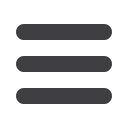
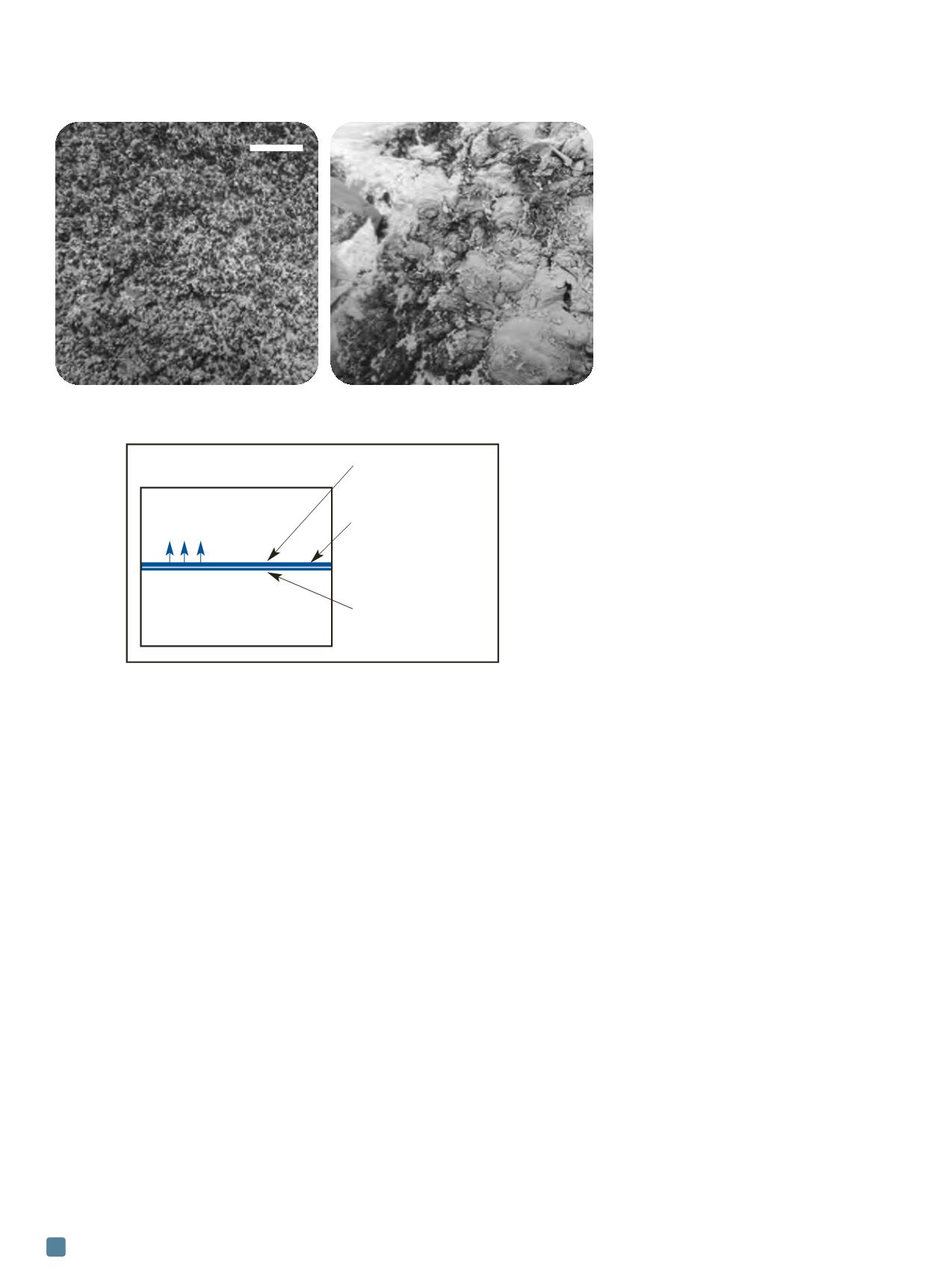
ADVANCED MATERIALS & PROCESSES •
MAY 2014
30
should be explored. It is well documented that minor addi-
tions of reactive elements cause a drastic improvement in
the high-temperature oxidation resistance of these alloys
[4]
.
