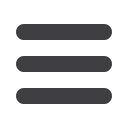
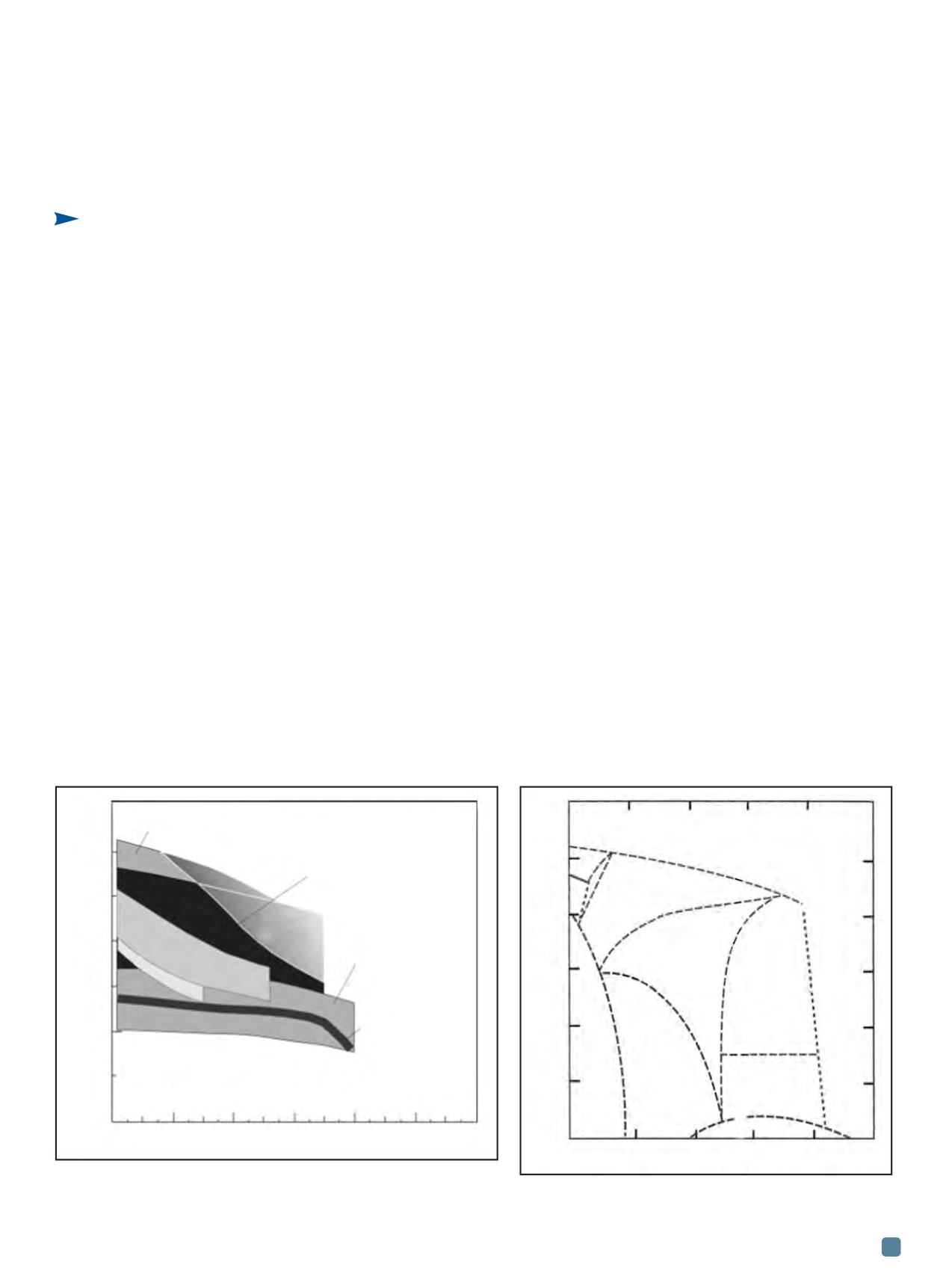
ADVANCED MATERIALS & PROCESSES •
MAY 2014
23
Development of Ti
2
AlNb Alloys:
Opportunities and Challenges
D
uring the past 30 years, enormous re-
search has been devoted to developing
Ti-base intermetallics for use in gas
turbine engines. The driving force was to re-
place Ni-base superalloys (density 8-8.5 g/cm
3
)
with lower-density materials (4-7 g/cm
3
) that
have adequate temperature capability to reduce
weight. Alloys based on the composition
Ti
2
AlNb, often called
orthorhombic alloys,
offer
higher specific strength and better stability
(Fig. 1) than conventional Ti-base inter-
metallics such as TiAl and Ti
3
Al
[1-2]
. (All alloy
compositions based on Ti
2
AlNb will be called
Ti
2
AlNb as a common class of alloy.)
