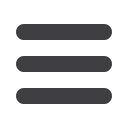
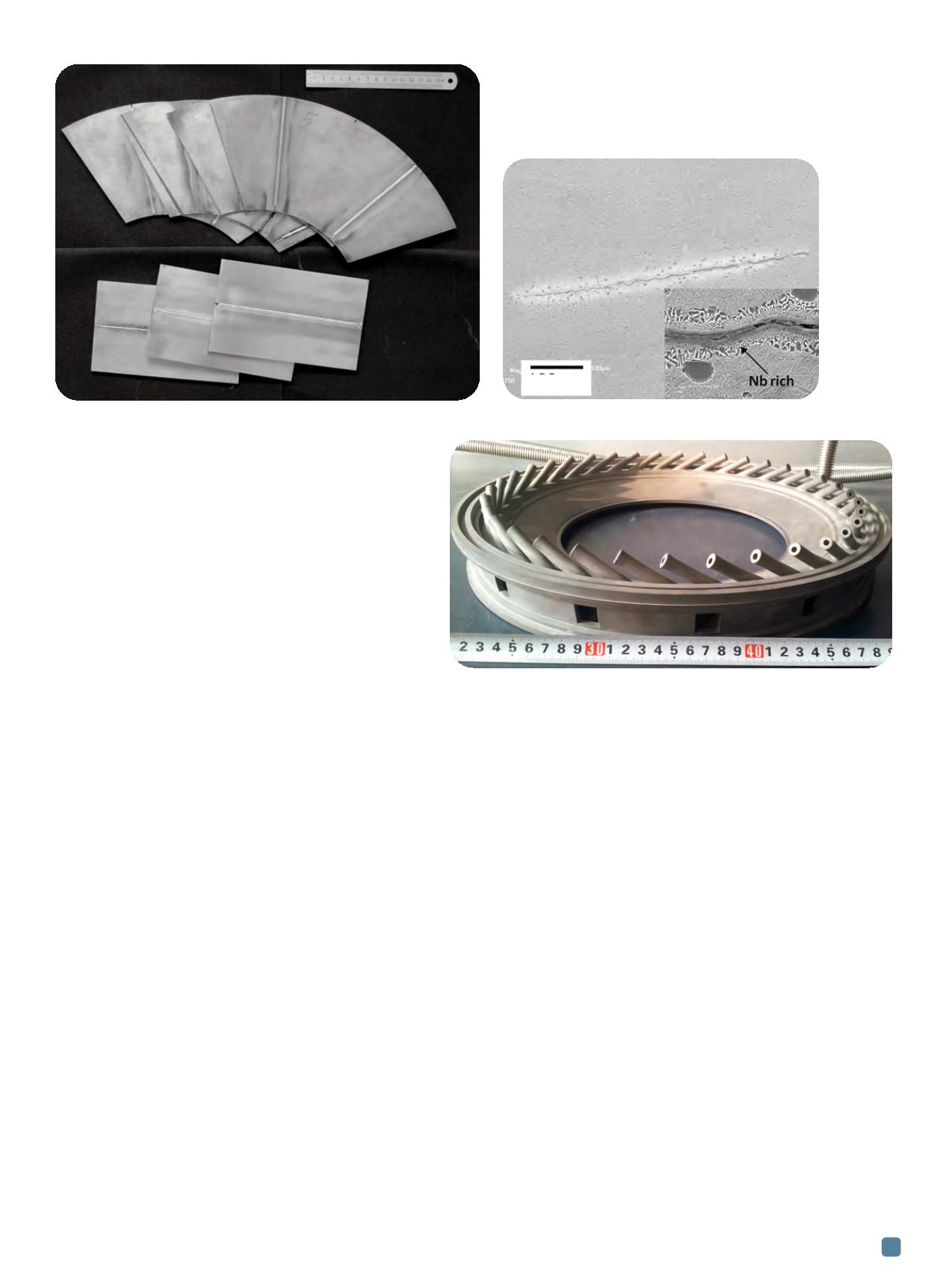
ADVANCED MATERIALS & PROCESSES •
MAY 2014
25
texture. Direct casting of Ti
2
AlNb components has not yet
succeeded, likely due to these problems.