Because the effectiveness of reactive elements depends on
base alloy chemistry, it is likely that some alloys may con-
tain substantial amounts of reactive elements, but only a
fraction of it is effective in inhibiting oxidation, ignition,
or other forms of surface reactivity. It is reported that a
combination of two or more reactive elements causes a
synergistic effect, substantially increasing their effective-
ness in suppressing ignition. For binary Mg-Y alloys, a sub-
stantial increase in ignition temperature to 900
o
C was
achieved for Y concentrations exceeding 10%
[5]
. That
amount of Y was reduced significantly with Ce additions to
form a Mg-Y-Ce system, which was attributed to a higher
contribution of Y
2
O
3
oxide within the scale. Combining Ca
with Y, and Ag or Be with rare earths, also yields benefits.
Developing nonflammable alloys
The need for nonflammable magnesium alloys, sup-
ported by application opportunities in aerospace, fuels
activities aimed at developing next-generation alloys.
Present commercial grades with improved ignition resist-
ance, such as WE43, ZE41, ZE10, or Elektron 21, were
primarily designed to retain certain mechanical proper-
ties at elevated temperatures. Because they contain rare
earths, ignition and flammability resist-
ance is improved.
A new Mg alloy development direction
contains—in addition to α-Mg—a novel
phase with a long period stacking order
(LPSO) structure
[6]
. The LPSO structure is
formed in the Mg-M-RE system where
M
is represented by Co, Ni, Cu, Zn, or Al, and
RE
are rare earths limited to Y, Gd, Tb, Dy,
Ho, Er, or Tm. The alloy with chemistry of
Mg96.75Zn0.75Al0.5, produced by powder
metallurgy and rapid solidification, reached
an ignition temperature of 780°-940
o
C. As
further progress, Kumadai nonflammable
magnesium alloys were developed, which
consist of C36 type intermetallic com-
pounds, produced by extrusion with a yield
point of 410-460 MPa and an ignition temperature ex-
ceeding 1107
o
C, the boiling point of pure magnesium.
Vital role of surface oxide
Magnesium alloys are not used in typical high-tem-
perature applications and are mostly exposed to high
temperatures during primary melting and at different
stages of the component manufacturing cycle such as
casting, hot forming, or welding
[7]
. The essence of magne-
sium ignition prevention in these processes is to create a
protective barrier layer on the solid or liquid surface, thus
supressing reaction with oxygen. Because conventional
magnesium alloys do not generate protective oxides, they
require protective atmospheres that react with the molten
alloy to form such a barrier.
The phenomena of ignition and flammability are in-
herently related to high-temperature oxidation. In a sense,
onset of ignition is understood as a failure of the protective
oxidation, when surface oxide or other compounds lose
their protective properties. The competing effect of tem-
perature and time during testing of ignition and flammabil-
ity indicates that both phenomena are controlled by the
progress in oxide growth during high-temperature expo-
sures, but before reaching the growth stage when oxide
loses its protective properties due to its morphological
characteristics. As shown in Fig. 3, the morphology of
oxide nodules does not act as a barrier layer, resulting in
magnesium ignition and combustion.
Ignition temperature is not generally correlated with a
presence of the liquid fraction. Although ignition of pure
magnesium may take place in solid state, for the majority
of alloys, it occurs in liquid state. Especially for magnesium
alloys containing reactive elements, the ignition tempera-
ture may be well above the liquidus line. A concern of aero-
space applications is that during in-flight or post-crash fire
scenarios, an aircraft component may experience partial
or complete melting. Because the surface oxide, composed
of pure MgO, does not offer sufficient protection, current
research focuses on modifying its chemistry and mi-
crostructure to suppress oxide diffusivity characteristics
[8]
.
By modifying substrate composition, the integrity and
10 mm
Fig. 3 —
Morphological development during magnesium oxidation and combustion:
(a) MgO oxide nodules formed on Mg-6%Al alloy prior to ignition, and (b) morphology of
combustion product.
(a)
(b)
Fig. 4 —
Schematics explaining suppression of magnesium
ignition and flammability through base alloying and protective
atmospheres of a reactive nature.
Solid protective film
or scale
Reactive gas atmosphere
to form protective
compounds
Base alloying to form
protective oxide (surface
alloying for solid-state
reactions)
Gaseous environment
Solid or liquid Mg alloy