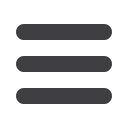
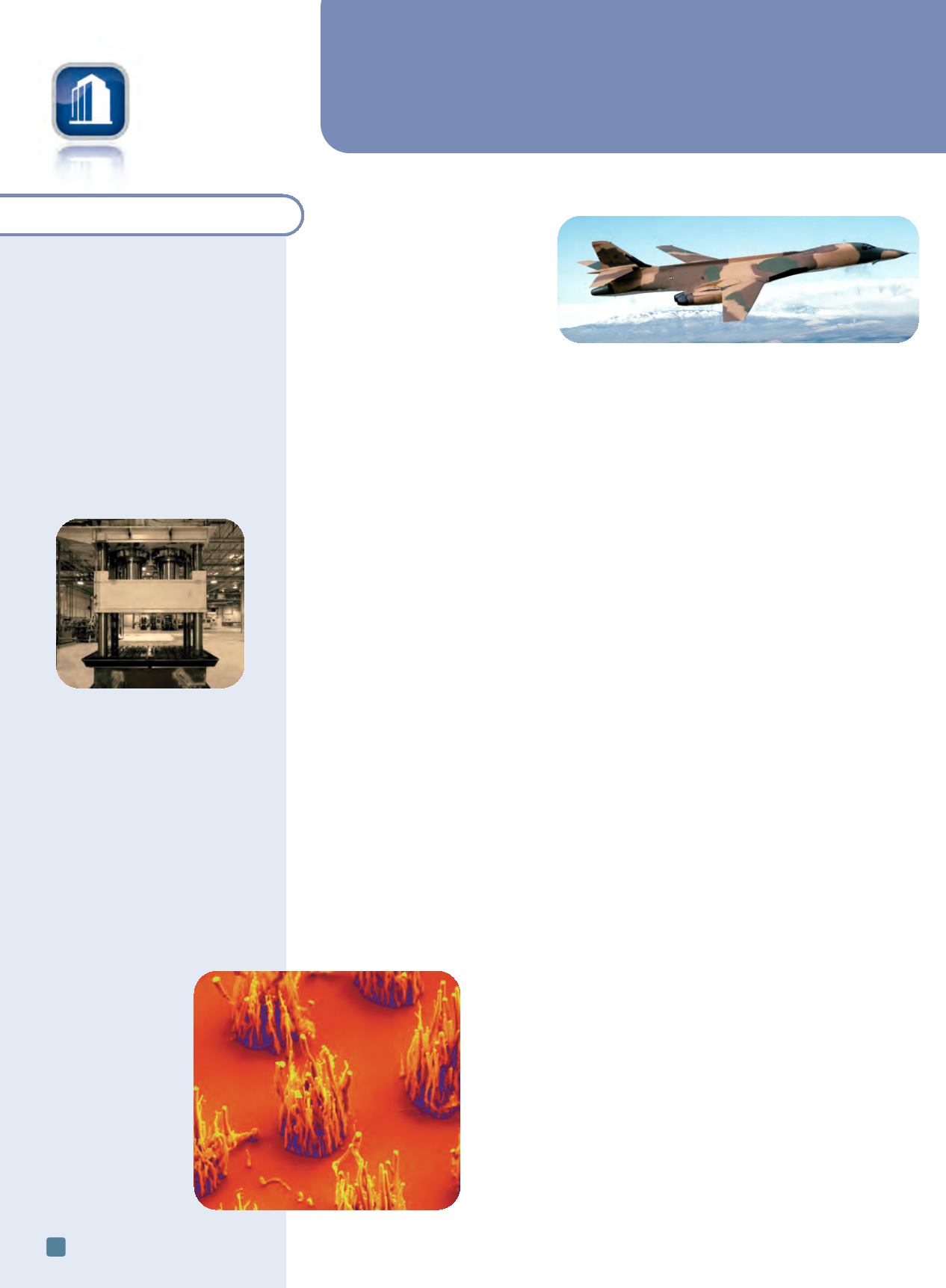
ADVANCED MATERIALS & PROCESSES •
MAY 2014
18
news
industry
briefs
After 23 years of service,
Vari-
Form,
Troy, Mich., announced the
retirement of the first machine to
ever hydroform an automotive
structural part. Production of
instrument panel beams for
Chrysler S body minivans such as
Dodge Caravan began in July
1990. Over time, the press was
used to produce structural parts
for several generations of these
vehicles. Dubbed
“Old Faithful”
by Vari-Form engineers, production
peaked at more than 700,000
units per year in 1996.
www.vari-form.com.
