, HCF: High cycle fatigue
TABLE 3 — EFFECTS OF ENVIRONMENT AND STRAIN RATE ON TENSILE DUCTILITY
OF A Ti-25Al-10Nb-3V-1Mo ALLOY TESTED AT 650°C
Environment
Strain rate
Fracture strain,
e
f
Elongation (%)
R of A (%)
Vacuum
2
x
10
-3
1.24
24.5
70.9
Air
2
x
10
-1
0.94
29.1
60.9
Air
2
x
10
-3
0.18
14.8
16.2