For the casting process, minimizing segregation is ex-
tremely important. Ingot inhomogeneities in both com-
position and microstructure are difficult to remove by
subsequent wrought processing. These inhomogeneities
can easily cause machining cracks during aerospace com-
ponent manufacturing. Figure 4a shows several hot rolled
Ti-22Al-24Nb-0.5Mo sheets after a welding test. This ma-
terial has fairly good weldability, but chemical analysis in-
dicates that the heat affected zone (HAZ) of welds is
prone to crack if Nb segregation happens in this area. As
can be seen in Figure 4b, the embedded picture illustrates
a large crack caused by Nb segregation. The yield stress,
ultimate tensile stress, and elongation of hot rolled Ti-
22Al-24Nb-0.5Mo sheets are 1130 MPa, 1233 MPa, and
7.3% at room temperature; and 845 MPa, 1002 MPa, and
12.5% at 650
o
C, respectively.
Hindustan Aeronautics Ltd. (Bangalore, India) man-
ufactured compressor blades from a Ti-24Al-15Nb alloy
for an experimental gas turbine GTX engine produced
by conventional close-die forging
[7]
. In addition, the Cen-
tral Iron and Steel Research Institute (Beijing, China) re-
ports component blanks made of Ti-22Al-25Nb alloy,
including rings, die-forged blades, and spin-formed com-
ponents
[18]
. However, no other public information about
testing and application of Ti
2
AlNb engine components
has been found.
Powder Metallurgy:
Powder metallurgy (PM) is a long-
standing method of producing Ni-base alloy components
used in turbine engines. The weakness of cast-and-
wrought processing motivated the exploration of PM tech-
nology to produce Ti
2
AlNb products. The advantage of the
PM technique is that high quality, near-net-shape, and ho-
mogeneous parts can be made with substantially reduced
machining and scrap. For high-alloyed materials such as
Ti
2
AlNb, PM methods are far superior to cast-and-
wrought processing for various reasons. These include el-
ement segregation, texture, and residual stress upon
cooling from processing conditions.
Ti
2
AlNb powders are generally too strong to be cold
compacted. They are therefore usually processed by hot
isostatic pressing (HIP) followed by heat treatment. IMR
developed a net-shape PM method for making various Ti
components with complex shapes using pre-alloyed, gas-
atomized powders. Dimensions of the final components
are calculated based on finite element modeling of powder
shrinkage during HIP. This technique has matured to a
state of designing and making aerospace components with
high precision. Figure 5 shows a PM net-shape Ti-22Al-
24Nb-0.5Mo aerospace engine component.
However, PM is no panacea either. Small volume frac-
tions of residual pores (less than several microns in diam-
eter) do not seem to affect tensile properties because
Ti
2
AlNb alloys have adequate ductility to withstand small
internal stress risers, but these same pores can act as fa-
tigue crack initiation sites during cyclic loading. In addi-
tion, weldability is also expected to be degraded by residual
porosity. Investigation of this issue is currently underway.
Opportunities and challenges
The potential for Ti
2
AlNb alloys to reach the engine
components market critically depends on understanding
and tailoring composition, and on subsequent processing
to achieve the required microstructure and mechanical
properties. A few challenges related to Ti
2
AlNb process-
ing were already described. The following discussion iden-
Fig. 4 —
(a) Hot rolled Ti-22Al-24Nb-0.5Mo sheets after welding test, and (b) a crack in the weld HAZ caused by Nb segregation.
(a)
(b)
Fig. 5 —
A PM net-shape Ti-22Al-24Nb-0.5Mo aerospace engine
component.
100 µm