Although the database for Ti
2
AlNb alloys
has been significantly expanded, few applica-
tions exist in aerospace engine production. Fac-
tors are both material and process related. This
article presents a brief history of Ti
2
AlNb and
efforts to mature this material for commercial
component production. The assessment is val-
idated using processing experience gained from
a current R&D program at Beijing Aeronauti-
cal Manufacturing Technology Research Insti-
tute (BAMTRI) and Institute of Metal Research
(IMR) in China.
Alloy design
In the late 1970s, Nb was found to improve
the ductility of Ti
3
Al (α
2
) alloys by stabilizing a
relatively ductile, ordered B2 phase
[3]
. A large
range of alloy compositions has since been exam-
ined and alloys with higher room temperature
ductility and enhanced temperature capabilities
were discovered. One of the most attractive al-
loys was Ti-25Al-10Nb-3V-1Mo (at.%), which
was referred to as “super-α
2
.” (All compositions
are reported in atomic percent in this article.)
Vanadium was added to replace some niobium
for cost and density reduction, while molybde-
num improves high-temperature strength, creep
resistance, and Young’s modulus
[4]
.
In 1988, Banerjee
[5]
first identified the
orthorhombic (O) phase based on the stoichio-
metric composition Ti
2
AlNb in the alloy Ti-
25Al-12.5Nb, which also contained the α
2
and
B2 phases. Because of the attractive properties
associated with alloys containing the O phase,
many Ti
2
AlNb alloys were investigated over the
years. Figure 2 shows the phase diagram of the
Ti-22Al-Nb system. Typical Ti
2
AlNb alloys have
compositions ranging from 20-30 Al and 12.5-
30 Nb. Ti-22Al-23Nb, Ti-22Al-25Nb, and Ti-
22Al-27Nb are among the ternary alloys that
have been mostly investigated.
The processing-microstructure relation-
ship of Ti
2
AlNb alloys is similar to conventional
α/β Ti alloys. A super-transus processing results
in acicular morphology of the α
2
/O phase while
a sub-transus processing results in equiaxed
W. Chen and
J.W. Li
Beijing Aeronautical
Manufacturing
Technology
Research Institute
Beijing, China
L. Xu and B. Lu
Institute of Metal
Research, Chinese
Academy of
Sciences
Shenyang, China
Ti
2
AlNb offers
a well-balanced
property profile
for application
in aerospace
engines to
significantly
reduce weight.
Fig. 1 —
Specific yield strength ranges as a function of temperature for
Ti
2
AlNb alloys in comparison to near-
a
Ti alloys, Ti
3
Al-base alloys,
nickel-base alloys, and TiAl-base alloys
[2]
.
Fig. 2 —
An isopleths of the Ti-Al-Nb phase diagram at a
constant 22Al
[6]
.
0
200 400
600
800
1000
1200
Temperature (°C)
30
20
10
0
Specific yield strength (R
p0.2
/
r
g), (km)
Ti
3
Al
Stable
Ti
2
AlNb
Stable
Limited
stability
Near-alpha-
Ti TiAl
Ni-base (IN718)
Alpha-beta-Ti
0 10
20 30
40 50
Ti-22 at.% Al
Nb composition (at.%)
1200
1100
1000
900
800
700
600
Temperature (°C)
B2
a
+
b
a
+
a
2
a
2
+B2
a
2
+
b
/B2+O
B2+O
a
2
a
2
+O
Order/disorder line
b
+O
O