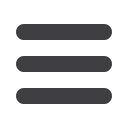
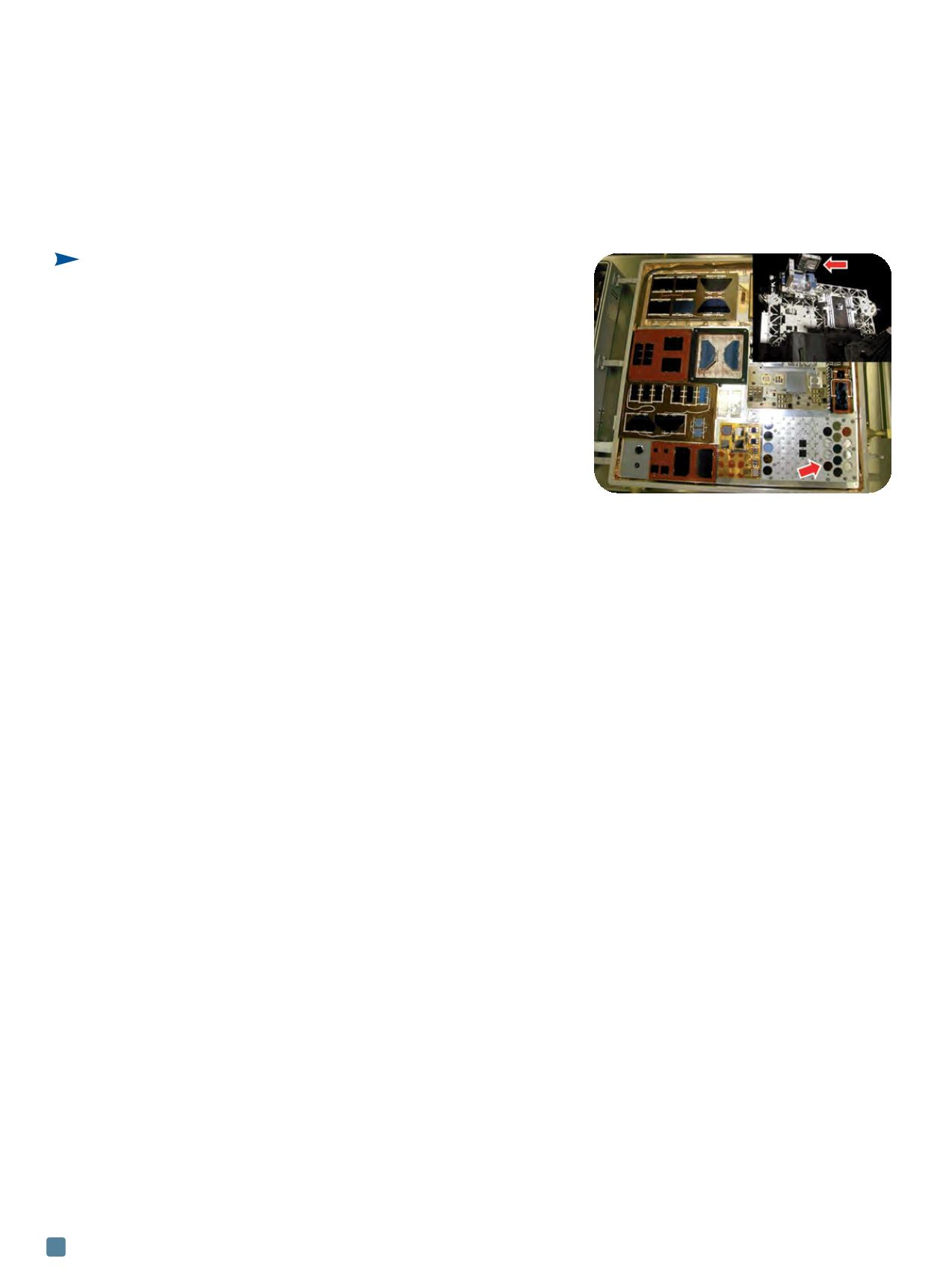
M.T. Dugger*
T.W. Scharf*
S.V. Prasad, FASM*
Materials Science and
Engineering Center,
Sandia National
Laboratories
Albuquerque, N.M.
