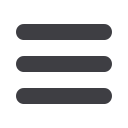
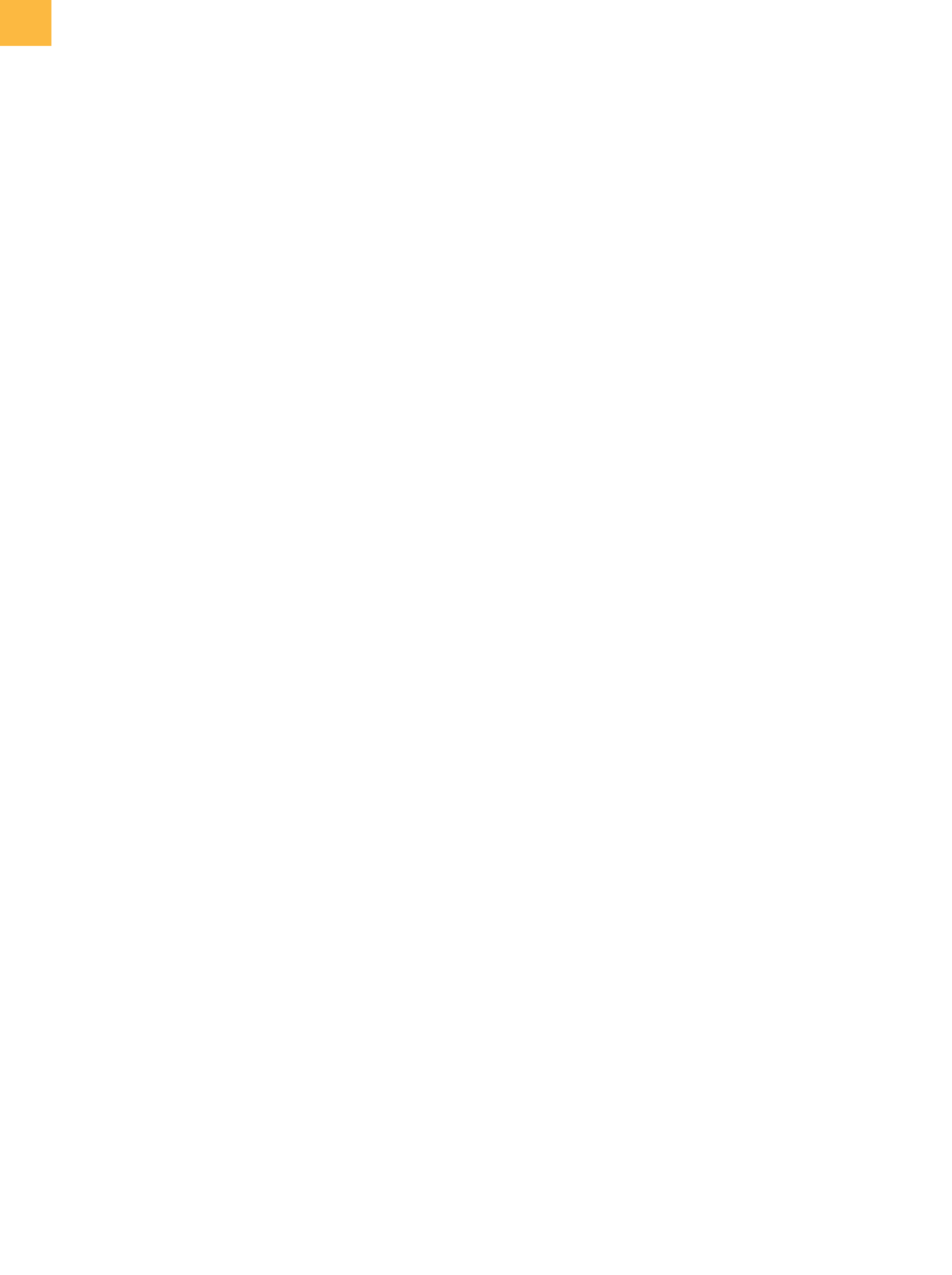
ELECTRONIC DEVICE FAILURE ANALYSIS | VOLUME 18 NO. 1
22
WIRE BONDING
Lee Levine, Process Solutions Consulting, Inc.