During two decades of active
use, Old Faithful output nearly
10 million units.
Jean-Paul Herteman, CEO of
Safran,
France, and Joseph
Morone, CEO of
Albany
International Corp.,
Rochester,
N.H., inaugurated a new plant in
Rochester that will produce 3D
woven RTM (resin transfer molded)
composite parts for aircraft
engines. The 300,000-sq-ft facility
will make fan cases and blades for
CFM International’s LEAP engine,
dedicated to the next-generation
single-aisle aircraft. Particularly
strong and lightweight,
the 3D parts will help
achieve 15% percent
better fuel consumption
than today’s best CFM
engine.
www.safran-group.com,
www.albint.com.
Cold spray technology restores aging bombers
South Dakota School of Mines
and Technology, Rapid City, and
Ellsworth Air Force Base, Pied-
mont, S.D., signed an agreement
formalizing a relationship for col-
laborative projects such as using
what they call a “revolutionary re-
search technology” to refurbish
aging bombers. The new partner-
ship has already helped return
four B-1s to service and could save the military millions of dollars.
School of Mines faculty researchers in connection with the Army Research Lab devel-
oped a patent-pending process using cold spray technology to deposit aluminum powder
in worn and damaged areas of aircraft panels, machining them back to their original dimen-
sions, thus returning bombers to full service. Panels were nearly impossible to replace with-
out significant cost and time because OEMs no longer produce these 30-year-old aircraft
components.
With proper approvals, $2.5 million could be saved this year alone on the B-1s at
Ellsworth. An emerging technology, cold spray is capable of depositing a wide range of
metal powders to create high-performance coatings on diverse materials without over-
heating them. This technology could be used for similar repairs on other weapon systems,
and also has broad commercial applications.
www.sdsmt.edu.
Scientists build carbon nanofibers with ambient air
Researchers fromNorth Carolina State University, Raleigh, demonstrate that vertically
aligned carbon nanofibers (VACNFs) can be produced using ambient air, making the man-
ufacturing process safer and less expensive. VACNFs hold promise for use in gene-deliv-
ery tools, sensors, batteries, and other technologies, but conventional techniques for
creating them rely on toxic ammonia gas.
“This discovery makes VACNF manufacture safer and less expensive, because there is
no need to account for the risks and costs associated with ammonia gas,” explains Anatoli
Melechko, adjunct associate professor of materials science and engineering. “This also
raises the possibility of growing VACNFs on a much larger scale.”
In the most traditional method to manufacture VACNFs, a substrate coated with nickel
nanoparticles is placed in a vacuum chamber and heated to 700°C. The chamber is filled
with ammonia gas and either acetylene or acetone gas, which contains carbon. When a
voltage is applied to the substrate and a corresponding anode in the chamber, the gas is ion-
ized. This creates plasma that directs nanofiber growth. Nickel nanoparticles free the car-
bon atoms, which begin forming VACNFs beneath the nickel catalyst nanoparticles.
However, if too much carbon forms on the nanoparticles, it can clog the passage of carbon
atoms to the growing nanofibers. Ammonia’s role in this process
is to keep carbon from forming a “crust” on the nanoparticles,
which would prevent formation of VACNFs.
“We didn’t think we could grow VACNFs without ammonia or
a hydrogen gas,” Melechko admits. His team tried the conven-
tional vacuum technique, using acetone gas. However, they re-
placed the ammonia gas with ambient air and it worked. The size,
shape, and alignment of the VACNFs are consistent with those
produced using conventional techniques.
For more information:
Anatoli Melechko, 865/566-2713,
anatoli_melechko@ncsu.edu,
www.ncsu.edu.
Researchers grow vertically-aligned carbon nanofibers using ambient
air, rather than ammonia gas. Courtesy of Anatoli Melechko.
P
ROCESS
T
ECHNOLOGY
Using innovative cold spray technology, aging B-1
bombers are being restored to full service at Ellsworth Air
Force Base. Courtesy of U.S. Air Force.