ADVANCED MATERIALS & PROCESSES •
MAY 2014
32
F
rom the 1960s through the early 1990s,
large government investments in space
exploration by both the U.S. and the for-
mer Soviet Union emphasized performance,
while factors such as cost and aging require-
ments were secondary. Spacecraft were
launched soon after they were completed and
tested, and traveled for relatively short mis-
sions. With today’s increased commercial and
military use of space, performance is still the
primary factor, but satellites may spend signif-
icant time awaiting launch opportunities. Mis-
sions often require longer time periods than
early exploration, so lubricants are expected to
perform in space for years rather than days or
weeks, and must do so after operating and
being stored in terrestrial environments for
months or years. While there have been several
notable missions within the solar system, many
space missions remain near Earth. Among
these missions are those associated with the In-
ternational Space Station (ISS), and polar-or-
biting satellites for Earth observation, in an
environment known as low earth orbit (LEO).
LEO corresponds to altitudes of roughly
200 to 1000 km. Objects in orbit experience
thermal cycles associated with cyclic sun expo-
sure and radiative heat transfer to space as well
as solar UV exposure, which can degrade poly-
meric materials. However, the primary element
present in LEO is atomic oxygen (AO)
[1]
. AO is
created by photodissociation of oxygen mole-
cules in the upper atmosphere by UV radiation
from the sun
[2]
. At orbital velocities near 8 km/s,
AO has energy of approximately 5 eV/atom and
flux density of 10
13
-10
15
atoms/cm
2
.s, depending
on altitude
[3]
. At this energy, AO can break bonds
and induce chemical reactions with many mate-
rials, posing a concern for long-term degrada-
tion of materials in LEO.
Satellite components—specifically those
designed for mechanical hold and release func-
tions—rely on solid lubricant coatings to miti-
gate adhesion, friction, wear, and debris
generation. Thin film solid lubricants have been
investigated for use in space for almost 30
years. Some of their advantages include lack of
migration, which eliminates extra mass associ-
ated with lubricant delivery and containment
systems, consistent frictional behavior from
cryogenic temperatures to hundreds of degrees
centigrade, and lack of velocity dependence on
friction coefficient over a wide range of sliding
speeds. Even with these advantages, space sys-
tems designers are hesitant to employ new ma-
terials without some flight history and an
understanding of how the space environment
impacts these materials.
This article considers the effect of AO ex-
posure on thin film solid lubricants of molybde-
num disulphide (MoS
2
) and diamond-like
carbon nanocomposites (DLN), a silica-con-
taining diamond-like carbon film. Advances in
deposition methods over the past few decades
enable dense films to be created that are more
resistant to oxidative degradation and the ef-
fects of adsorbed moisture than their predeces-
sors. Further, incorporating additional phases
improves the films’ tribological performance in
a range of atmospheres.
MoS
2
films
Sputtered thin films of MoS
2
were first ex-
posed to atomic oxygen in LEO as part of the
NASA Evaluation of Oxygen Interactions with
Materials-3 (EOIM-3) experiment during the
STS-46 mission aboard the shuttle Atlantis,
launched July 31, 1992
[4]
. The total AO fluence
for EOIM-3 was estimated to be 2.2 to
2.5×10
20
atoms/cm
2
over a period of 42.25
hours. The specimens also experienced an es-
timated 22±4 equivalent solar hours of UV ex-
posure. The tray reached a temperature of
Materials in Space:
Exploring the Effect of Low Earth Orbit
on Thin Film Solid Lubricants
Challenges
facing
materials used
in space have
not changed
significantly
over the past
few decades,
but today’s
requirements
have a
different focus
than those
used in the
heyday of
space
exploration.
This article
considers the
effect of
atomic oxygen
exposure on
thin film solid
lubricants.
*Member of ASM International
Fig. 1
—
MISSE-7 solid lubricant films (denoted by
red arrow) placed in a “suitcase-style” passive
experiment container (PEC) mounted externally on
the ISS (shown in inset with red arrow pointing to
the PEC). Courtesy of NASA.