levilr@ptd.netEDFAAO (2016) 1:22-28
1537-0755/$19.00 ©ASM International
®
T
he dominant process for interconnecting semicon-
ductor chips to the outside world is an ultrasonic
welding process called wire bonding. More than
90% of the chip interconnections produced annually
(more than 15 trillion wires) are produced with this
process. Welding is a process where an intermetallic
alloy is formed from thematerials to be joined. Generally,
intermetallic alloys are stronger and alsomore brittle than
their constituents. Welding is superior to other joining
methods such as soldering, which requires that a low-
melting-temperaturematerial melt and solidifywithin the
joint. Low-melting-temperaturematerials such as solders
have significantly lower strength and are more subject
to creep and fatigue failures than intermetallics. There
are two major variations of the wire bonding process:
ball bonding and wedge bonding. Ball bonding is the
larger portion, with approximately 90% of the entire wire
bonding market. The fastest ball bonders can bondmore
than 20 wires/second compared to less than 10 wires/
second for wedge bonding. Ball bonding also has more
advanced capabilities than wedge bonding. However,
ball bonding is limited to wires below approximately
50 µm indiameter. All interconnections that require larger-
diameter wire are produced bywedge bonding aluminum
or copper, using either round wire or ribbon (a flattened
form of round wire).
During the past 5 years there has been a major transi-
tion in our industry from ball bonding with gold wire to
the use of copper, palladium-coated copper, or silver wire.
This year will be the first year wheremarket share for gold
wire falls below 50%. Cost, yield, and reliability have all
played a major part in this transition. In 2009, when gold
rose in price above $1000/troy ounce and remained there,
gold reduction became a mandate in semiconductor
packaging. Gold wire represented a large portion of the
gold used in semiconductor packaging. Copper had been
discussed
[1]
and demonstrated since the early 1980s but
had not been widely adopted. Copper was more difficult
to bond and had package reliability issues. As these issues
(optimumbondpadmetallization, encapsulation chemis-
try for long-termreliability, bonder recipe improvements)
were resolved, the transition became a stampede and in 5
years became a newparadigm. Silver is also less expensive
than gold. Silver is used for bonding light-emitting diode
devices because it has better reflectivity properties than
either copper or gold. Early problems with silver wire in
85 °C/85% relative humidity testing were resolved using
silver-palladium alloy wire. Silver market share is now
approaching 10%.
Figure 1 is a photo of the bond head with capillary,
wire, and electronic flame-off (EFO) wand. Inball bonding,
the tip of a fine-diameter metallic wire (protruding from
the capillary) is melted by a spark from the EFO. Surface
tension in themetallic liquid pulls the liquid into a sphere;
the sphere solidifies, withmore than80%of theheat trans-
ferring back into thewire. This leaves a short region above
the ball, called the heat-affected zone (HAZ), that has been
rapidly heated to just below themelting temperature and
then cooled rapidly to near room temperature. The HAZ
is the weakest portion of the wire. The bond head, with
capillary and ball dangling below it, descends at high
speed toward the surface (normally the bond pad on a
die). At a programmed height above the surface, the bond
pad velocity transitions to a slower, constant velocity,
and the bonder begins searching for the surface (surface
height can vary due to the many tolerances from mate-
rial and prior operations). Surface detection can occur by
a number of methods, including mechanically opening
a contact spring, as in older machines, or high-speed
sensing of a current rise in a voice coil motor when the coil
stalls on contact. After contact detection, the bond head
continues downward to apply a programmable force on
the ball. Ultrasonic energy froma piezoelectric transducer
is added for a programmable time (8 to 12ms is typical for
a high-speed ball bonder). The die and substrate are nor-
mally heated to 125 to 200 °C, depending on the process
andmaterials. These four factors—ultrasonic energy, bond
force, heat, and time—constitute the principal variables
for ultrasonic weld formation.
After completing the ball bond cycle, the bond head
rises and a series of very precise coordinated motions
occur, forming a loop between the ball bond and the
second bond. Loop height and uniformity are very